Get a Free WorkTrek Demo
Let’s current you methods WorkTrek will make it easier to optimize your repairs operation.
Try with out value
Regarding sustaining industrial gear and companies, reactive repairs – fixing points solely after they break – may appear like a cheap methodology at first look. This textual content covers the best 10 disadvantages of reactive repairs and the way in which it impacts your group.
Nonetheless, this system is usually an expensive gamble in the long run. As industries flip into an increasing number of automated and equipment additional refined, the drawbacks of reactive repairs flip into additional pronounced and financially impactful.
Let’s uncover the quite a few disadvantages of reactive repairs and understand why proactive strategies are necessary in proper now’s industrial panorama.
1. Unpredictable Downtime from Reactive Maintenance Disrupts Operations
In all probability probably the most on the spot and disruptive have an effect on of reactive repairs is sudden gear failure. Emergency repairs is a reactive and urgent kind of repairs that occurs when necessary gear fails unexpectedly, posing a safety hazard or halting manufacturing.
When a necessary machine unexpectedly stops working, manufacturing grinds to a halt with out warning, making a cascade of operational challenges.
Take into consideration a producing plant the place a key assembly line aspect fails all through peak manufacturing hours.
This halts all of the manufacturing course of and creates a ripple impression by means of the provision chain. Employees stand idle, provide schedules are delayed, and purchaser satisfaction suffers.
In distinction to deliberate repairs shutdowns, sudden failures current no various to rearrange numerous manufacturing plans or notify stakeholders. The true worth of this downtime extends far previous the moment manufacturing loss.
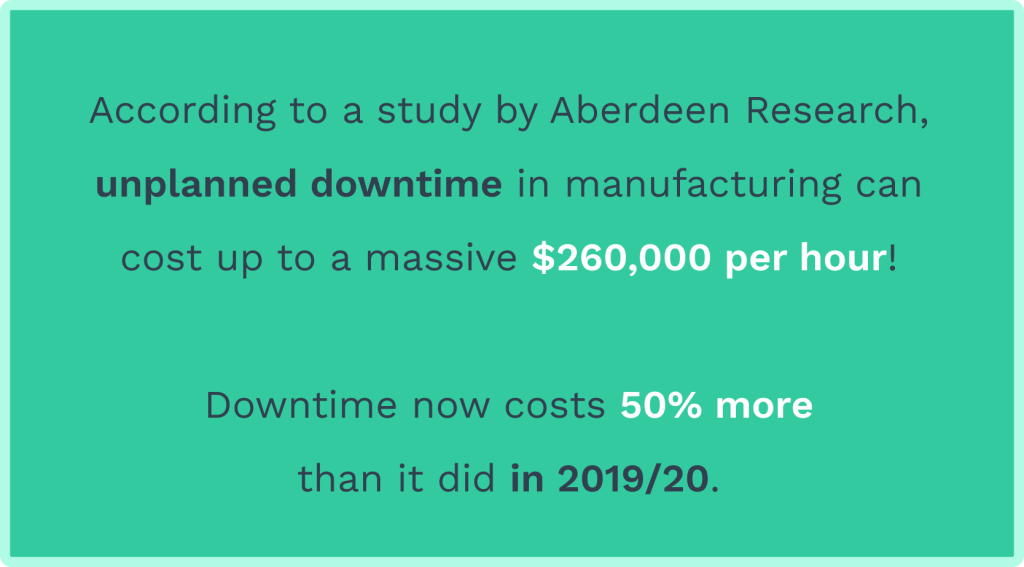
When orders are delayed, purchaser relationships may be damaged, in all probability leading to misplaced future enterprise alternate options.
Employee morale can endure from the stress of fastened catastrophe administration, and the company’s reputation for reliability may be tarnished.
In proper now’s just-in-time manufacturing setting, even a fewhours of sudden downtime can have penalties that reverberate for weeks or months.
2. Better Costs from Emergency Repairs
Emergency repairs just about always worth higher than scheduled repairs, notably when following a breakdown repairs approach, the place gear is repaired solely after failure.
The premium paid for urgent service could also be substantial. When gear fails unexpectedly, organizations often should pay premium prices for rush provide of substitute parts and emergency service calls.
Technicians may should work extra time or all through holidays, incurring additional labor costs which may be two to 4 events the standard value.
As an example, if an HVAC system fails all through a summer season heatwave, the urgency to revive cooling means paying regardless of it takes to get it mounted immediately.
The financial have an effect on goes previous merely the moment restore costs. Rush orders for parts often embody premium transport bills, and the urgency may energy companies to purchase from non-preferred suppliers at higher prices.
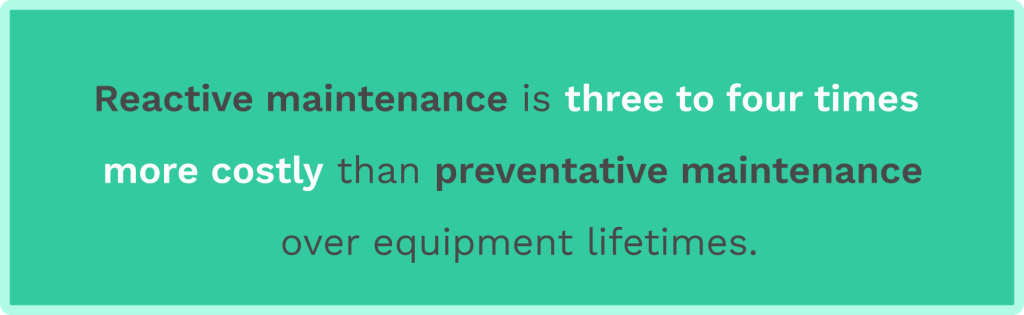
Non everlasting repairs can also be made to get the gear working shortly, necessitating a additional thorough restore later—efficiently paying twice for the same downside.
These emergencies often worth three to 4 events higher than the repairs carried out all through frequent enterprise hours with accurately scheduled repairs.
3. Shortened Gear Lifespan
Gear that solely receives consideration when it breaks down tends to have a significantly shorter operational life, leading to additional frequent capital expenditure on replacements.
Corrective repairs, then once more, addresses system malfunctions proactively sooner than they escalate into full breakdowns.

With out frequent repairs, small factors compound over time, creating additional stress on parts and accelerating placed on.
A straightforward occasion is a bearing that runs with out right lubrication.
What might have been prevented with routine greasing finally led to a catastrophic failure that damaged a lot of associated parts.
The cumulative impression of neglect could also be considerably excessive in superior packages the place parts work collectively.
A minor misalignment in a single half can create a vibration that damages the system’s bearings, seals, and completely different parts.
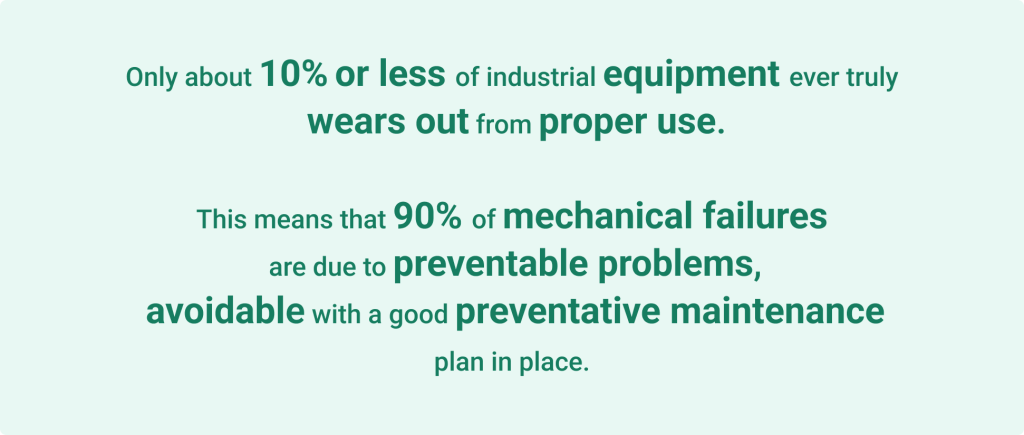
Over time, this cascade of wear and tear and tear ends in premature failure of all of the unit. Analysis have confirmed that gear maintained solely reactively may have diminished helpful life by 30-40% compared with accurately maintained gear.
This premature gear failure means additional frequent substitute of high-priced capital belongings, dramatically rising long-term costs and lowering return on funding.
4. Elevated Safety Risks
Reactive repairs creates dangerous working conditions that put every operators and maintenance personnel at risk.
Reactive repairs means addressing gear failures as they occur with out prior planning or scheduling, allowing for immediate response to sudden factors.
Gear that hasn’t been accurately maintained is additional vulnerable to fail catastrophically, in all probability injuring workers or creating hazardous circumstances.
For example, a poorly maintained stress vessel may develop microscopic cracks that go unnoticed until failure occurs, in all probability releasing hazardous provides or inflicting explosion risks.
Widespread inspections and preventive repairs would catch these factors sooner than they flip into safety hazards.
The safety implications delay previous the moment hazard of equipment failure. Attributable to time stress, repairs personnel working beneath emergency conditions are inclined to take shortcuts or make errors.
They might not have right safety gear obtainable or may skip important safety procedures throughout the rush to revive operation.
This creates a dangerous cycle the place emergency repairs enhance the chance of accidents, which can end in additional emergencies.
The potential costs of worker compensation claims, regulatory fines, and approved obligation could also be monumental.
5. Lower Manufacturing Top quality
Gear working in a deteriorated state often produces lower-quality output sooner than full failure occurs, leading to waste, rework, and purchaser dissatisfaction.
This highlights the disadvantages of reactive repairs, as relying solely on this system can result in extreme enterprise implications and financial costs associated to unplanned repairs and operational downtime.
In precision manufacturing, worn devices or misaligned gear can create delicate defects which might not be immediately apparent nonetheless end in purchaser complaints and rejected merchandise.
This degradation in top quality can damage mannequin reputation and end in misplaced enterprise alternate options, creating costs that far exceed the value of ordinary repairs.
Top quality factors may start subtly and worsen over time, making them insidious. As an example, a packaging machine with worn sealing parts may produce packages that appear acceptable nonetheless have compromised barrier properties, leading to diminished product shelf life.
When these factors are discovered, big parts of substandard merchandise may have already been shipped to prospects.
The value of recollects, returns, and damaged purchaser relationships could also be astronomical compared with the value of frequent repairs that may have prevented the difficulty.
6. Inefficient Helpful useful resource Allocation
The reactive repairs methodology makes it nearly inconceivable to allocate repairs property successfully, leading to higher labor costs and diminished repairs effectiveness.
Maintenance teams ought to persistently shift priorities to deal with the most recent emergency, leaving a lot much less urgent nonetheless nonetheless important duties unfinished.
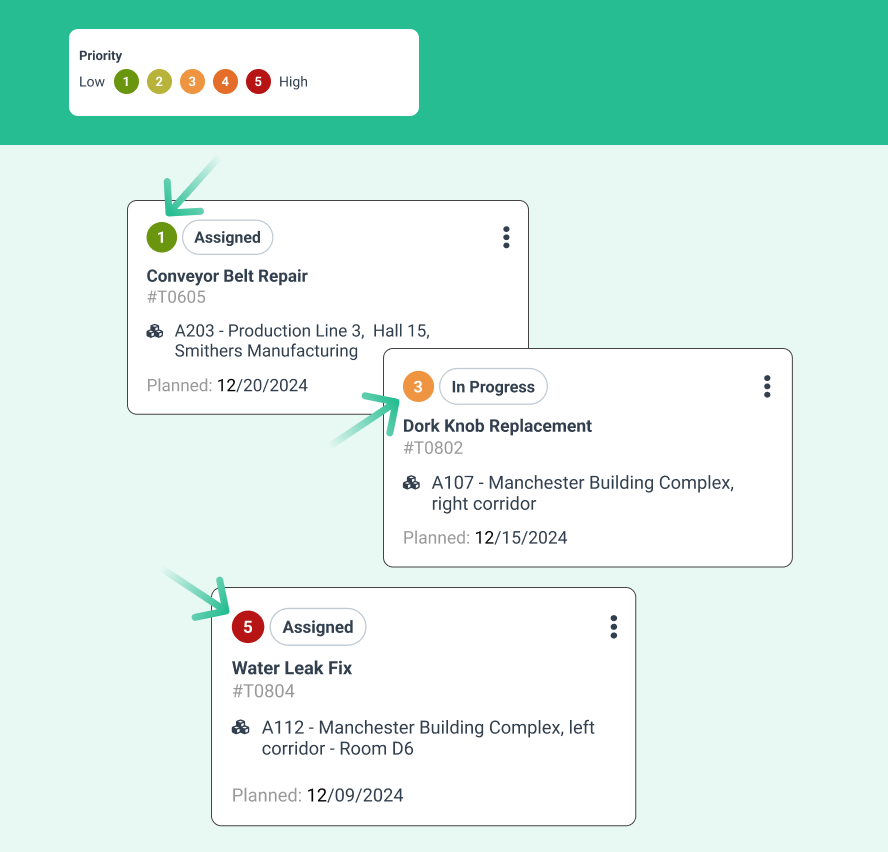
This creates a perpetual catastrophe administration cycle the place technicians can in no way get ahead of points, leading to burnout and diminished job satisfaction.
Parts inventory administration turns into considerably tough beneath a reactive repairs regime.
Organizations ought to each tie up necessary capital in intensive spare parts inventories to cope with any attainable failure or hazard extended downtime prepared for parts to succeed in.
Neither selection is financially optimum. The issue is extra tough because of emergency repairs often require expedited transport and non-standard procurement procedures, which add administrative overhead and enhance costs.
7. Better Energy Consumption
Gear that isn’t appropriately maintained often consumes additional vitality, leading to higher operational costs and elevated environmental have an effect on.
A straightforward occasion is an air compressor with a small air leak. If left unaddressed, the compressor ought to work harder always to maintain up stress, dropping electrical power.
Equally, poorly maintained HVAC packages, manufacturing tools, and autos devour additional vitality when working beneath optimum effectivity.
The have an effect on of elevated vitality consumption could also be substantial.
Analysis have confirmed that well-maintained gear can use 15-20% a lot much less vitality than gear working in a deteriorated state.
8. Lack of Data and Finding out Alternate options
Possibly basically probably the most uncared for downside of reactive repairs is the misplaced various to assemble worthwhile gear effectivity information that may forestall future failures and optimize operations.
When repairs is solely carried out after failure, organizations miss the prospect to hint deterioration patterns and set up early warning indicators that may forestall future failures.
This information may presumably be used to optimize repairs schedules, predict gear lifetime, and make educated decisions about gear substitute.
Fashionable predictive repairs strategies rely intently on historic effectivity information to ascertain patterns and predict potential failures sooner than they occur.
Organizations in no way develop this worthwhile database of equipment conduct and maintenance historic previous in a reactive repairs mode.
This prevents them from benefiting from superior analytics and artificial intelligence devices that may help optimize their repairs operations and reduce costs.
9. Interference with Deliberate Maintenance
Reactive repairs can significantly intervene with deliberate repairs actions, inflicting a ripple impression that disrupts all the maintenance schedule.
When emergency repairs take priority, deliberate repairs duties are generally pushed once more or canceled, leading to a backlog of necessary repairs work.
This creates a repairs demise spiral, the place reactive repairs consumes all obtainable property, leaving no time for proactive repairs duties.
Take into consideration a state of affairs the place a facility has scheduled routine repairs for its HVAC system. Instantly, a necessary piece of apparatus breaks down, requiring on the spot consideration.
The maintenance crew ought to drop each half to deal with the emergency restore, which is delaying the deliberate HVAC repairs.
As additional unplanned repairs come up, the backlog grows, and the crew turns into trapped in a cycle of fastened catastrophe administration.
This reactive repairs methodology disrupts the maintenance schedule and prevents the crew from performing compulsory preventive and predictive repairs.
Over time, this ends in additional frequent gear failures and higher basic repairs costs. Organizations can break free from this cycle by prioritizing proactive repairs strategies and guaranteeing that every one repairs duties are completed successfully and on schedule.
10. Lack of Root Set off Analysis
One necessary drawback of reactive repairs is its tendency to present consideration to fixing the indicators comparatively than addressing the premise purpose behind the difficulty.
When gear fails, the moment function is to get it once more up and working as shortly as attainable. Nonetheless, this methodology often ends in repeated repairs, as a result of the underlying problem stays unresolved.
As an example, if a motor steadily overheats and fails, a reactive repairs approach may include merely altering the motor each time it breaks down.

With out investigating why the motor is overheating, the difficulty will seemingly recur, leading to ongoing gear failures and elevated repairs costs.
In distinction, a proactive repairs approach would include conducting an intensive root set off analysis to ascertain and deal with the underlying problem, equivalent to inadequate air movement or {{an electrical}} fault.
By neglecting root set off analysis, organizations miss the possibility to implement long-term choices that forestall future failures.
This can improve the frequency of emergency repairs and reduces basic gear reliability and effectivity.
Embracing a proactive repairs methodology that options root set off analysis will assist organizations set up and resolve factors at their provide, leading to additional regular and cost-effective operations.
Conclusion: Embracing a New Maintenance Paradigm
The proof in the direction of reactive repairs is compelling and multifaceted. From unpredictable downtime and escalating restore costs to shortened gear lifespans and elevated safety risks, the “restore it when it breaks” methodology proves counterproductive in trendy industrial settings.
Organizations clinging to reactive repairs strategies often uncover themselves trapped in an expensive cycle of emergency repairs, top quality factors, and inefficient helpful useful resource allocation, lastly undermining their aggressive place.
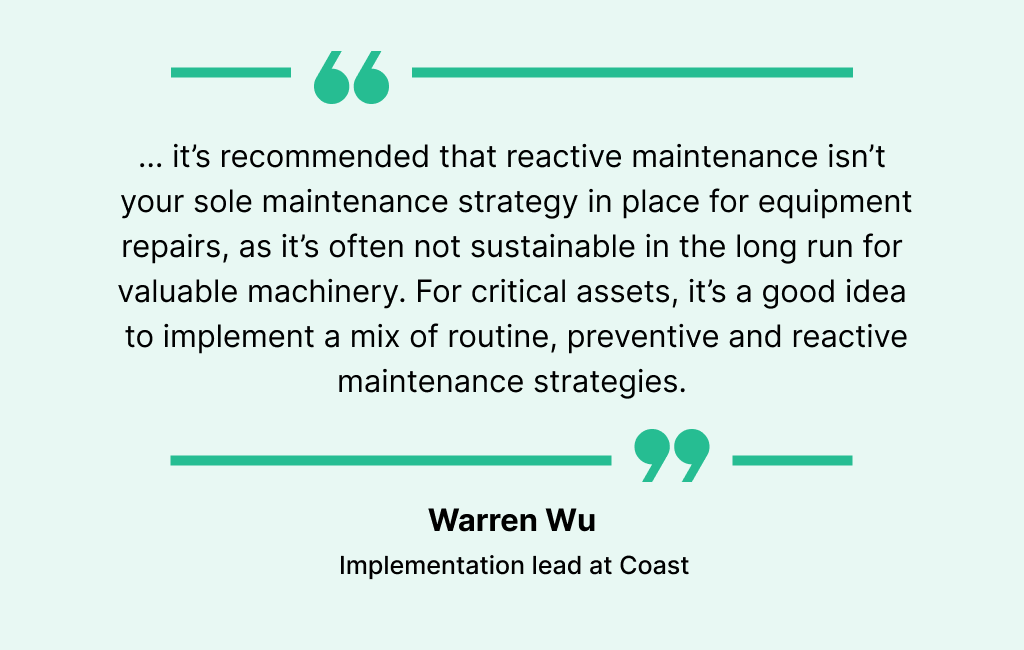
The path forward is embracing proactive repairs strategies that leverage preventive scheduling and condition-based monitoring.
Whereas the transition requires preliminary planning, teaching, and know-how funding, the long-term benefits outweigh these upfront costs.
Organizations that effectively make this shift often experience improved gear reliability, enhanced safety conditions, increased vitality effectivity, and, lastly, stronger bottom-line outcomes.