Get a Free WorkTrek Demo
Let’s current you the way in which WorkTrek would possibly enable you to optimize your repairs operation.
Attempt with out spending a dime
In case you deal with gear, you focus on guaranteeing machines run simply. Two well-liked methods for doing this are proactive and predictive repairs. Whereas they may sound comparable, these approaches have key variations which will impression a company’s bottom line and decreasing unplanned downtime.
Proactive repairs objectives to cease points sooner than they occur, whereas predictive repairs makes use of data to forecast when factors might come up.
Proactive repairs appears to be for the idea motive for potential points. Nonetheless, predictive repairs collects data to schedule fixes on the right time.
Every strategies would possibly assist firms avoid costly breakdowns, lengthen gear life and forestall stunning failures.
By understanding the distinctive benefits of each technique, companies can choose the proper methodology for his or her desires and even combine them for optimum outcomes.
Key Takeaways
- Implementing proactive repairs prevents factors, whereas a predictive repairs approach forecasts them
- Information analysis performs a key place in predictive repairs strategies
- Combining a proactive repairs approach with a preventive repairs approach may end up in easier repairs packages
Defining Proactive Maintenance
Proactive repairs objectives to forestall gear failures sooner than they happen. It makes use of data and analysis to hunt out and restore potential factors early on.
This technique helps maintain machines working simply and cuts down on costly breakdowns.
Traits of Proactive Maintenance
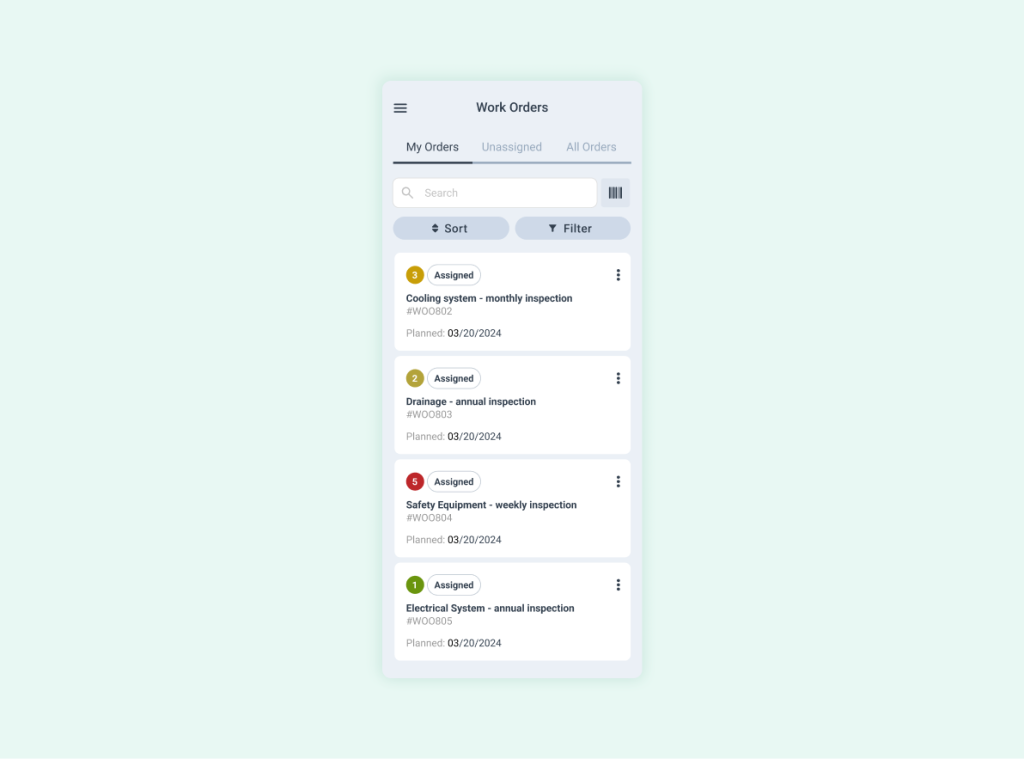
Proactive repairs addresses underlying factors in gear and applications sooner than failure occurs. It depends upon frequent inspections, testing, and monitoring to determine points early to reinforce gear lifespan. Technicians seek for indicators of damage and tear, hurt, or totally different crimson flags that may end in failures.
Preventative Maintenance and Monitoring
Frequent, systematic checks of equipment and applications to ascertain potential factors sooner than they modify into essential failures, along with using sensors, gauges, and visual inspections to hint effectivity metrics and kit circumstances. This may moreover embrace monitoring utilization intervals.
Information-Pushed Selection Making
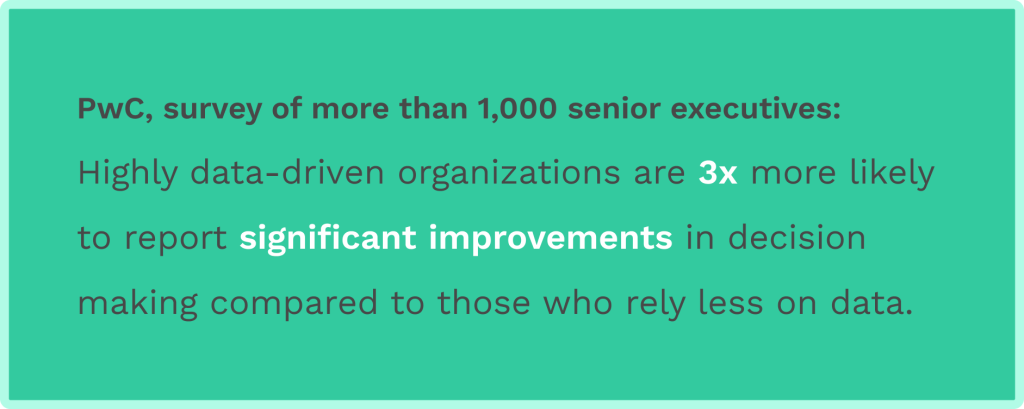
Amassing and analyzing historic repairs data, effectivity tendencies, and kit metrics to predict potential failures and optimize repairs schedules permits organizations to resolve when to hold out repairs actions.
Scheduled Maintenance Actions
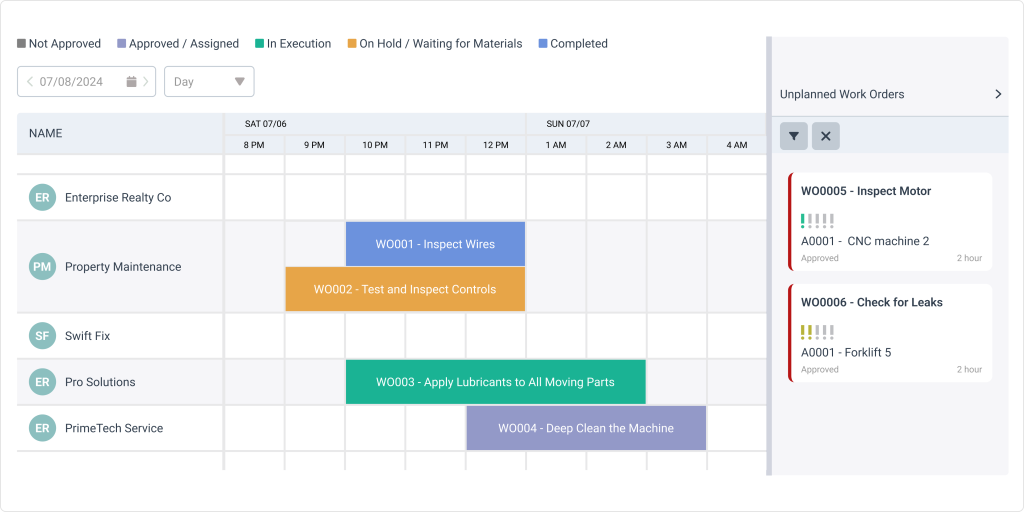
Implementation of routine repairs duties based totally on producer ideas, gear utilization patterns, and historic effectivity data barely than prepared for gear to fail or current indicators of decay.
Inventory Administration and Helpful useful resource Planning
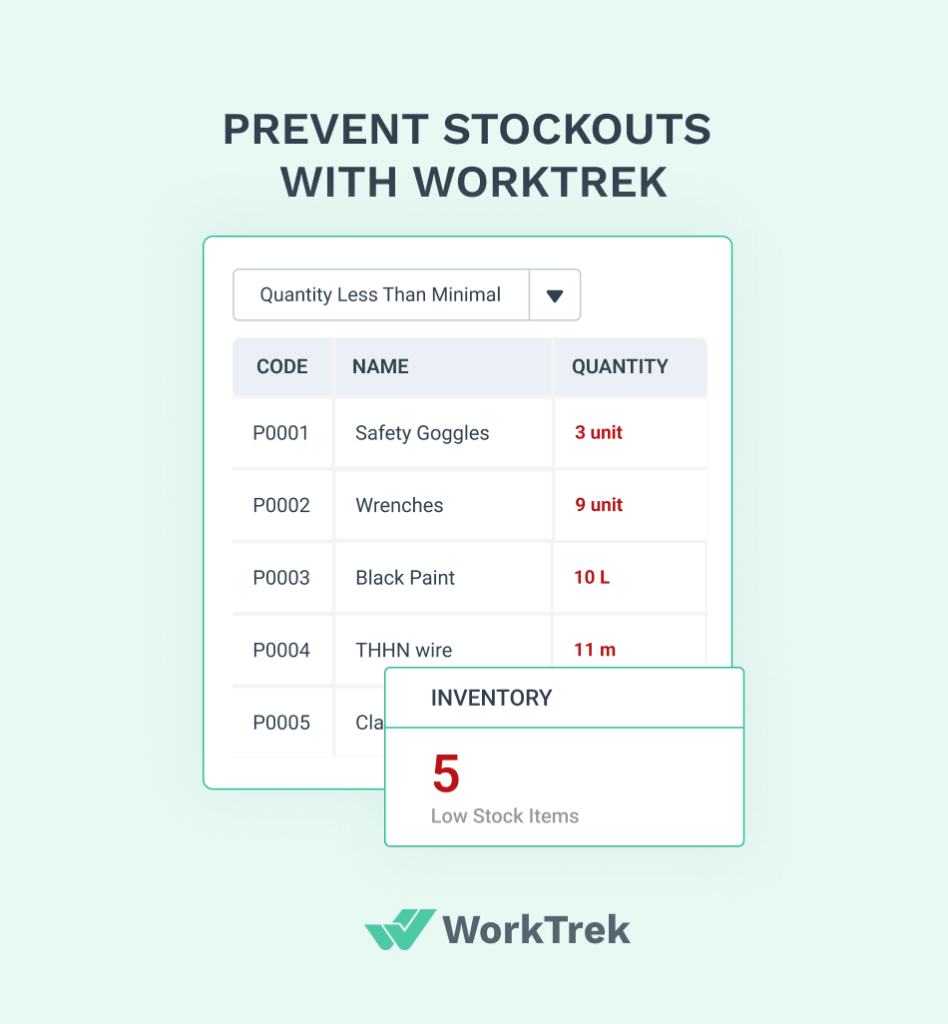
Sustaining optimum ranges of spare parts and scheduling repairs personnel successfully to verify belongings could be discovered when needed, decreasing downtime and enhancing repairs effectiveness.
Documentation and Customary Working Procedures

Progress and maintenance of detailed repairs protocols, gear histories, and standardized procedures to verify consistency in repairs actions and knowledge change amongst workforce members.
Teaching and Expertise Progress
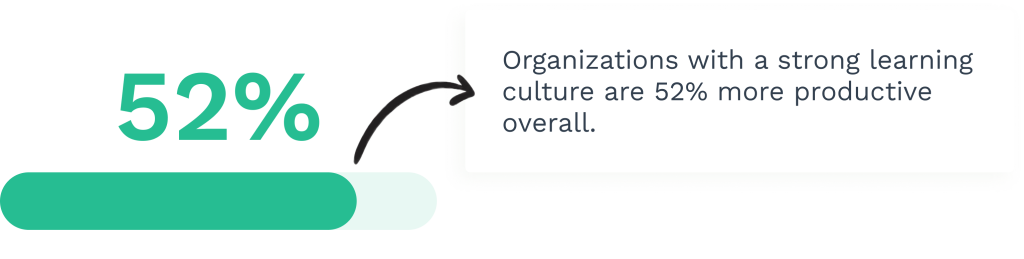
Regular education and training for repairs workers assure they maintain educated regarding the latest utilized sciences, repairs methods, and specific gear requirements. This may enhance the overall effectiveness of the maintenance program.
Regular Enchancment Course of
Generally take into account repairs strategies and outcomes to ascertain areas for enchancment. This consists of analyzing recurring factors and maintenance costs and reviewing historic data and kit reliability metrics to refine and enhance the maintenance program.
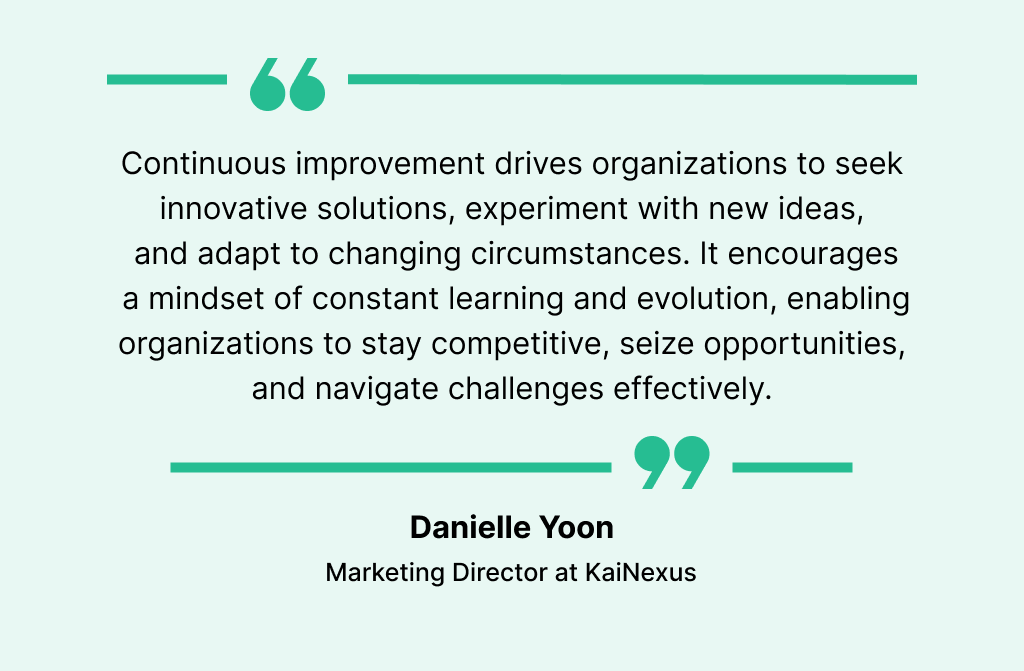
This technique goes previous merely fixing points as soon as they break when conducting repairs. It objectives to boost gear reliability and operational effectivity, lengthen its lifespan, and reduce stunning downtime. Proactive repairs requires a shift in mindset from reactive to preventive pondering.
Benefits of Proactive Maintenance
Proactive repairs presents many advantages for firms. It helps reduce downtime and stunning repairs, enhancing productiveness and lowering repairs costs over time.
Some key benefits embrace:
Worth Low cost and Monetary financial savings
Proactive repairs significantly reduces expensive emergency repairs and unplanned downtime, lowering whole repairs costs. Organizations often save 12-18% compared with reactive repairs strategies, along with diminished further time labor costs and minimized emergency parts procurement.
Extended Gear Lifespan
Frequent monitoring and maintenance help gear operate at optimum circumstances, significantly extending its operational life. Gear that undergoes proactive repairs usually lasts 30-40% longer than gear maintained reactively, representing necessary capital monetary financial savings over time.
Improved Safety and Compliance
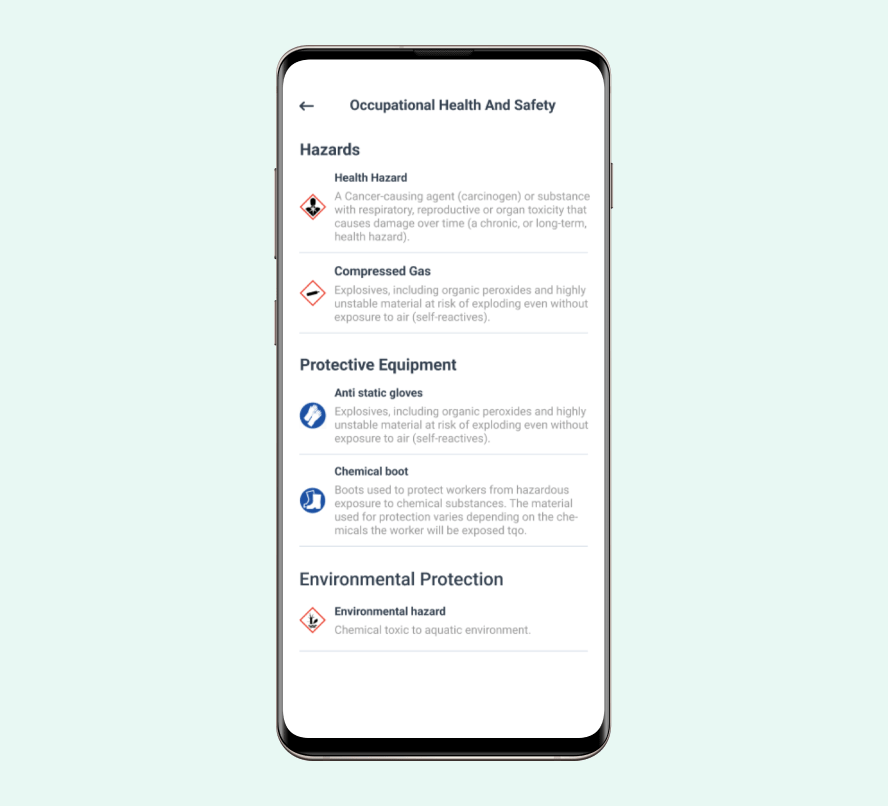
Proactive repairs creates a safer working environment by determining and addressing potential factors sooner than they modify into hazardous. This technique helps organizations protect compliance with safety legal guidelines and reduces workplace accidents related to gear failure by as a lot as 70%.
Enhanced Manufacturing Reliability
Scheduled repairs actions scale back stunning breakdowns, leading to further fixed manufacturing output. Analysis current that facilities implementing proactive repairs strategies experience as a lot as 30% a lot much less downtime than these using reactive approaches.
Increased Helpful useful resource Utilization
Deliberate repairs actions allow for further atmosphere pleasant use of repairs personnel and belongings. Organizations can schedule work all through off-peak hours and better coordinate the availability of parts and technicians, enhancing labor effectivity by as a lot as 25%.
Elevated Vitality Effectivity
Properly-maintained gear operates further successfully, consuming a lot much less vitality and decreasing utility costs. Frequent repairs actions like cleaning, lubricating, and adjusting gear may end up in vitality monetary financial savings of 5-15% yearly.
Bigger Prime quality Output
Gear working at optimum circumstances produces larger prime quality merchandise with fewer defects. Organizations implementing proactive repairs often see a 20-25% low cost in quality-related factors and purchaser complaints.
Proactive repairs moreover helps teams plan their work further efficiently. This technique permits for larger helpful useful resource administration and smoother operations whole.
Defining Predictive Maintenance
Predictive repairs makes use of data and superior analytics to foresee gear factors sooner than they happen. This technique helps firms avoid stunning breakdowns and optimize their repairs schedules.
Traits of Predictive Maintenance
Predictive repairs depends upon real-time monitoring of machine circumstances. Sensors monitor vibration, temperature, and oil prime quality, serving to identify early indicators of damage and tear or hurt.
The target is to restore points at merely the suitable time—not too early, which wastes belongings, and by no means too late, which ends up in failures. Predictive repairs leverages superior analytics to forecast when factors might occur.
This technique can get financial financial savings by decreasing downtime and rising gear life. It moreover improves safety by stopping sudden breakdowns.
Utilized sciences in Predictive Maintenance
A lot of key utilized sciences make predictive repairs potential:
- Net of Points (IoT) sensors
- Big data analytics for analyzing data
- Machine learning algorithms
- Cloud computing
IoT sensors purchase data from machines in real-time. This knowledge is then despatched to extremely efficient pc methods for analysis. Machine learning helps spot patterns that individuals might miss.
Superior data methods help forecast future points. For example, vibration analysis can detect misalignments in rotating gear, and infrared cameras can uncover overheating parts sooner than they fail.
These devices let repairs teams plan and restore factors on the good time. This technique is further actual than setting schedules or prepared for breakdowns.
Key Variations Between Proactive and Predictive Maintenance
Proactive and predictive repairs strategies intention to forestall gear failures, nonetheless their methods and outcomes differ. These approaches fluctuate in how they monitor gear, implement fixes, and impression costs.
Technique and Implementation
Proactive repairs focuses on stopping potential points sooner than they occur. It entails frequent inspections and addressing minor factors early.
Predictive repairs makes use of data and analytics to forecast when gear might fail. It depends upon real-time monitoring and superior utilized sciences.
Proactive repairs is further hands-on and routine-based. Predictive repairs is data-driven and tailored to each piece of equipment’s specific desires.
Gear Monitoring Strategies
Proactive repairs usually makes use of seen inspections, frequent testing, and scheduled half replacements. These methods help catch obvious indicators of damage and tear or hurt.
Predictive repairs employs sensors, data analysis, and machine learning to detect refined changes in gear effectivity. It could set up factors which might not be seen to the naked eye.
This technique permits for a further actual evaluation of potential points. It could predict failures weeks or months prematurely.
Worth Implications
Proactive repairs is likely to be cheaper to implement initially. It requires a lot much less specialised gear and training.
Predictive repairs usually has elevated upfront costs on account of sensor installations and data analysis applications. Nonetheless, it might really end in long-term monetary financial savings by decreasing pointless repairs and stopping principal breakdowns.
Proactive repairs might end in further frequent downtime for routine checks. Predictive repairs can scale back downtime by scheduling repairs solely when needed.
Every strategies intention to reduce the extreme costs of reactive repairs and stunning gear failures.
Understanding Maintenance in Commerce
Maintenance strategies have superior to reinforce gear reliability and reduce costs. Completely totally different phrases are used to clarify repairs approaches in industrial settings.
Evolution of Maintenance Strategies
Throughout the early days of enterprise, repairs was largely reactive. Machines have been fixed solely after they broke down, leading to unplanned downtime and extreme restore costs.
As know-how improved, preventive repairs grew to develop into widespread. Corporations carried out frequent upkeep based totally on set schedules. This helped avoid some breakdowns nonetheless was not always atmosphere pleasant.
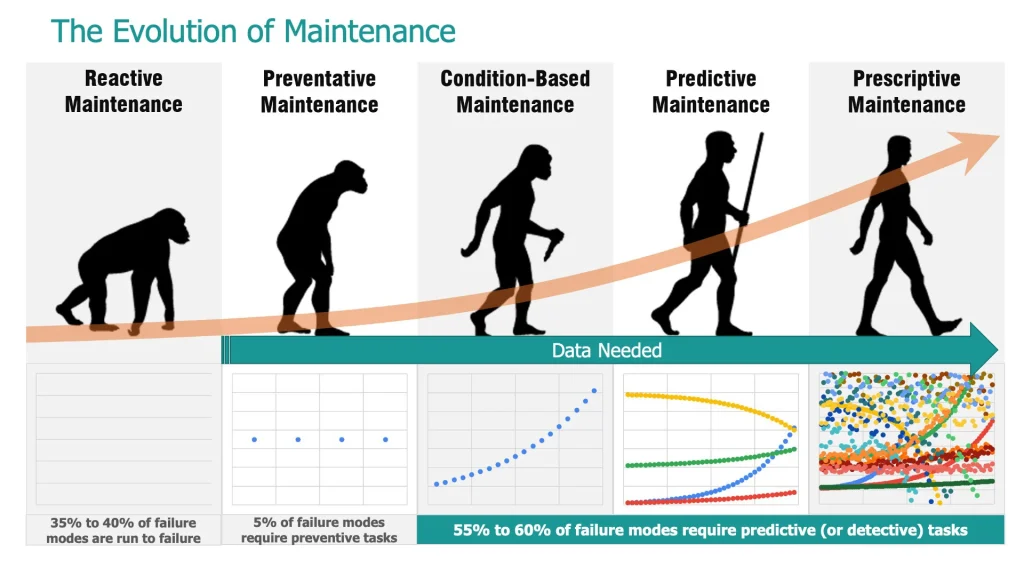
In newest a few years, further superior strategies have emerged. Predictive repairs makes use of sensors and data to determine points to reduce gear downtime, allowing for further targeted repairs.
Proactive repairs goes further. It objectives to cope with the idea causes of equipment factors, which can lengthen machine life and improve reliability.
Every approaches reduce reactive repairs strategies which will end in stunning failures.
Maintenance Terminology
Key repairs phrases embrace:
- Reactive repairs: Fixing gear after it fails
- Preventive repairs: Frequent, scheduled upkeep
- State of affairs-based repairs: Monitoring gear effectively being
- Predictive repairs: Using data to forecast failures
- Proactive repairs: Addressing root causes of points
Indicate Time Between Failures (MTBF) is a vital metric. It measures the everyday time gear runs between breakdowns. A greater MTBF signifies larger reliability.
When there could also be machine failure, downtime refers to intervals when the faulty gear won’t be working.
There are two types of downtime:
- Deliberate (for repairs)
- Unplanned (on account of drugs failures)
Deciding on the Correct Maintenance Method
A lot of key components resolve the effectiveness of a repairs technique. Organizations ought to fastidiously take into account their desires and belongings to seek out out primarily probably the most acceptable approach.
Assessing Organizational Needs
Corporations ought to start by analyzing their gear and property. This consists of making an attempt on the age, state of affairs, and criticality of apparatus.
They need to consider the potential impression of equipment failure on operations and safety. Extreme-risk property might require further superior predictive methods.
Worth vary and accessible know-how moreover play a job. Predictive repairs usually desires specialised sensors and software program program, which is likely to be costly upfront.
Skilled personnel are important. Organizations ought to take into account in the event that they’ve workers who can interpret data and perform superior repairs duties.
Considerations for Small vs. Large Enterprises
Small firms might uncover preventive repairs further doable. It often requires a lot much less preliminary funding and is likely to be easier to implement with restricted belongings.
They will start with main schedules and checklists for gear upkeep. This technique can nonetheless significantly reduce stunning breakdowns.
Large enterprises usually revenue from a mix of strategies. They will use predictive methods for essential property and preventive for a lot much less important gear.
These companies typically have further data to work with. This allows for larger growth analysis and further right failure predictions.
Scalability is important for big organizations. They should choose applications which will develop with their desires and mix all through a lot of locations.
Means ahead for Maintenance: Combining Strategies
Modern repairs strategies combine proactive and predictive approaches with rising utilized sciences. This built-in technique enhances effectivity, reduces costs, and improves enterprise reliability.
Constructed-in Maintenance Approaches
Many companies now combine preventive and predictive repairs methods. This hybrid approach permits for full repairs safety, addressing every frequent upkeep and potential factors sooner than they occur.
Constructed-in applications use data from a lot of sources to make educated decisions. For example, a producing facility might use sensors to observe gear effectivity whereas following a repairs schedule.
This technique helps steadiness costs and benefits. It reduces pointless repairs whereas nonetheless catching points early.
Affect of Rising Utilized sciences
New utilized sciences are reshaping repairs practices. Artificial intelligence and machine learning allow for further right predictions of equipment failures.
Net of Points (IoT) devices current real-time data on asset effectively being. This mounted stream of data helps repairs teams make quick, educated decisions.
Augmented actuality devices assist technicians inside the space. They will instantly entry restore manuals {and professional} suggestion, enhancing restore velocity and accuracy.
Superior analytics help companies optimize their repairs strategies by evaluating sensor data. By analyzing patterns in gear effectivity, firms can fine-tune their technique for max effectivity.
Conclusion
Proactive and predictive repairs every intention to forestall gear failures. They use completely totally different methods to reach this goal.
Proactive repairs focuses on fixing underlying factors. It objectives to forestall points sooner than they start, and this technique usually entails frequent checks and fixes.
Predictive repairs makes use of data and tech to determine factors early. It leverages superior analytics to predict when points might break down.
Every methods can save time and money. They help maintain machines working simply. Corporations might use one or every, counting on their desires.
The choice between them relies upon diversified components. These embrace:
- Gear type
- Worth vary
- How essential the machine is
Some firms mix every approaches, yielding the proper outcomes and allowing for a tailored repairs approach.
The target is to keep up points working successfully and reduce downtime.