Get a Free WorkTrek Demo
Let’s current you the way in which WorkTrek can help you optimize your maintenance operation.
Try for free of charge
In a super world, all maintenance might be deliberate, scheduled, and executed proactively to do away with instruments downtime and operational disruptions. On this remaining info, we’ll uncover the seven major lessons of reactive maintenance in-depth.
We would wish to dwell in a actuality the place every potential failure is predicted and prevented, every asset hums alongside at peak effectivity, and maintenance is a straightforward, orderly course of from start to finish.
Nonetheless, in comply with, the sudden tends to happen. Instruments can break down with out warning, even with basically probably the most sturdy predictive and preventive maintenance packages.
Parts placed on out, instruments breaks, accidents occur, and the surprising rears its head. When points go incorrect, reactive maintenance is how we reply and restore common operations.
Whereas proactive maintenance strategies are literally preferable for necessary property, reactive maintenance strategies will always be important for a balanced reliability and maintenance program.
The recent button is knowing the various types of reactive maintenance and understanding when and how one can deploy the becoming technique for max effectiveness.
On this whole info, we’ll uncover the eight major lessons of reactive maintenance in depth:
- Breakdown maintenance
- Corrective maintenance
- Emergency maintenance
- Deferred maintenance
- Run-to-failure maintenance
- Catastrophe maintenance
- Opportunistic reactive maintenance
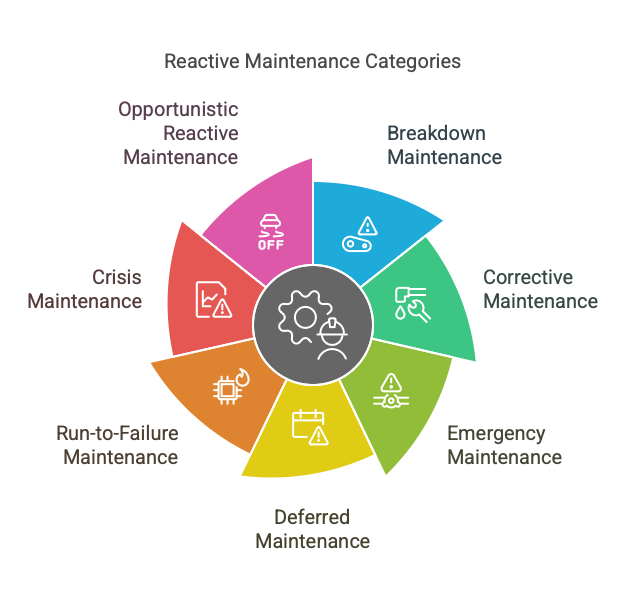
We’ll current a clear definition for each type, make clear the way in which it really works with real-world examples, deal with the benefits and downsides, and provide steering on when to make use of.
Let’s dive in, starting with basically probably the most basic form of reactive work: breakdown maintenance.
1. Breakdown Repairs
The first technique is Breakdown Repairs. Moreover often called run-to-failure maintenance, breakdown maintenance is actually probably the most straightforward form of reactive maintenance.
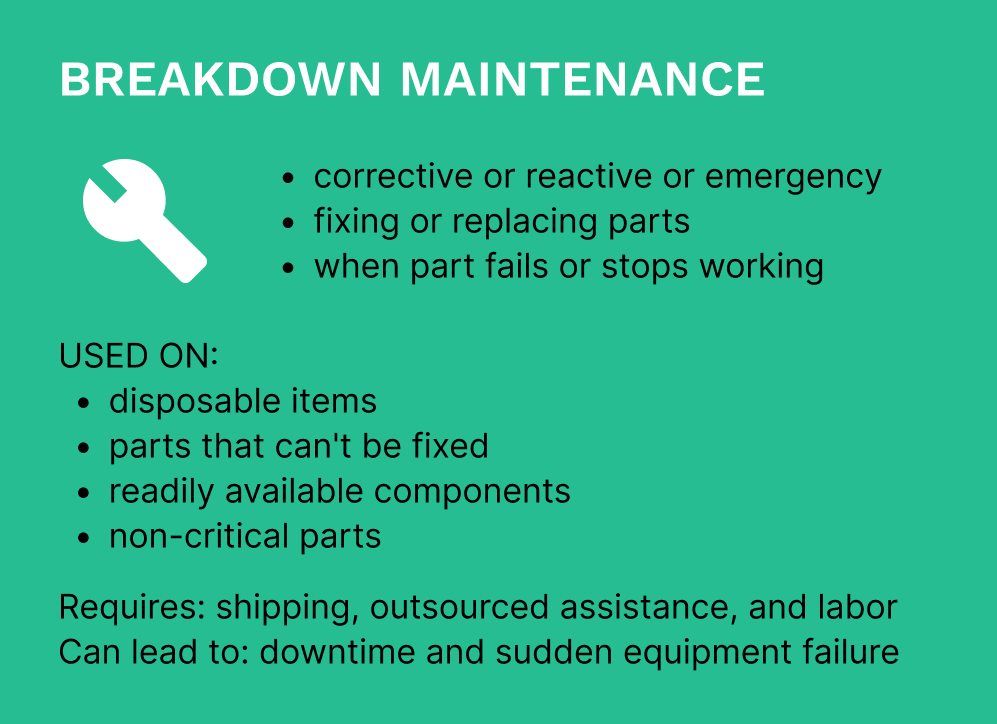
As a result of the title implies, it consists of deliberately letting instruments run until it completely breaks down after which repairing or altering it.
Whereas this reduces short-term restore costs, it might improve unpredictable instruments failures.
How does breakdown maintenance work?
With a breakdown maintenance technique, property are intentionally operated until they fail. No preventive or predictive actions are taken to maintain the instruments’s state of affairs.
Any corrective movement is lastly taken when the asset bodily breaks all the way in which all the way down to the aim that it might no longer function as meant.
This may sound like negligence or poor planning at first.
Nonetheless, in certain circumstances, breakdown maintenance is a deliberate, rational option to forego any preventive or predictive work on a low-criticality asset and run it to failure sooner than repairing or altering it.
When to make use of breakdown maintenance
Breakdown maintenance is often used for non-critical property the place a failure does not significantly impression operations, worker safety, product prime quality, or the ambiance.
It’s biggest fitted to instruments that meets a variety of of the subsequent requirements:
- Redundant property: When a variety of equal property exist, one can take over if one different fails.
- Replaceable property: Instruments that is quick, easy, and low-cost to modify upon failure.
- Low-cost property: When the restore or various costs are low as compared with the worth of preventive maintenance over time.
- Non-essential property: Failure does not halt manufacturing or impression safety or prime quality.
Some examples of relevant breakdown maintenance embrace basic lighting in a storage room, redundant pumps in a non-critical fluid swap system, or a single desktop laptop computer in an administrative office.
In each case, a failure, whereas inconvenient, does not interrupt core operations.
Backup selections may be discovered, and restore/various is straightforward.
Investing carefully in stopping these low-impact failures would in all probability not be effectively well worth the costs.
Advantages of breakdown maintenance
- Minimal planning and labor hours are required upfront
- No funding throughout the asset until failure occurs
- Makes monetary sense for low-priority, low-cost property
- Simple for the group to know and implement
Disadvantages of breakdown maintenance
- Elevated hazard of sudden, unplanned downtime
- Failures could also be catastrophic and costlier to restore
- Funds and helpful useful resource desires develop into unpredictable
- May end up in a shorter whole asset lifetime
- Potential safety, environmental, and prime quality risks
So, in summary, breakdown maintenance usually is a authentic and economical technique significantly conditions for non-critical property.
Nonetheless, relying solely on breakdown maintenance might be irresponsible and harmful for any asset important to manufacturing, safety, or the ambiance.
2. Corrective Repairs
The second reactive maintenance technique is corrective maintenance.
Corrective maintenance goes a step further than basic breakdown maintenance.
It moreover consists of repairing failed instruments nevertheless with the necessary additional targets of determining the muse causes of the failure and making corrective changes to working practices or instruments to forestall the problem from recurring.
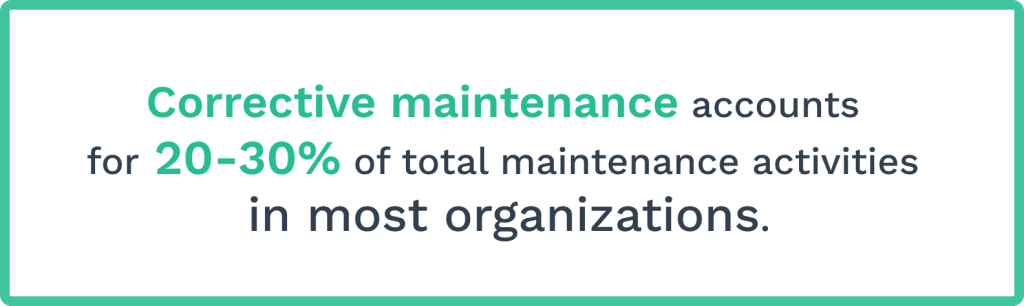
How does corrective maintenance work?
Corrective maintenance begins equally to breakdown maintenance—an asset is run until it fails, then repaired to working state of affairs.
Nonetheless, what models corrective maintenance apart is the additional cope with systematically determining why the failure occurred after which taking centered steps to forestall it from occurring as soon as extra.
After repairing the failed instruments, maintenance technicians will completely analyze the asset to find out all the components contributing to the breakdown.
They provide the impression of being previous the superficial indicators to uncover the muse set off – not merely the quick technical clarification for the failure nevertheless the underlying weaknesses in instruments, processes, or practices that allowed it to happen.
As an example, suppose a necessary pump failed because of the impeller expert excessive cavitation damage.
Examples of Corrective Repairs
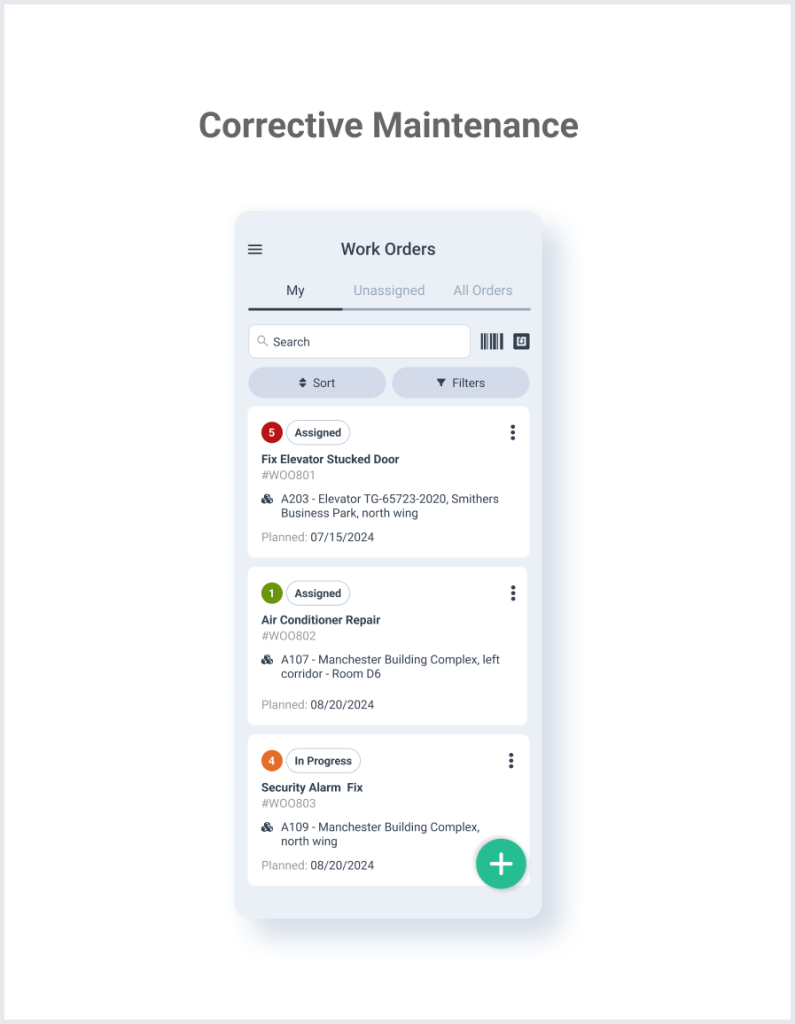
Whereas breakdown maintenance may restore or substitute the impeller itself, corrective maintenance digs deeper to hunt out out why the cavitation occurred throughout the first place:
- Have been the impeller or pump housing comprised of the wrong supplies?
- Was the pump being operated outside its designated flow into range?
- Have been there insufficient internet constructive suction head (NPSH) margins?
- Was the fluid contaminated with abrasive particulates?
- Have been there errors throughout the pump’s arrange or alignment?
By asking these sorts of probing questions and tracing the failure once more to its provide, maintenance personnel can then make corrective changes to forestall the cavitation from damaging the impeller as soon as extra, akin to:
- Upgrading the impeller supplies
- Adjusting the working flow into expenses
- Rising suction piping diameter to boost NPSH
- Placing in suction strainers to remove contaminants
- Realigning shafts and bettering arrange practices
This systematic problem-solving course of is the essence of corrective maintenance – not merely fixing failures nevertheless understanding and eliminating their causes to boost whole reliability and effectivity.
When to make use of Corrective Repairs
Corrective maintenance is appropriate when breakdowns have occurred, and in addition it’s worthwhile to cease them from reoccurring.
It’s significantly related for high-impact failures which have already occurred a variety of situations.
At a certain stage, repeatedly fixing the similar draw back again and again turns into costlier and disruptive than merely investing the time to investigate and resolve the underlying root causes fully.
The frequency and costs of breakdowns exceed the costs of corrective movement.
Corrective maintenance may also be useful when comparable failure patterns emerge in groups of equal or related property.
Suppose a complete fleet of autos is experiencing the similar persistent breakdowns. In that case, corrective maintenance can help decide design flaws, improper utilization practices, or maintenance shortcomings that could be addressed all through the whole fleet concurrently.
Advantages of corrective maintenance:
- Targets to cope with and do away with the muse causes of points, not merely indicators
- Reduces reactive maintenance desires and repeat failures over time
- Gives alternate options to enhance and optimize property
- Builds organizational information about failure modes and outcomes
- Extends asset lifespans and improves whole system reliability
Disadvantages of corrective maintenance:
- Requires additional time, skill, and belongings than basic breakdown repairs
- Relies upon upon educated technicians expert in root set off analysis
- May comprise in depth troubleshooting, analysis, and testing
- Sometimes necessitates short-term manufacturing disruptions to complete
- Might require shopping for spare elements and provides not saved available
Variations to Breakdown Repairs
Corrective maintenance is moderately extra full and improvement-focused than straightforward breakdown maintenance.
When executed efficiently, it might lead to necessary, systemic effectivity enhancements that cut back full maintenance costs and downtime over the long run.
Nonetheless, it does require an even bigger upfront funding and performance than merely fixing the quick points.
3. Emergency Repairs
The third and most urgent form of reactive maintenance is emergency maintenance.
As a result of the title suggests, it provides with basically probably the most pressing, necessary, and possibly dangerous failures that require quick movement.
How emergency maintenance works
Emergency maintenance is all about velocity. When a excessive failure occurs, the overriding priorities are to scale back damage, defend human safety, and restore common operations as shortly as attainable.
Repairs are made rapidly, usually even swiftly, to get the failed instruments up and working as soon as extra above all else.
Until the emergency is stabilized, additional full repairs and proper troubleshooting of the underlying causes are deferred.
The primary goal is on making use of quick fixes to stop the metaphorical bleeding and preserve points transferring throughout the transient time interval.
Examples of Emergency Repairs
As an example, take into consideration a water treatment plant experiencing a catastrophic failure of an enormous pump, with water flooding the pump room.
On this case, emergency maintenance would comprise shortly turning off the flow into, fixing the pump seals with short-term gaskets or coatings, and restarting the pump to keep up the water present flowing—even when the pump is due for scheduled preventive maintenance.
The chief concern is defending public effectively being by stopping water present interruption.
Solely after the quick hazard has handed would the maintenance group perform a full root set off analysis, substitute the short-term repairs with appropriate elements, and full all the deferred preventive maintenance work.
When to make use of emergency maintenance
Emergency maintenance must be reserved for lower than basically probably the most excessive, pressing failures that significantly threaten operations, worker or public safety, the ambiance, or compliance with authorized tips and guidelines.
Some real-world conditions the place emergency maintenance might be warranted embrace:
- A burst pipe flooding a necessary work area
- {{An electrical}} instruments fire in a chemical processing facility
- A severed underground power cable disrupts electrical power
- Failure of a single personalized asset that halts the whole manufacturing line
- A cracked storage tank leaking poisonous or explosive substances
Suppose breakdowns comprise imminent risks to employee safety, completely halt manufacturing, threaten to set off environmental contamination, or rapidly lead to in depth secondary property damage. In that case, emergency maintenance is the appropriate plan of motion.
It’s not for minor inconveniences nevertheless for genuinely extreme and urgent malfunctions.
Advantages of emergency maintenance
- Minimizes the impression and size of necessary asset failures
- Incorporates and controls the extreme penalties of failures
- Prioritizes velocity to protect agency output and reputation
- Useful for rapidly satisfying approved/regulatory requirements
- Prevents most important damage to indispensable property and infrastructure
Disadvantages of emergency maintenance
- Rushed repairs are generally short-term stopgap measures
- Repairs personnel would possibly take unsafe shortcuts beneath stress
- Typically, it costs additional as a consequence of additional time labor, expedited elements expenses, and plenty of others.
- Lack of appropriate planning will enhance the possibilities of errors and rework
- Causes unimaginable stress and stress on the maintenance group
- Can in all probability set off further damage if not executed fastidiously
Emergency maintenance is actually probably the most chaotic, demanding, and error-prone reactive maintenance work. The combo of intense time stress, extreme stakes, and restricted belongings make doing the job appropriately an unimaginable downside.
Nonetheless it is the solely risk in bona fide emergency conditions — it takes absolute priority over all completely different deliberate maintenance actions.
In spite of everything, the additional an organization can cease failures from escalating into full-blown emergencies, the upper.
4. Deferred Repairs
The fourth form of reactive maintenance is deferred maintenance.
Deferred maintenance postpones maintenance actions, usually as a consequence of restricted belongings or completely different priorities taking precedence.
How deferred maintenance works
With deferred maintenance, wished inspections or scheduled routines decide maintenance work, nevertheless the repairs are deliberately delayed reasonably than acted on immediately.
The maintenance duties get added to a backlog, so I am going to return to complete them later.
Let’s ponder an occasion state of affairs to make deferred maintenance additional concrete:
All through a routine maintenance inspection on an air compressor, technicians uncover that the consumption filter housing is cracked.
It doesn’t appear to impact effectivity adversely, however it need to be modified rapidly.
Nonetheless, the maintenance group is understaffed and lacks spare filter housing.
They resolve that the hazard of failure is low throughout the transient time interval and deliberate, deferring the filter housing restore until additional personnel could also be employed and the half procured. The filter housing various is added to the deferred maintenance backlog.
This occasion reveals how deferred maintenance permits organizations to consciously prioritize and schedule maintenance duties over an prolonged time horizon based mostly totally on hazard, belongings, and targets.
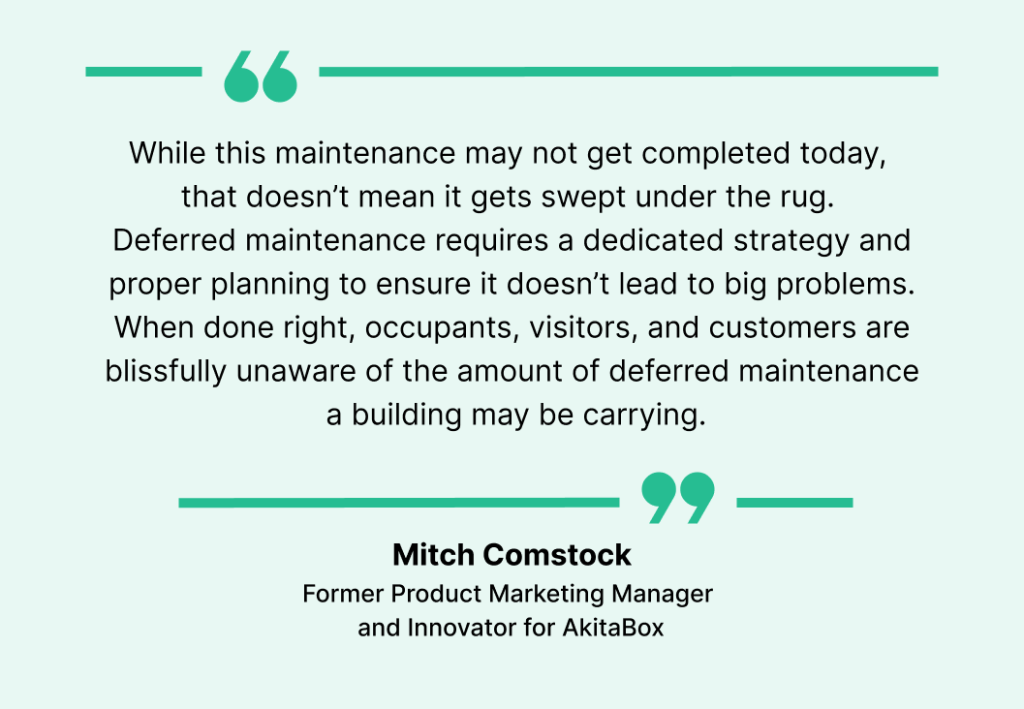
When to make use of deferred maintenance: Deferred maintenance is appropriate for lower-risk maintenance desires that don’t require quick consideration to forestall extreme penalties.
It’s generally used for:
- Lower-criticality property which have remaining useful life
- Repairs desires that are not safety-critical
- Repairs that could be safely postponed with low-risk
- Work that could be combined with future scheduled maintenance
- Duties the place labor, elements, or funds are briefly unavailable
Examples of deferred maintenance
- Touching up paint on the skin of a setting up
- Altering worn nevertheless nonetheless helpful flooring in an office lobby
- Upgrading getting older nevertheless not unsafe electrical wiring
The recent button is in truth and exactly assessing the risks of deferral. Just because instruments stays to be working doesn’t indicate pushing apart maintenance is wise.
Any deferral alternative should account for failure prospects, safety, and the implications of breakdown. Deferral is for lower-risk maintenance solely.
Advantages of deferred maintenance
- Greater makes use of restricted maintenance belongings and budgets
- Permits bundling of maintenance duties for effectivity
- Accommodates labor, supplies, and funding availabilities
- Permits maintenance planning on longer time scales
- Avoids over-maintaining property with an enormous remaining life
Disadvantages of deferred maintenance
- Will enhance the hazard of sudden failures and downtime
- Can enhance costs if small points set off greater damage
- Deferred duties usually develop into additional superior over time
- Creates a maintenance backlog that need to be managed
- May negatively impression asset effectivity and longevity
- Can create safety risks if deferrals shouldn’t managed appropriately
Lastly, the even handed use of deferred maintenance is about balancing costs, risks, and restricted maintenance capacities.
There’ll always be additional maintenance desires than time and belongings to cope with them. The recent button is prioritizing intelligently based mostly totally on criticality and managing the deferred backlog fastidiously so points don’t snowball uncontrolled.
Like the alternative reactive maintenance varieties, deferred maintenance is one different useful nevertheless restricted instrument that have to be utilized with skill, information, and discretion as half of an even bigger maintenance method.
5. Run-to-Failure Repairs
The fifth form of reactive maintenance is Run-to-failure maintenance.
The intentional maintenance method permits chosen instruments to operate until it breaks down completely with none preventive or predictive maintenance interventions.
No matter its title, run-to-failure is not a haphazard technique nevertheless a conscious option to forgo maintenance investments in an asset.
How run-to-failure maintenance works
In a run-to-failure technique, property are deliberately chosen to acquire no proactive maintenance all by means of their service life.
The group makes an educated alternative that it is additional economical to react to failures as they occur reasonably than spend cash on stopping or predicting failures for these specific property.
This doesn’t indicate that run-to-failure property are ignored or that failures are a shock. The necessary factor distinction is that run-to-failure is utilized selectively and intentionally to property that meet certain requirements.
The property get hold of shut monitoring and are allowed to run until clear indicators of impending failure are detected, at which stage they’re shut down and repaired or modified.
Enterprise Examples
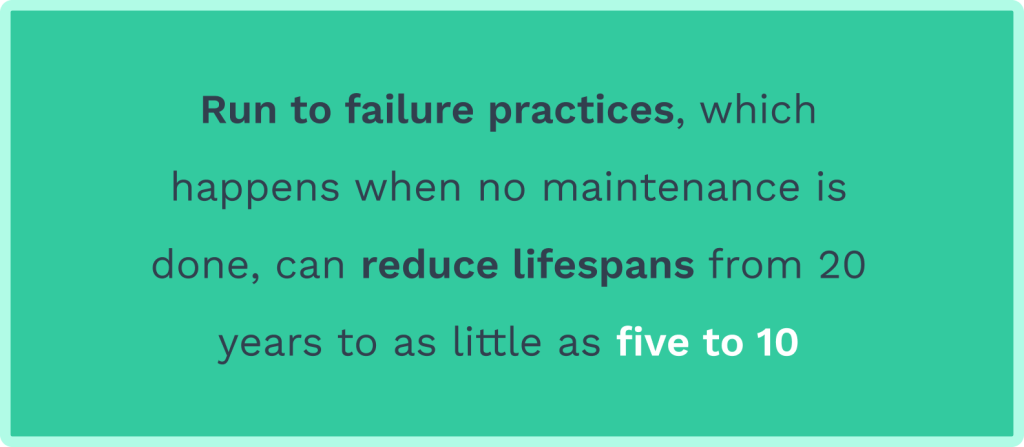
Take into consideration a producing facility with two equal air compressors supplying instrument air, each sized to meet full plant demand.
The plant managers do a financial analysis evaluating the costs to maintain the compressors proactively to the costs and risks associated to a run-to-failure technique.
They determined that since each compressor can cope with 100% of the load, an unplanned failure of 1 compressor will not impression manufacturing as long as the restore turnaround is relatively quick.
Based mostly totally on the compressors’ historically low failure expenses and acknowledged wear-out mechanisms, they decide {{that a}} run-to-failure method makes financial sense as compared with investing in preventive overhauls.
Don’t merely set it and overlook it.
Nonetheless, it’s important to note that this is not a “set it and overlook it” technique. The group nonetheless routinely screens the compressors’ effectivity, monitoring stress, temperature, vibration, and effectivity.
As rapidly as any of these parameters exceeds preset thresholds, indicating the tip of life is near, the plant will proactively take the unit offline for various sooner than catastrophic failure.
In summary, run-to-failure doesn’t indicate abandoning the property completely; in its place, it means consciously deciding on to forego maintenance until clear indicators of impending breakdown are seen by state of affairs monitoring.
The aim is to maximise the asset’s useful life whereas avoiding premature or pointless maintenance spending.
When to make use of run-to-failure maintenance
Run-to-failure is often reserved for terribly reliable, non-critical property which may be easy to modify or restore upon failure.
Some key requirements for potential run-to-failure candidates embrace:
- Instruments has prolonged mean-time-between-failures (MTBF) intervals
- Failure modes are well-understood and relatively predictable
- Redundant fashions may be discovered to carry the load all through repairs
- Spares could also be obtained shortly and inexpensively upon failure
- Belongings could also be modified additional economically than repaired
- Instruments has a random failure pattern not impacted by getting older
- Failures do not pose any safety, environmental or prime quality risks
Some widespread examples of property which may be commonly managed with a run-to-failure technique:
- Lightbulbs or small electrical motors for non-critical instruments
- Laptop peripherals like keyboards, mice, and audio system
- HVAC fashions for employee break rooms or administrative areas
- Redundant pumps or followers in utility packages with further functionality
- Automotive tires which may be modified upon reaching tread placed on limits
Advantages of run-to-failure maintenance:
- Can significantly cut back maintenance costs for high-reliability property
- Eliminates hazard of toddler mortality from pointless PM actions
- Permits property to be used for his or her full-service life sooner than various
- Simple to know and doesn’t require detailed planning or scheduling
- Works successfully for property with random failure patterns if spares may be discovered
Disadvantages of run-to-failure maintenance:
- Not acceptable for necessary property the place failure might be very costly or unsafe
- Requires retaining ample spare elements and various property in inventory
- Could possibly be powerful to deal with if too many property are put into run-to-failure mode
- Relies upon carefully on state of affairs monitoring to detect impending failures in time
- Might lead to a whole lot of outdated or unrepairable property piling up
When appropriately utilized to the becoming types of property, run-to-failure maintenance usually is an economical method for managing reliability whereas avoiding over-maintenance.
The way in which to Apply Run-To-Failure Repairs?
Nonetheless, it need to be utilized selectively based mostly totally on a radical analysis of failure modes, outcomes, and asset criticality.
For a lot of plant property, some combination of preventive and predictive maintenance will usually be additional relevant than a pure run-to-failure technique.
Nonetheless run-to-failure usually is a worthwhile part of an whole maintenance program for that subset of property the place the cost-risk-benefit calculation is wise.
6. Catastrophe Repairs
The sixth form of reactive maintenance is catastrophe maintenance.
Catastrophe maintenance is actually probably the most urgent and extreme form of reactive maintenance.
It occurs when an sudden, excessive, and time-critical failure causes or threatens to set off most important operational, safety, environmental, or financial impacts.
In a catastrophe maintenance state of affairs, the singular prime priority is to revive the failed asset to the minimal required efficiency as shortly as attainable to avert catastrophe.
How catastrophe maintenance works
Catastrophe maintenance is a rapid-response, all-hands-on-deck emergency. When a catastrophe failure occurs, all of the issues else takes a backseat to the overriding targets of:
- Defending human effectively being and safety
- Stopping or containing environmental damage
- Minimizing operational downtime and disruption
- Avoiding regulatory non-compliance and approved obligation
Repairs teams abandoned all completely different deliberate work and rushed to implement short-term repairs and workarounds to stabilize the state of affairs.
They cope with doing the minimal important to get the asset once more up and working shortly.
Examples of Catastrophe Repairs
As an example, take into consideration a ruptured high-pressure gas pipeline at a petroleum refinery. A catastrophe maintenance response would comprise:
- Immediately shutting off the flow into and isolating the ruptured half
- Containing and cleaning up any spills or releases
- Welding a short patch over the rupture
- Re-routing flow into to bypass the damaged half if attainable
- Conducting a safety analysis and restarting the pipeline at lowered functionality
On this case, the patch job might be going not a eternal restore, however it permits operations to resume in a managed methodology until a full restore could also be completed. The recent button is velocity over perfection – doing what it takes to handle the quick catastrophe.
Forensic analysis determines the muse causes of failure, and durable eternal repairs are deferred until after the catastrophe has subsided. Stopping catastrophic impacts is the one concern throughout the heat of the second.
When to impress catastrophe maintenance
Catastrophe maintenance is triggered solely by excessive failures that threaten people, the ambiance, or enterprise viability and requires quick intervention. Eventualities that warrant a catastrophe response embrace:
- Fires, explosions, or toxic releases from course of instruments
- Structural collapses of buildings, tanks, or necessary infrastructure
- Most important spills of hazardous chemical substances or petroleum merchandise
- Ruptures of high-pressure vessels, piping, or storage tanks
- Full power outages or electrical system failures
The widespread thread is that these failures lengthen previous the asset itself and threaten to rapidly spiral into quite a bit larger human, environmental, or operational catastrophes if not managed shortly. They usually comprise potential off-site impacts and regulatory or approved penalties.
Advantages of catastrophe maintenance:
- Shortly accommodates and controls impacts of utmost asset failures
- Prioritizes velocity to cut back operational disruption and financial losses
- Protects human effectively being, safety and the ambiance from harm
- Minimizes bodily damage to plant property and infrastructure
- Ensures compliance with approved requirements and avoids penalties
Disadvantages of catastrophe maintenance:
- Reactive repairs are rushed and sometimes short-term “band-aid” choices
- Deferred root set off analysis permits underlying points to persist
- The maintenance group faces intense time stress and psychological stress
- Costs are extreme as a consequence of unplanned downtime, additional time, and emergency expenses
- Hasty work won’t alter to procedures and introduce errors and rework
- Belongings may be additional weak to recurring failures or a shorter lifespan afterward
Catastrophe maintenance, by definition, is an all-out, no-holds-barred firefighting response to an extreme event.
There’s no time for cautious planning, preparation, and procedure-following for normal maintenance. Expediency and triage are the driving components.
So, whereas a catastrophe maintenance response is necessary when true emergencies occur, it’s not an enchanting mode of operation.
It might be very demanding and cost-intensive, and it might moreover damage asset effectively being. The ultimate phrase function of a robust, proactive maintenance program is to forestall crises.
7. Opportunistic Reactive Repairs
The seventh form of reactive maintenance is opportunistic reactive maintenance.
Opportunistic reactive maintenance is a clever method that takes good thing about unplanned downtime or maintenance on one asset to proactively perform maintenance on completely different property which may be moreover down or accessible.
It’s a technique to benefit from an sudden various to complete completely different wished maintenance work with minimal additional disruption.
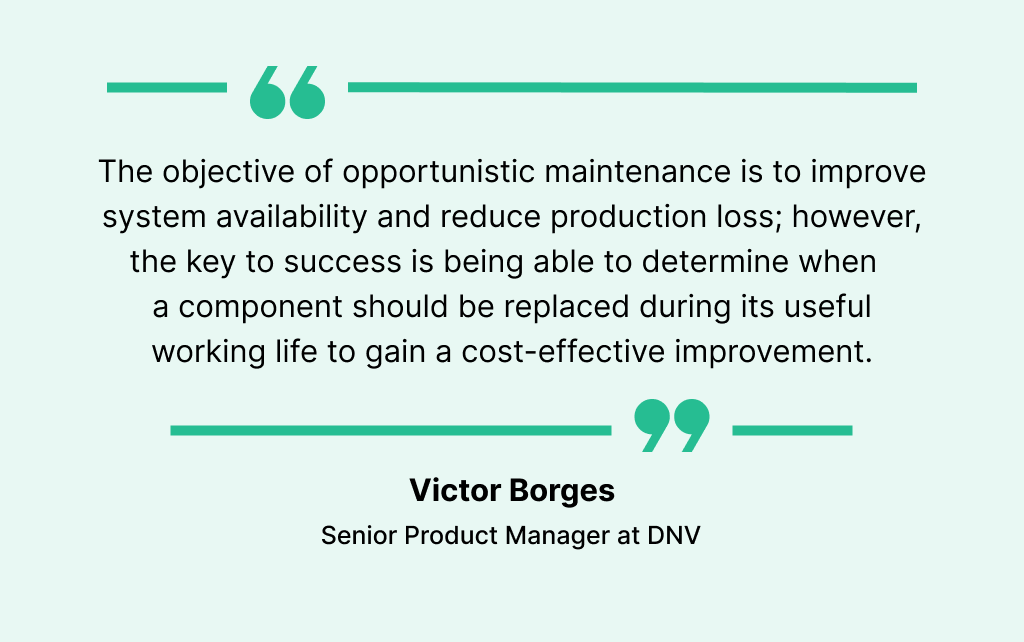
How opportunistic reactive maintenance works: The necessary factor idea behind opportunistic maintenance is that when a piece of equipment unexpectedly fails or is down for repairs, there could also be usually a ripple affect on completely different related or shut by instruments.
This unplanned downtime can present a golden various to hold out proactive maintenance on these completely different property with out further affecting manufacturing.
The way in which to use opportunistic reactive maintenance
Let’s stroll by an occasion for instance how opportunistic reactive maintenance is utilized:
Take into consideration a necessary conveyor belt in a producing plant unexpectedly breaking down, forcing the whole manufacturing line to be halted for repairs. The maintenance group ought to reactively substitute the damaged belt and rollers, which might take an estimated 12 hours.
The maintenance planner acknowledges an opportunity all through this 12-hour window whereas manufacturing stops.
The conveyor’s failure has made a variety of upstream and downstream property which may be usually powerful to entry whereas working (identical to the pallet wrappers, case erectors, and labelers) moderately extra obtainable.
The planner shortly generates a listing of all the PM duties and repairs due on these adjoining property all through the following month, akin to altering worn elements, calibrating sensors, and deep cleaning.
A crew is promptly assigned to complete all that soon-coming maintenance whereas the conveyor is being mounted.
Consequently, the plant can full a substantial amount of additional proactive maintenance all through unplanned downtime together with the reactive conveyor repairs.
Positive, the conveyor breakdown nonetheless disrupted manufacturing, nevertheless on the very least the plant could take full good thing about the downtime and “make lemonade out of lemons.”
That’s the essence of opportunistic maintenance—having the ability to mobilize and capitalize on sudden maintenance alternate options to get ahead of the PM curve. It requires a maintenance group to be agile, well-planned, and always trying to find alternate options to piggyback proactive work onto reactive repairs.
One other prime alternate options for opportunistic maintenance embrace:
- When a machine is down for scheduled PMs or upgrades, perform the similar work on equal stand-by machines whereas idle.
- If a roof is already being repaired, use the scaffolding and crew to look at and proactively restore adjoining roof areas, drains, and gutters.
- Conduct thorough cleaning, modifications, and inspections on hard-to-access packages and components all through a deliberate plant shutdown.
When executed appropriately, opportunistic maintenance helps organizations perform additional proactive work with a lot much less whole impression on manufacturing schedules.
It’s a technique to flip unavoidable reactive downtime into productive, value-adding maintenance time.
When to make use of Opportunistic Repairs?
Opportunistic maintenance could also be utilized each time an asset is unexpectedly down for reactive repairs or when deliberate downtime on an asset moreover makes completely different related property obtainable for work. Ideally suited requirements for opportunistic maintenance embrace:
- A key asset failure causes completely different instruments to be idled
- The failure makes hard-to-access areas or components reachable
- Repairs are anticipated to take prolonged ample to get completely different work executed
- Licensed personnel may be discovered to hold out the extra work
- Spare elements and devices for the alternative work are available and ready
- Options align with high-priority PMs or repairs on necessary property
- The additional work scope gained’t negatively impression manufacturing
One other components that help organizations benefit from opportunistic maintenance:
- Having a proactive mindset and always trying to find hidden alternate options
- Sustaining detailed instruments histories and failure info for reference
- Conserving PM exercise lists and spare half requirements up to date and obtainable
- Using a grasp maintenance schedule to prioritize and coordinate all work
- Empowering maintenance crews to behave on alternate options whereas following standardized alternative requirements flexibly
- Monitoring opportunistic maintenance monetary financial savings and benefits to strengthen the comply with
Advantages of opportunistic maintenance:
- Reduces whole deliberate downtime by piggybacking PMs into unplanned repairs
- Gives entry to instruments that is usually powerful, dangerous or disruptive to maintain whereas working
- Permits additional of the “little points” to get executed that often get deferred
- Boosts proactive maintenance completion expenses and schedule compliance
- Will enhance productiveness of maintenance crews by reducing journey and setup time
- Promotes a additional versatile and opportunity-driven maintenance custom
Disadvantages of opportunistic maintenance:
- Requires cautious coordination to steer clear of conflicts between reactive and proactive work
- May lengthen the size of unplanned outages if not managed appropriately
- May trigger labor and spare elements shortages if alternate options shouldn’t well-forecasted
- Will enhance hazard of errors if appropriate procedures shouldn’t adopted throughout the rush to get further work executed
- May incentivize deferring proactive maintenance in hopes of “catching it” later opportunistically
The Upside of Emergency Repairs
Lastly, opportunistic maintenance is a technique to help organizations make the proper of a foul state of affairs when unplanned downtime occurs.
By being able to benefit from sudden alternate options to complete completely different wished maintenance, companies can improve their proactive maintenance effectivity with out together with to their schedule or funds.
Nonetheless, opportunistic maintenance need to be utilized thoughtfully and systematically to steer clear of inflicting additional points than it solves. It requires a extreme diploma of planning, communication, and coordination to guarantee that the additional work is definitely opportunistic and by no means disruptive.
It’s moreover important that opportunistic maintenance does not develop into an excuse for deferring necessary PMs or planning work.
Scheduled maintenance stays to be one of the best whole method—opportunistic maintenance must be the exception, supplementing, not altering, a robust PM program.
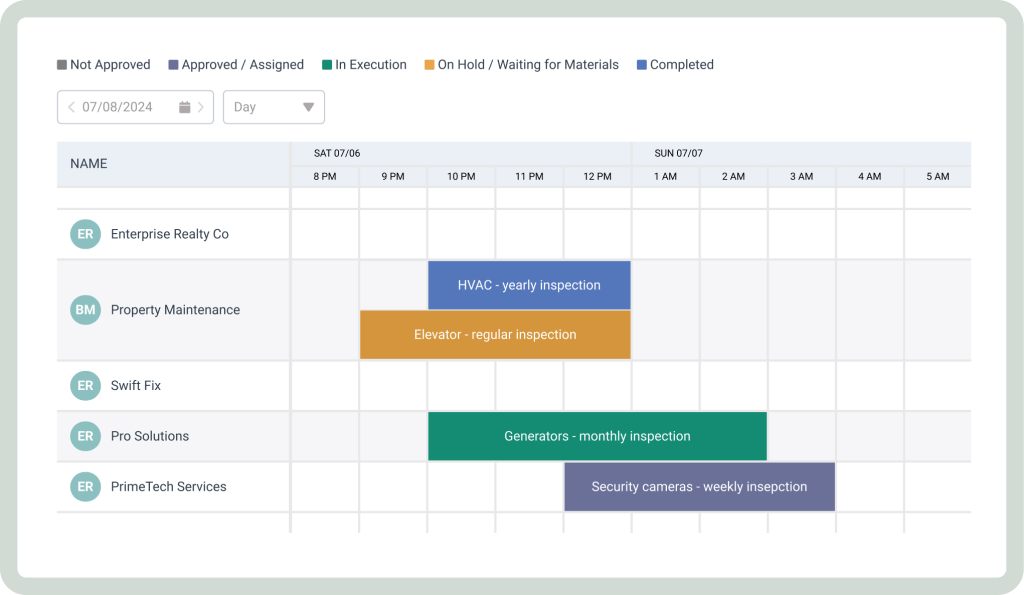
When utilized appropriately within the becoming circumstances, opportunistic maintenance is a worthwhile addition to the maintenance mix that will help counteract the unfavourable impacts of reactive repairs.
Making the most of every minute of downtime permits organizations to cut back their proactive maintenance backlogs and drive their property to ever-higher reliability ranges.
Closing Concepts
To summarize, a whole maintenance method can’t embody solely deliberate and scheduled maintenance.
Reactive maintenance will always play an enormous place in reliability and asset administration. Whereas it shouldn’t be the default technique, understanding and preparing for varied reactive maintenance circumstances is a core competency.
With a whole maintenance program encompassing proactive and reactive biggest practices, you’ll be successfully in your technique to optimizing your bodily property’ effectivity, reliability, and longevity all by means of their lifecycle.
The need for unplanned reactive work will not ever be eradicated. Nonetheless, you probably can take these unavoidable failures and breakdowns in stride and use them as alternate options to strengthen your asset administration program.