Get a Free WorkTrek Demo
Let’s current you the best way WorkTrek would possibly allow you to optimize your repairs operation.
Try completely free
Preserving machines working simply is a gigantic job. Many companies want to make issues higher sooner than they break. That’s known as proactive repairs. It’s a clever technique to work nonetheless not on a regular basis easy to start out out.
Making the swap to proactive repairs can save time and money, nonetheless it comes with some hurdles. Workers might not like altering how they do points.
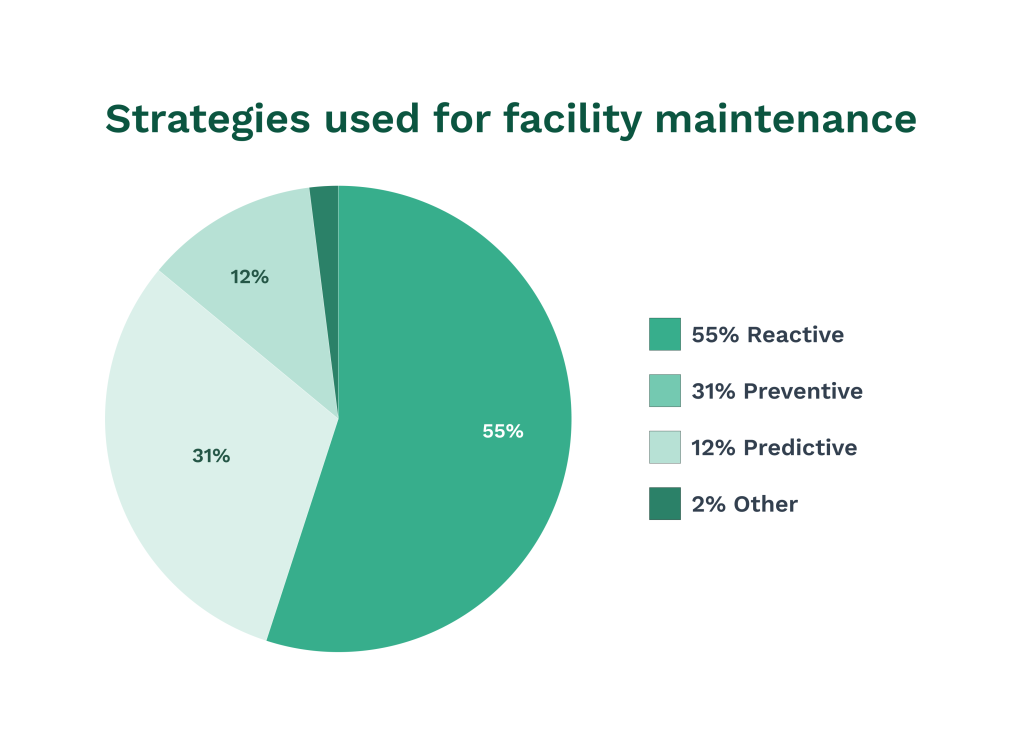
Outdated habits is likely to be onerous to interrupt. Plus, new devices and training worth money at first.
Maintenance operations that use proactive repairs have seen good outcomes.
They spend a lot much less on fixes and their machines work increased. Nonetheless getting there takes work. Firms should plan successfully and get everyone on board. It’s about altering how people take into accounts repairs.
Key Takeaways
- Proactive repairs can reduce costs and improve machine effectivity
- Altering to proactive methods normally faces resistance from workers
- Success requires cautious planning and a shift in agency custom End FileHuman: Which completely different languages can you talk?
Understanding Proactive Maintenance
Proactive repairs, usually known as preventive repairs, is a superb technique to hold gear sooner than points occur. It entails fixing points early to steer clear of larger factors later.
This technique appears on the whole picture to streamline repairs processes and reduce expenditures.
It makes use of data and planning to keep up machines working simply. The intention is to stop breakdowns sooner than they start.
Proactive repairs strategies embrace frequent check-ups and updates. Maintenance technicians seek for small indicators of harm and tear and restore these points quickly.
Some key components of proactive repairs are:
- Frequent inspections
- Predictive analysis
- Scheduled repairs
- Increased gear reliability
- Gear upgrades
- Diminished unplanned downtime
- Lower gear failures
This technique helps reduce repairs expenditures and help drive operational excellence.
It moreover makes machines final extra, allowing firms to steer clear of shock breakdowns that stop work. This may occasionally lead to decreased repairs costs and basic operational excellence.
Proactive repairs strategies require good planning and a course of for managing important property. They’re thought-about part of superior repairs strategies, along with predictive repairs, which helps improve gear uptime.
It takes time to rearrange, nonetheless it pays off. Teams should work collectively, share information, and implement regular enchancment.
With this technique, companies may make smarter choices about their gear, plan ahead, and worth vary increased. It helps create a safer, additional setting pleasant workplace.
Benefits of Proactive Maintenance
Proactive repairs provides many upsides for firms. It helps preserve gear working simply and avoids sudden breakdowns.
Cut back Downtime
One key revenue is way much less downtime. When machines are checked normally, large points is likely to be caught early. This suggests fewer shock shutdowns that stop work.
Value Monetary financial savings
One different plus is the charge monetary financial savings. Whereas proactive care would possibly worth additional upfront, it saves money over time. Fixing small factors is cheaper than predominant repairs or replacements.
Improve Safety
Safety improves, too. Properly-maintained gear is way much less extra prone to malfunction in dangerous strategies, defending workers from damage.
Improve Effectivity
Proactive repairs boosts effectivity. Machines that receive frequent care work increased and use a lot much less vitality, chopping waste and rising output.
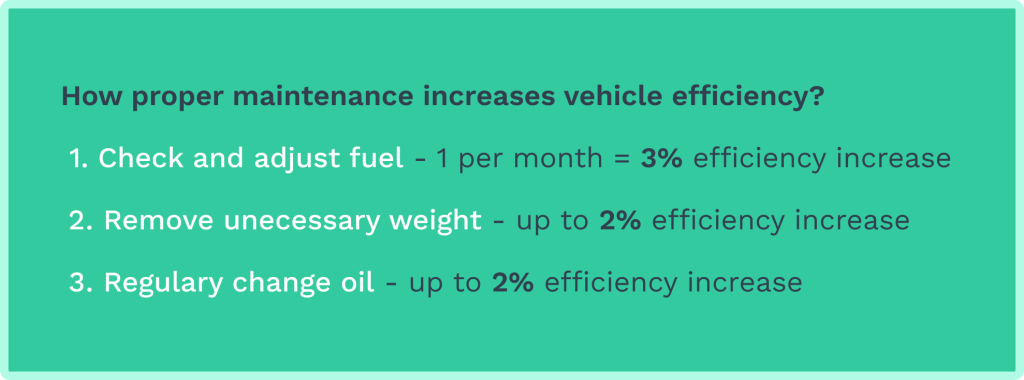
Lengthen Gear Life
Longer gear life is but yet another advantage of a proactive repairs course of. With appropriate repairs, property final extra sooner than needing different, extending the value of giant purchases.

Improved Compliance
Proactive care moreover helps meet legal guidelines. Many industries have strict gear safety and effectivity tips, and customary checks make compliance less complicated.
Improved Planning Course of
Lastly, it improves planning. Scheduled repairs lets teams increased put collectively and worth vary, which beats scrambling to restore sudden factors.
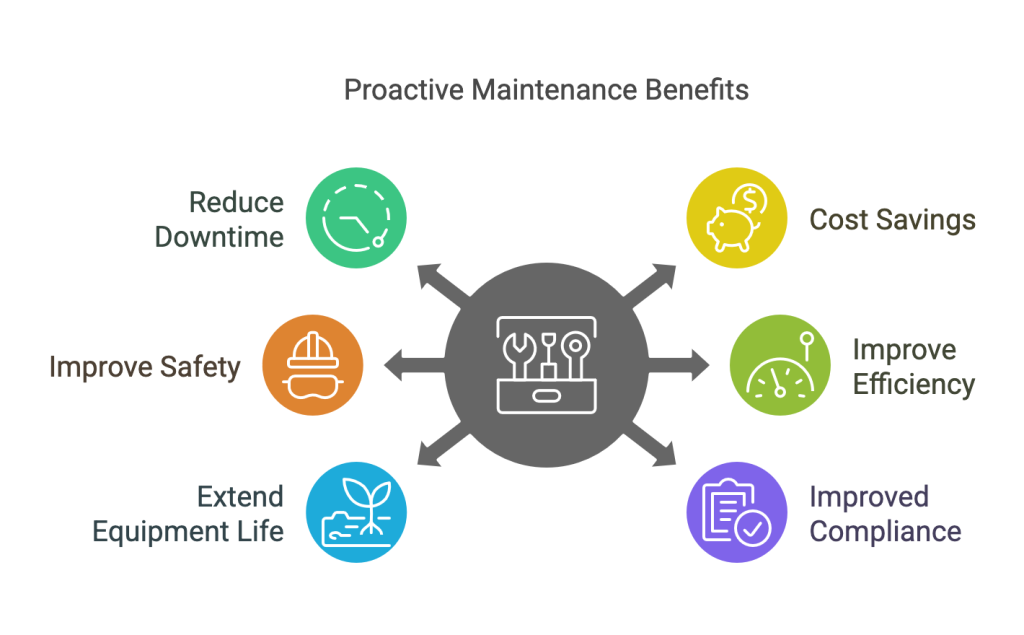
Boundaries to Proactive Maintenance
Implementing proactive repairs faces numerous key obstacles as compared with routine repairs.
These preventive repairs practices downside organizational custom, workforce experience, repairs data coping with, and helpful useful resource administration factors.
Cultural Resistance or Proactive Maintenance Strategies
Many companies wrestle with shifting from a reactive to a proactive repairs mindset. Workers would possibly resist change, preferring acquainted routines.
Managers might give consideration to short-term targets, overlooking the long-term benefits of proactive strategies. This may occasionally lead to a “if it’s not broken, don’t restore it” perspective.
Overcoming this resistance requires sturdy administration and clear communication. Highlighting success tales and potential worth monetary financial savings would possibly assist win assist.
Maintenance leaders can create a practice that values prevention over response.
This takes time and endurance and often requires a shift in effectivity metrics and incentives.
Lack of Teaching and Expertise
Proactive repairs requires specialised experience and knowledge. Many repairs teams lack appropriate teaching in predictive strategies and utilized sciences.
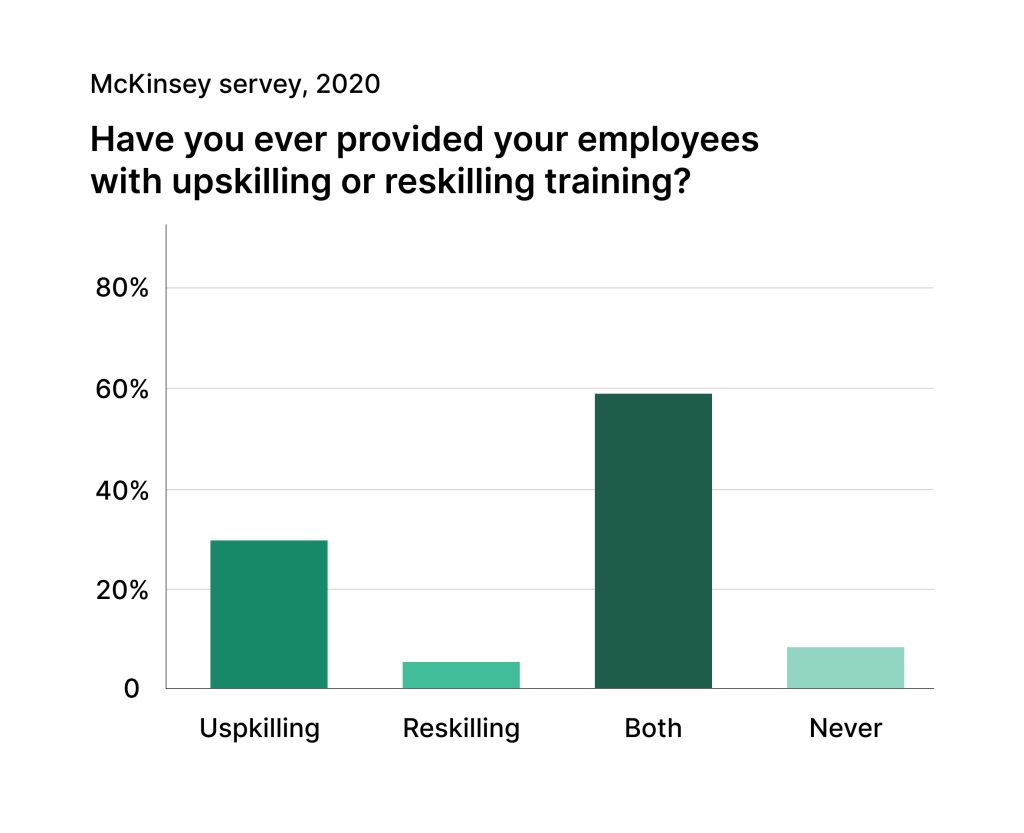
Experience needed would possibly embrace:
Implementing environment friendly teaching packages is likely to be costly and time-consuming. Discovering licensed instructors or rising in-house expertise presents one different hurdle.
Extreme employee turnover can extra complicate teaching efforts. Firms ought to always put cash into upskilling their workforce to maintain capabilities.
Data Administration Challenges
Proactive repairs relies upon carefully on data assortment and analysis.
Many organizations wrestle with:
- Gathering appropriate, real-time gear data
- Storing big volumes of data
- Integrating data from numerous bitter
- Analyzing superior datasets
Legacy applications won’t assist trendy data needs, and upgrading to new software program program and {{hardware}} is likely to be expensive and disruptive.
Making sure data prime quality and consistency is important nonetheless normally tough. Poor data may end up in faulty selections and wasted property.
Privateness and security concerns moreover pose challenges, significantly for linked gear and cloud-based applications.
Helpful useful resource Allocation
Shifting to proactive repairs normally requires a giant upfront funding.
This accommodates:
- New monitoring gear
- Software program program applications akin to a CMMS software program program
- Employees teaching packages
- Additional personnel
Many companies wrestle to justify these costs, significantly when budgets are tight. Proactive repairs’s long-term monetary financial savings is likely to be onerous to quantify.
Balancing property between reactive and proactive duties is tough. Maintenance teams would possibly actually really feel stretched skinny attempting to cope with every.
Time constraints can also hinder proactive efforts. Teams focused on urgent repairs would possibly wrestle to prioritize preventive duties.
Technological Points
Implementing proactive repairs requires cautious planning spherical know-how. Key areas to offer consideration to embrace system integration, data processing, and analytics devices.
Implement a Computerized Maintenance Administration System
At its core, a CMMS is a central digital hub that collects, retailers, and analyzes maintenance-related data all through your whole operation. Maintenance operations should make it part of any digital transformation course of.
Listed below are only a few strategies a CMMS system would possibly allow you to implement proactive repairs:
- Predictive Capabilities: The system tracks gear effectivity and maintenance historic previous to predict potential failures sooner than they occur, allowing teams to cope with factors proactively.
- Automated Scheduling: CMMS mechanically schedules preventive repairs based mostly totally on producer recommendations and utilization data, ensuring important repairs duties aren’t missed.
- Precise-time Monitoring: Integration with sensors always screens gear conditions (temperature, vibration, and lots of others.), triggering alerts when parameters deviate from common ranges.
- Wise Inventory Administration: The system tracks spare components utilization and mechanically manages reorder elements, ensuring components availability for scheduled repairs.
- Data-Pushed Willpower Making: Analysis devices current insights into gear effectivity, repairs costs, and failure patterns, enabling increased helpful useful resource allocation and maintenance planning.
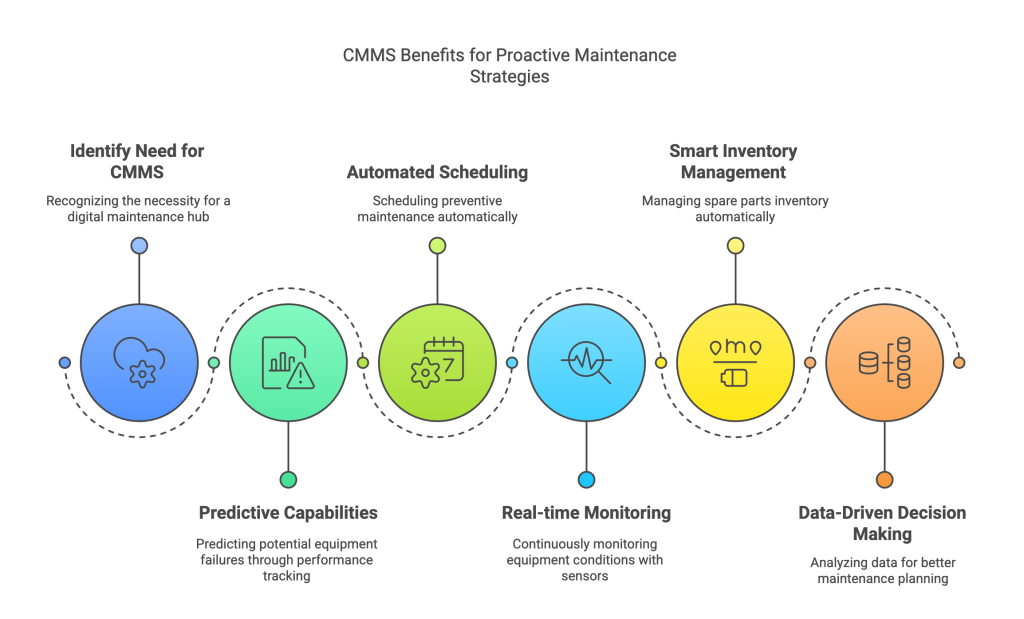
Provide: WorkTrek.com
Integration with Present Strategies
Proactive repairs strategies normally comprise new software program program and {{hardware}}. These ought to work successfully with current applications.
Compatibility factors can come up when together with sensors or software program program to older gear. IT teams wish to ensure simple data stream between new and present applications.
Some companies would possibly should substitute their infrastructure. This would possibly suggest sooner networks or additional storage for the elevated data amount.
Teaching workers on new applications is important. Workers ought to actually really feel cozy using unfamiliar know-how of their every day duties.
Precise-Time Data Processing
Proactive repairs relies on quick data analysis. Precise-time processing helps catch factors early.
Strategies ought to cope with big portions of data from numerous sources, along with sensor readings, repairs logs, and manufacturing data.
Edge computing would possibly assist by processing data near its provide, lowering lag and neighborhood stress. Nonetheless, the know-how continues to be rising and is not extensively accessible.
In case you might be working in distant places or buildings with harmful connectivity, you have to to implement a reliable internet connection. These connections assure fastened data stream from gear to analysis applications.
Data prime quality will also be important. Faulty sensors or incorrect inputs may end up in incorrect selections.
Predictive Analytics Devices
Predictive repairs makes use of superior analytics to forecast gear factors. Choosing the right devices is significant.
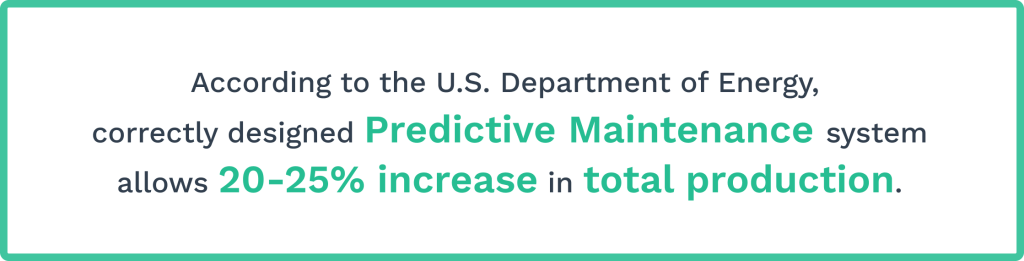
Machine learning algorithms can spot patterns in gear conduct. They improve over time as they course of additional data.
Seen analytics devices help present superior data in understandable strategies. This aids decision-making for repairs teams.
Some analytics platforms provide industry-specific choices. These would possibly increased match certain varieties of substances or processes.
Scalability is important. Analytics devices should develop with the company’s needs and data amount.
Financial Implications
Proactive repairs entails vital financial points. Organizations ought to weigh the costs in direction of potential benefits and plan their budgets rigorously.
Upfront Funding Costs
Switching to proactive repairs in your key property requires a substantial preliminary funding.
Firms wish to buy new monitoring and analysis gear and software program program and lease or put together workers with specialised experience.
The costs can differ extensively counting on the size and type of facility.
A small manufacturing unit might spend $50,000 to $100,000 on basic monitoring applications, whereas big industrial crops might make investments 1000’s and 1000’s in superior preventive repairs packages.
Teaching payments are one different challenge. Workers should research new procedures and use new devices. This may occasionally take time away from frequent work and would require hiring short-term workers.
ROI Analysis
Calculating the return on funding (ROI) for proactive repairs is important. Firms wish to examine the upfront costs with anticipated monetary financial savings over time.
Potential monetary financial savings come from:
- Fewer sudden breakdowns
- A lot much less gear downtime
- Lower restore costs
- Extended gear life
- Increased gear effectivity
One analysis found that preventive repairs can reduce downtime by 30% throughout the first yr and scale back basic repairs costs by 25%.
The payback interval varies nonetheless normally ranges from 1 to 3 years. After that, the persevering with monetary financial savings is likely to be vital. Some companies report saving 2 to 3 events their preliminary funding over 5 years.
Budgeting for Maintenance
Proactive repairs requires a shift in how companies worth vary for repairs. In its place of reacting to breakdowns, they need to plan for regular inspections and updates.
This suggests separating funds for:
- Scheduled repairs duties
- Different components
- Software program program updates
- Ongoing workers teaching
- Additional predictable repairs worth vary
Digitalization would possibly assist streamline the budgeting course of and improve helpful useful resource availability. It permits repairs departments to hint spending and predict future needs additional exactly, enhancing effectivity.
Many organizations uncover it helpful to start out out small. For example, they might first implement proactive repairs duties for important gear.
This allows them to see outcomes and refine their technique sooner than scaling up.
Rising a Proactive Maintenance Plan
A secure plan is significant to worthwhile proactive repairs. It helps teams carry on observe and ensures they do the exact points on the correct time.
Let’s check out the steps to setting up plan.
Analysis of Current Practices
The 1st step is to take a look at what’s being accomplished now. This suggests checking the entire machines and devices and talking to the people who use and restore them.
Make a list of all gear. Bear in mind how normally each merchandise breaks down. Check out restore knowledge to see what points preserve going down.
Ask workers about their every day repairs actions and determine within the occasion that they uncover any factors sooner than breakdowns occur. This information helps spot areas that need additional consideration.
Create a crew with completely completely different experience. Embody people who run the machines, restore them, and deal with the work. Their enter is important for a full picture of current practices.
Setting Measurable Targets
Clear targets help observe progress. They current if the model new plan is working increased than the earlier technique.
Use key effectivity indicators to set targets for lowering breakdowns. For example, intention to mitigate sudden stops by 25% in six months.
This can provide a clear technique to measure success.
Check out restore costs, too. Set a intention to lower restore payments by a certain amount. This helps current the money saved by stopping points.
Don’t neglect about time. Set targets for the best way quickly factors are mounted after they do happen. This retains the give consideration to fast movement when needed.
Guarantee that targets are affordable. Communicate to crew members to set targets they assume are attainable to achieve.
Making a Roadmap for Implementation
A step-by-step plan helps everyone know what to do. Start with small modifications and assemble as a lot as larger ones.
Select one or two machines to start out out with. This lets the crew apply new methods with out feeling overwhelmed.
Organize a schedule for checking gear. Decide how normally each merchandise needs inspection. Guarantee that these checks match into the standard workday.
Observe workers on new duties, current them spot early indicators of hassle and offers them devices to report what they uncover.
Use a laptop system to hint all repairs work. This helps see patterns and plan future work.
Overview the plan normally. Be ready to change points that aren’t working successfully. Protect talking to the crew to get their ideas for bettering points.
Hazard Administration and Mitigation
Factories should deal with risks when using proactive repairs. This suggests assessing what might go incorrect and planning to forestall points.
One large half is doing hazard assessments for machines. Teams take a look at how probably each machine is to interrupt and the best way harmful it is likely to be if it did. This helps them give consideration to essential gear first.
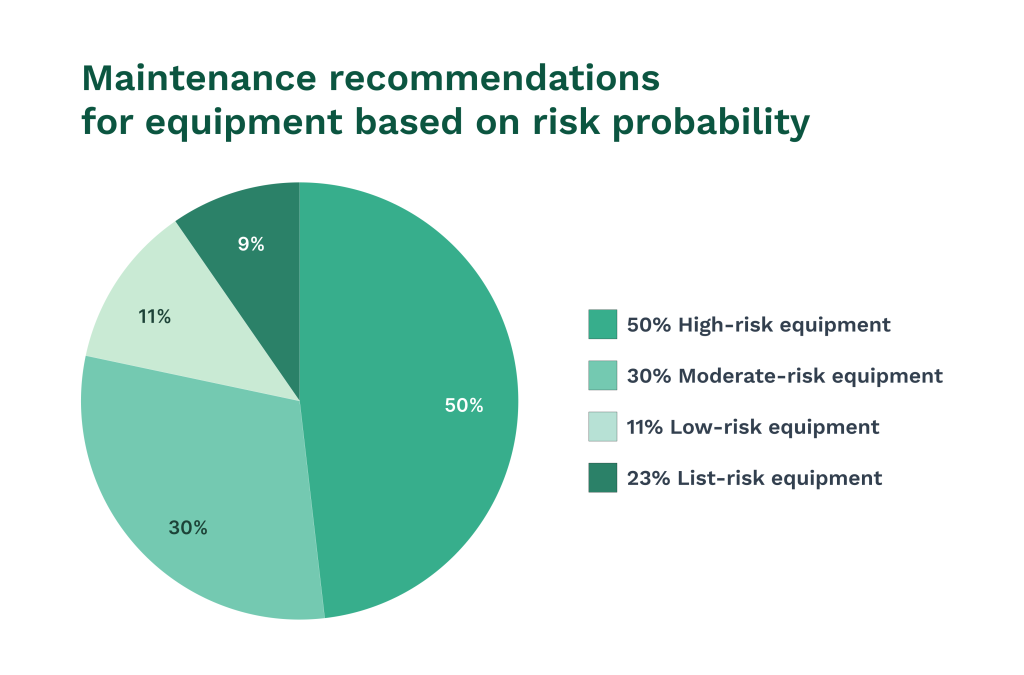
One different key step is making backup plans. If an important machine fails, the manufacturing unit needs a technique to keep up working. This may occasionally suggest having spare components ready or teaching workers on handbook processes.
Data performs an infinite perform, too. By monitoring machine effectivity over time, teams can spot tendencies and restore factors early, lowering shock breakdowns.
Safety is super important in peril administration. Proactive repairs helps create a safety-conscious custom the place workers on a regular basis bear in mind lowering risks.
Some strategies to lower risks embrace:
- Frequent machine check-ups
- Teaching workers on appropriate gear use
- Preserving detailed repairs knowledge
- Using sensors to watch machine nicely being
By specializing in these areas, factories can steer clear of many points sooner than they happen. This retains workers protected and helps the enterprise run simply.
Measuring the Success of Proactive Maintenance
Monitoring and adjusting the exact metrics and KPIs is significant to a worthwhile proactive repairs program. Managers should give consideration to specific effectivity indicators and monitor outcomes over time.
Effectivity Metrics
Managers can use numerous key metrics to gauge the effectiveness of their proactive repairs efforts. One important measure is gear uptime, which reveals how normally machines run in its place of being down for repairs.
One different useful metric is the number of emergency repairs. Fewer rush fixes normally suggest the proactive technique is working successfully. Value monetary financial savings are moreover telling. Managers ought to watch how rather a lot money they save on repairs and replacements.
Asset lifespan will also be worth monitoring. Machines that final extra stage to good repairs practices. Safety incidents can also reveal program success. Fewer accidents would possibly current that gear is in increased type.
Ongoing Monitoring and Adjustment
Monitoring key effectivity indicators is an ongoing course of. Managers ought to rearrange frequent check-ins to evaluation the numbers. This helps spot tendencies and factors early on.
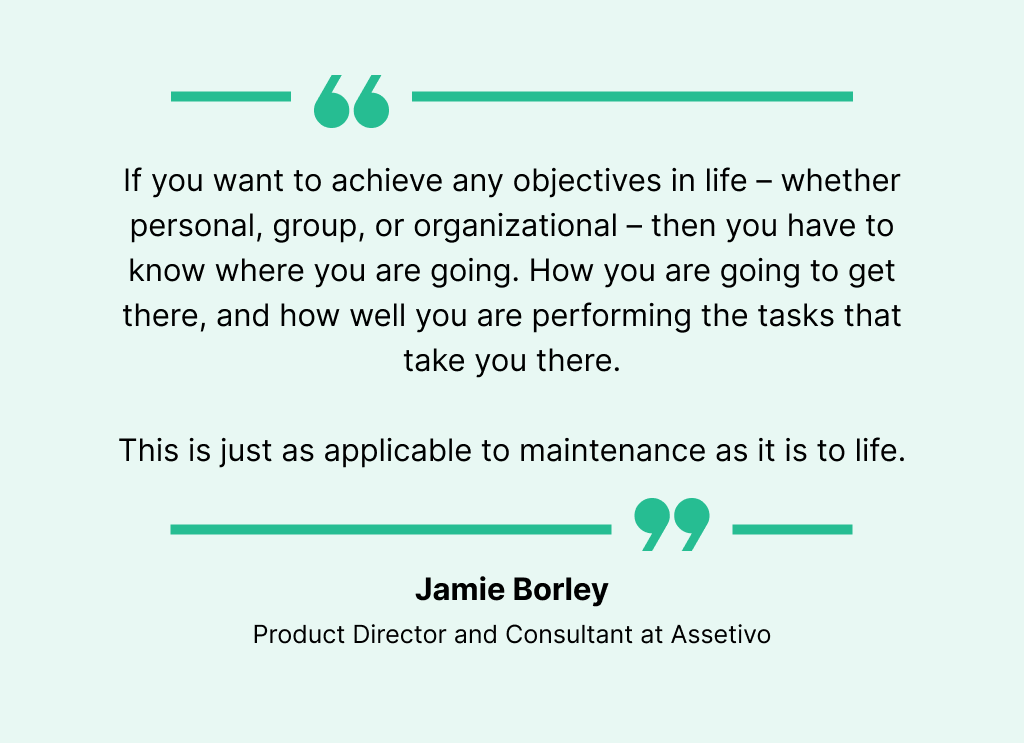
It’s important to be versatile with the maintenance plan. If certain duties aren’t serving to, teams should try new approaches. They might wish to regulate how normally they do inspections or change the sorts of checks they perform.
Getting recommendations from repairs workers is efficient. They normally have insights into what’s working and what’s not. Managers should create easy strategies for workers to share their concepts and ideas for enchancment.
Case Analysis: Proactive Maintenance in Movement
Caterpillar’s journey to predictive repairs reveals how superior tech can change an {{industry}}. They used smart radio applications to watch their gear.
This new technique helped Caterpillar spot points sooner than they grew to change into vital, saving time and cash by fixing points early and sustaining gear reliability.
One different occasion comes from the manufacturing world. Some companies have reduce their repairs costs by as a lot as 28% using proactive methods and improved the smoothness of their operations.
Proper right here’s a quick check out what these companies achieved:
- A lot much less downtime
- Lower restore costs
- Longer gear life
- Happier prospects
Proactive repairs isn’t just for large machines. IT companies use it, too. They take a look at their applications at all times to forestall crashes sooner than they happen.
Even cities and utilities are getting involved throughout the movement.
Hofor
Hofor is a giant Swedish utility agency that carried out a number of of sensors and cameras for 300 Km of heating pipes that run beneath city of Copenhagen.
The company has roughly 40 staff to cope with spherical 60-100 leaks per week. These sensors supplied fast data that the crew might give consideration to. Whereas this technique did not do away with reactive repairs, it did improve uptime.
Conclusion
Proactive repairs brings large benefits however as well as faces hurdles. Firms that want to use it should plan rigorously.
Getting everyone on board is significant. Leaders ought to current why it points. Workers need teaching to make use of recent devices and methods.
Money is normally a disadvantage at first. New tech and sensors worth fairly a bit.
Nonetheless proactive repairs saves money over time by avoiding breakdowns.
Altering earlier habits takes work. Some people need fixing points solely after they break. Persistence and good communication help shift this mindset.
Data factors can sluggish points down. Firms need strategies to collect and use particulars about their machines, and good software program program helps deal with this data.
No matter these challenges, many firms uncover proactive repairs worthwhile. It helps machines final extra and work increased, leading to a lot much less downtime and additional output.
With planning and power, companies can overcome these hurdles. The payoff is smoother operations and reduce costs in the long run.