Get a Free WorkTrek Demo
Let’s current you the way in which WorkTrek will enable you to optimize your repairs operation.
Try freed from cost
Maintenance is important to retaining any facility or gear working simply. Many corporations nonetheless use reactive repairs, fixing points solely after they break down.
Nonetheless there’s a larger technique. Proactive repairs will assist cut back repairs costs by as a lot as 70%.
By switching to proactive repairs, corporations can avoid dear breakdowns, lengthen gear life, and improve effectivity.
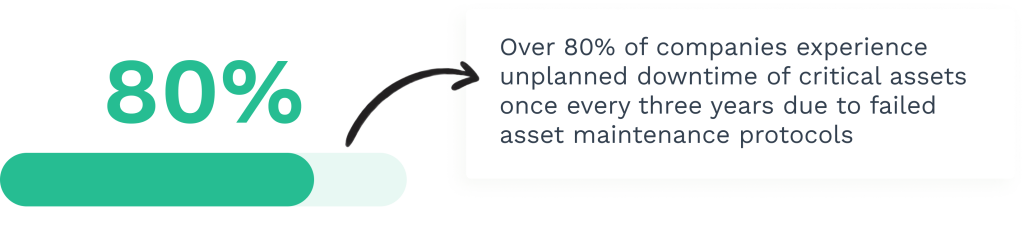
Making the change to proactive repairs isn’t always simple. It takes planning and dedication, nonetheless the benefits are value it.
This submit will uncover seven strategies to maneuver within the route of a further proactive technique and strategies to transition to a proactive repairs method. The following advice help repairs teams catch points early and maintain points working simply.
Key Takeaways
- Proactive repairs can get financial financial savings and improve gear reliability
- Altering to a proactive technique requires planning and workforce buy-in, along with implementing a proactive repairs custom
- Info analysis and staff teaching are key to worthwhile proactive repairs
What exactly is proactive repairs?
Proactive repairs is a way for stopping gear failures sooner than they occur. It identifies and addresses potential factors early reasonably than prepared for breakdowns for very important belongings.
This technique consists of various key methods:
Proactive repairs offers many benefits:
- Extended gear lifespan
- Improved asset reliability
- Diminished downtime risk
- Lower operational costs
- Enhanced vitality effectivity
- Optimizes repairs belongings
Not like reactive repairs, which fixes points after they happen, proactive repairs takes movement upfront. It appears for hidden factors that may set off future failures, reducing unplanned downtime.
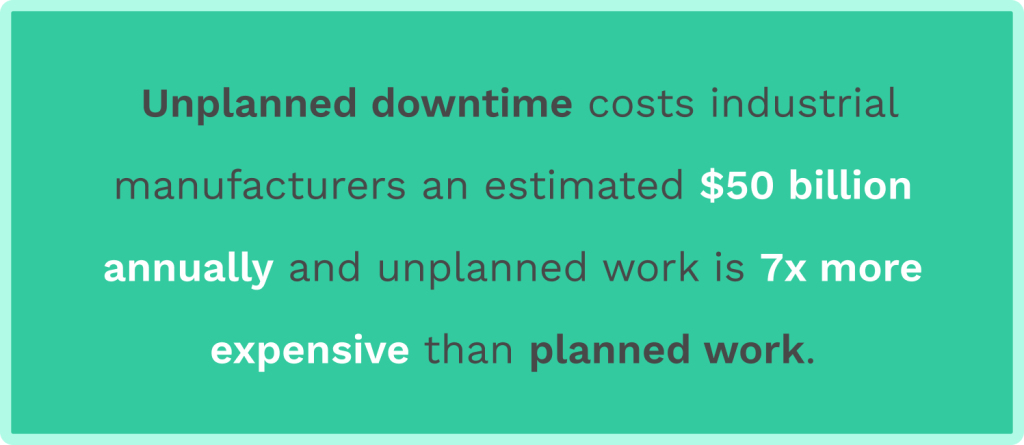
Some examples of proactive repairs duties embody:
- Checking pipes for corrosion indicators
- Lubricating machines often
- Monitoring automotive tire tread depth
By shifting from reactive to proactive strategies, organizations can get financial financial savings and improve operations in the long run. This alteration requires cautious planning and a dedication to ongoing repairs actions.
Proactive repairs simply is not a one-size-fits-all decision. For lots of corporations, a hybrid or mixed technique is essentially the most appropriate alternative.
The goal is to look out the exact stability between proactive and reactive methods for every little bit of equipment.
The Concept of Proactive Maintenance
Proactive repairs targets to forestall gear failures sooner than they happen. It’s a way that focuses on determining and fixing potential factors early.
This technique differs from reactive repairs, which solely addresses points after they occur. Proactive repairs entails widespread inspections, testing, and preventive actions.
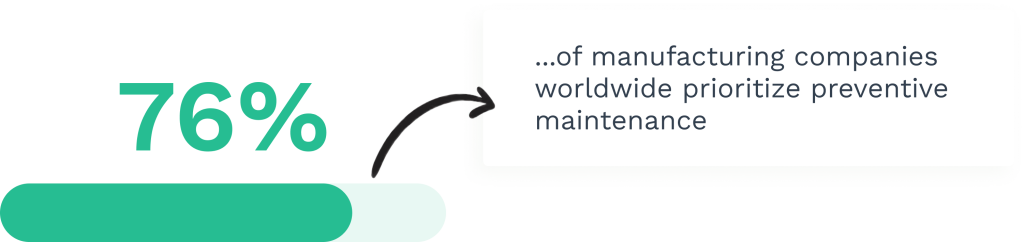
Key components of proactive repairs embody:
Companies can cut back emergency repairs and lengthen gear life by implementing proactive repairs.
Proactive repairs helps organizations:
- Lower downtime
- Lower restore costs
- Improve safety
- Improve gear reliability
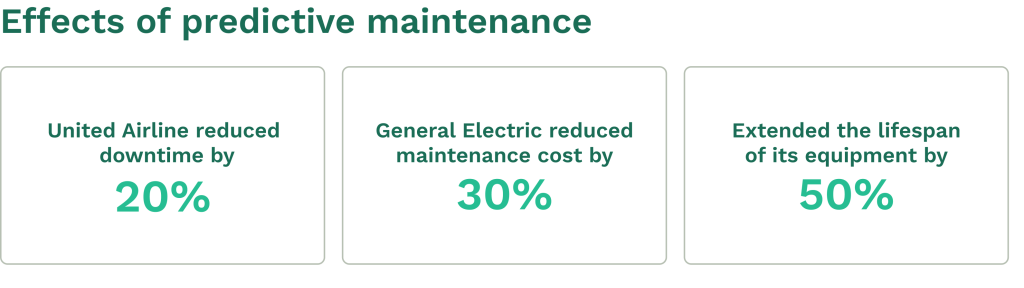
To undertake this system, corporations must create a faithful repairs workforce and spend cash on right devices and training.
Method to Transition to Proactive Maintenance
Transitioning from reactive to proactive repairs requires a shift in mindset and processes. It entails analyzing data, planning, and taking preventive movement.
Worthwhile proactive repairs is determined by good communication between departments and a dedication to regular enchancment.
Seven Strategies for Implementing Proactive Maintenance
Shifting to proactive repairs requires a centered technique. Key strategies embody rising predictive methods, using know-how for monitoring, and setting up a gifted workforce.
1. Develop a Predictive Maintenance Program
Predictive repairs makes use of knowledge to establish factors sooner than they set off breakdowns. Start by setting benchmarks for normal gear operation. Observe elements like vibration, temperature, and noise ranges.
Subsequent, create a schedule for regular checks. Use sensors and meters to collect data all through these checks. This data helps predict when elements might fail.
Analyze earlier breakdowns to look out patterns. Seek for indicators that preceded failures. Use this information to make increased predictions.
Organize alerts for when readings go exterior common ranges. This allows quick movement sooner than points develop. Consider and exchange this method often based mostly totally on new data and outcomes.
2. Benefit from Know-how for Scenario Monitoring
Scenario-based monitoring (CBM) permits repairs teams to judge asset effectively being in real-time in its place of solely on fixed schedules.
Stylish tech makes monitoring gear effectively being easier. Arrange sensors, akin to IoT Items, on key machines to measure important elements.
These might embody:
Be a part of these sensors to a central system computerized repairs administration system (CMMS) like WorkTrek to collect and analyze real-time data.
Use repairs administration software program program to establish tendencies and predict factors, reducing sudden gear failures.
Many packages use AI to boost accuracy over time and improve repairs operations. Mobile apps let staff take a look at gear standing and historic effectivity data from anyplace.
Put cash into devices like thermal cameras and ultrasonic detectors when implementing a proactive repairs program.
These help uncover hidden points all through inspections.
Observe staff on recommendations on use and interpret the outcomes from these devices.
3. Assemble a Professional Maintenance Workforce
A strong workforce is important to proactive repairs success. Start by assessing current staff talents and determining gaps in information or experience.
Prioritizing Staff Education
Staff education ought to offer consideration to proactive repairs strategies. This consists of instructing methods to find out potential gear factors sooner than they set off breakdowns. Teaching packages can cowl issues like:
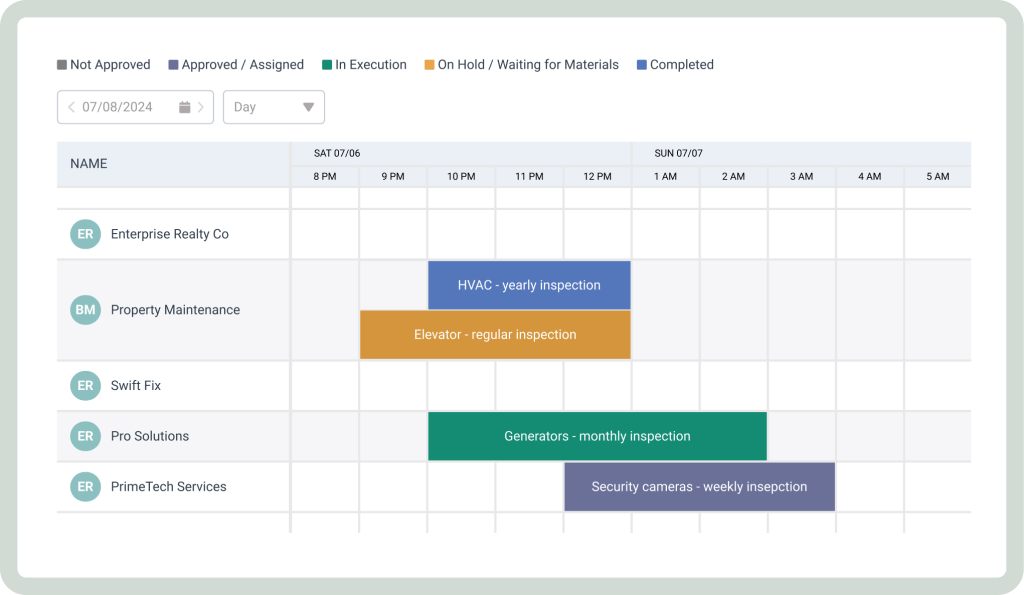
Arms-on workshops allow staff to use new methods in a managed setting, setting up confidence and competence in making use of proactive methods.
Frequent refresher applications maintain talents up-to-date as know-how evolves. On-line finding out platforms present versatile selections for ongoing education.
Create a training plan to fill these gaps.
Cowl issues like:
Encourage staff to get certifications in associated areas to boost present repairs processes and kit effectivity.
This builds expertise and motivation in your proactive repairs efforts.
Organize mentoring packages to share information between expert and new workforce members.
Comprise repairs staff in planning and decision-making. Their hands-on experience is efficacious, and this will help them actually really feel invested inside the new technique.
Foster a practice of regular finding out.
Sustain-to-date with new repairs methods and utilized sciences. Reward staff who advocate enhancements or spot factors early.
4. Conduct Frequent Instruments Assessments
Frequent checks help spot factors early. Use a mix of seen inspections and knowledge analysis to seek for indicators of damage and tear, unusual noises, or modifications in effectivity.
Create a tips for every little bit of equipment. Embody objects like oil ranges, belt stress, and filter conditions.
Observe repairs division staff to make use of those checklists accurately.
Info analytics devices can predict when elements might fail, serving to to plan replacements sooner than breakdowns occur.
Maintain detailed information of earlier factors and repairs. Use this information to boost future repairs plans.
5. Arrange Setting pleasant Workflows
Clear processes make repairs duties smoother. Start by mapping out each step of typical repairs jobs.
Seek for strategies to chop again wasted time or effort to lower repairs costs.
Use CMMS software program program like WorkTrek to hint work orders and elements inventory.
This helps avoid delays as a consequence of missing devices or offers. Organize a system to prioritize duties based mostly totally on gear significance and urgency.
Observe technicians in best practices for each exercise.
Create easy-to-follow guides with footage or films. This ensures fixed prime quality of labor all through fully completely different shifts or teams.
When attainable, schedule routine duties all through deliberate downtime.
Group comparable jobs collectively to save lots of numerous time. Always go away room inside the schedule for sudden factors.
6. Leverage Maintenance Info
Maintenance teams accumulate machine data, along with temperature, vibration, and oil ranges. AI and superior analytics can uncover patterns on this data and predict when a machine might break down rapidly.
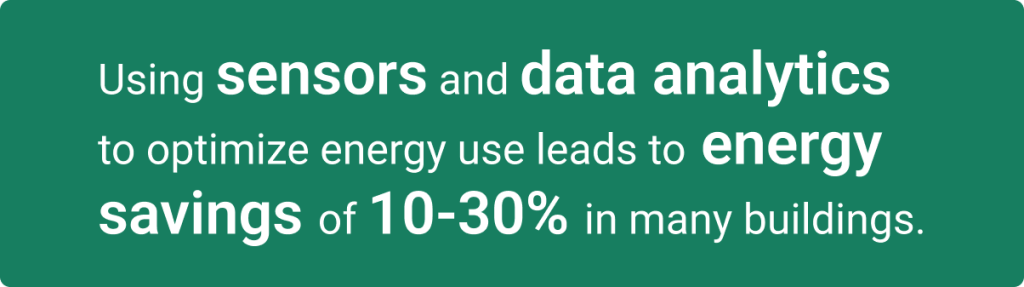
All this data helps organizations transition to proactive repairs.
Teams can use sensors to look at machines 24/7. This offers them up-to-date information on how points are working, and to allow them to prepare alerts when one factor appears incorrect.
Historic data will be worthwhile. It displays how machines acted sooner than earlier breakdowns, serving to foretell future very important gear factors.
Making Educated Maintenance Alternatives
Good data helps teams make increased repairs choices. They will type issues sooner than they break in its place of after, which cuts down on shock breakdowns and upfront costs.
Precise-time data lets teams act fast when needed.
If a machine begins showing up, they may restore it immediately, stopping small points from turning into big ones.
Info moreover helps teams plan increased. They will schedule fixes for after they’ll set off the least problem, retaining machines working further often.
7. Fostering a Custom of Regular Enchancment
Making a practice of enchancment encourages staff to hunt out new information.
This mindset helps repairs teams hold ahead of potential factors.
Employee development packages can embody:
- Mentorship options
- Cross-training in a number of repairs areas
- Attendance at enterprise conferences
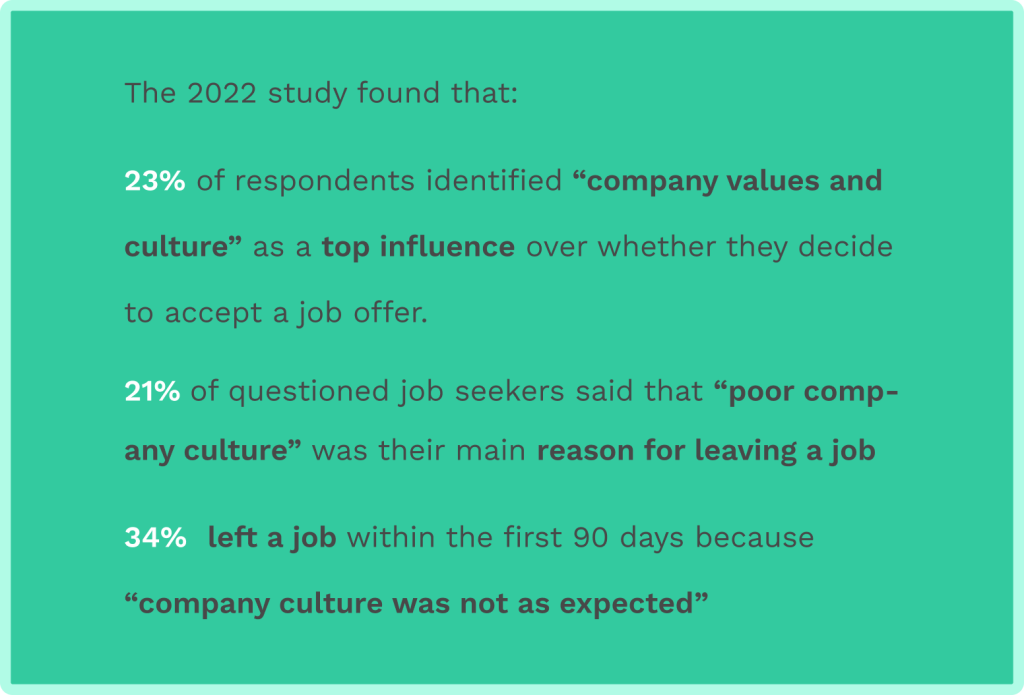
Recognizing and rewarding proactive habits reinforces its significance. This will likely comprise effectivity bonuses or growth options for employees who excel in preventive practices.
Encouraging idea-sharing amongst workforce members promotes innovation. Frequent conferences to debate enhancements can lead to further surroundings pleasant repairs processes.
Value-Revenue Analysis of Proactive vs. Reactive Maintenance
Proactive repairs practrices give consideration to stopping factors sooner than they occur.
This technique can cut back repairs costs by 25% as compared with reactive strategies.
Reactive repairs solely addresses points after gear fails. Whereas it may seem cheaper initially, it often ends in larger costs in the long run.
Proper right here’s a breakdown of key elements as a result of it pertains to reactive and proactive repairs:
Costs:
- Proactive: Elevated upfront funding in planning, teaching, and kit
- Reactive: Lower preliminary costs nonetheless larger emergency restore payments
Benefits:
- Proactive: Extended gear lifespan, lowered downtime, improved safety
- Reactive: No fast costs if no failures occur
Proactive repairs prevents sudden breakdowns, chopping downtime and emergency restore costs. This ends in long-term monetary financial savings and improved effectivity.
A price-benefit analysis must take note of every short-term and long-term impacts. Whereas proactive repairs may value further upfront, it often results in very important monetary financial savings over time.
Companies that change to proactive repairs often see a optimistic return on funding.
Diminished restore payments and elevated gear reliability offset the preliminary costs.
Prolonged-Time interval Have an effect on of Proactive Maintenance
A proactive repairs plan creates lasting benefits for organizations. It extends gear lifespans and reduces and boosts effectivity all through operations.
These impacts add up over time to produce very important price.
Enhancing Asset Life Cycle
Proactive repairs helps belongings final extra. Frequent checks and upkeep forestall small factors from turning into big points. This technique reduces placed on and tear on gear.
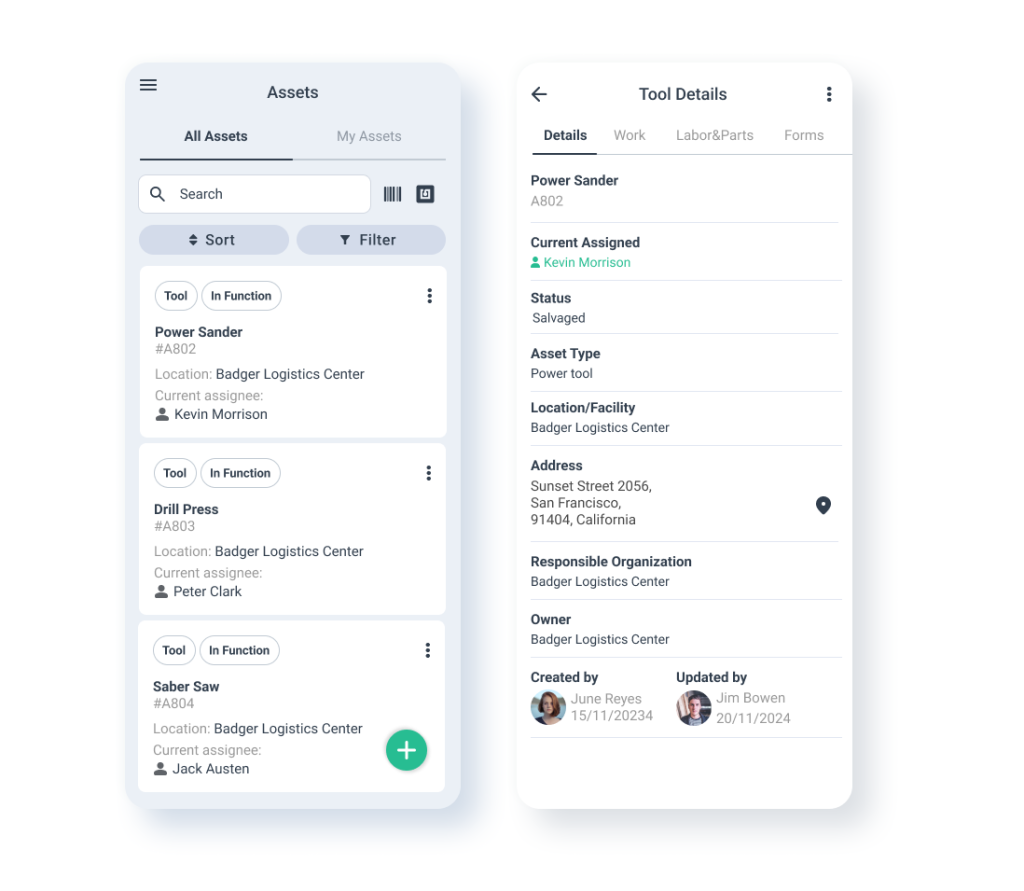
Improved gear reliability is a key outcomes of proactive repairs practices.
Appropriately maintained machines break down a lot much less often, which implies a lot much less downtime and fewer emergency repairs.
Proactive repairs can predict when replacements are needed. Organizations can plan and funds for model spanking new gear, avoiding sudden, dear purchases.
Over time, longer-lasting belongings get financial financial savings.
The need for frequent replacements decreases, and capital payments decrease as gear serves its goal for further years.
Enhancing Operational Effectivity
Proactive repairs focuses on how correctly a facility runs day-to-day. An environment friendly proactive repairs program creates a smoother workflow with fewer disruptions.
Deliberate repairs actions set off a lot much less interference than sudden breakdowns. Work may be scheduled all through off-peak hours, retaining operations working all through busy cases.
One different revenue is lowered repairs costs.
Catching factors early is often cheaper than fixing primary failures. It moreover makes use of fewer belongings and takes a lot much less time.
Effectivity constructive features lengthen previous repairs duties. Successfully-maintained gear works increased, which can improve manufacturing tempo and prime quality. As machines run at peak effectivity, vitality use may also go down.
Conclusion
Shifting to proactive repairs offers many benefits for corporations. It helps forestall breakdowns, cuts costs, and extends gear life.
Organizations can take various steps to make this transformation. Making a faithful repairs workforce and using data and know-how to establish factors early is important.
Teaching staff on new methods will be important. Getting buy-in from administration will assist drive the transition.
Proactive repairs has some challenges. It requires an upfront funding of time and belongings, nonetheless the long-term payoff is value it for a lot of corporations.
With the exact technique, corporations can cut back reactive work, improve routine inspections, and provides consideration to prevention. This ends in smoother operations and fewer downtime.
The switch to proactive repairs is a journey. It takes time and effort.
Nonetheless for lots of organizations, it’s a smart technique to boost effectivity and cut back costs.