Get a Free WorkTrek Demo
Let’s current you methods WorkTrek will aid you optimize your repairs operation.
Try for free of charge
Reactive repairs is a technique for repairing gear after it fails or breaks down. It’s completely completely different from completely different varieties that try and cease points sooner than they happen. Some people identify it “run-to-failure” repairs. This technique is customary in plenty of industries and homes.
The type of breakdown repairs can work successfully for some objects.
It’s prone to be good for reasonably priced or easy-to-replace points, nevertheless it’ll most likely set off huge points for very important machines.
Understanding when to utilize it is key to defending costs down and operations working simply.
Key Takeaways
- Reactive repairs fixes gear solely after it breaks down
- This method can be cost-effective for non-critical belongings
- Appropriate implementation requires cautious planning and risk analysis
Understanding Reactive Maintenance
Definition and Fundamentals
Reactive repairs is a way whereby repairs occur after gear fails. It’s moreover referred to as “run-to-failure” repairs. Corporations using this technique don’t perform frequent checks or repairs.
The precept thought is to utilize machines until they stop working ensuing from gear failure.
Then, technicians step in to restore the problem. This will likely decrease your bills on routine repairs costs.
Nonetheless, whereas reactive repairs is widespread in plenty of industries, it’ll most likely lead to additional extended downtimes when stunning points occur.
Sorts of Reactive Maintenance
Reactive repairs encompasses quite a few approaches to addressing gear failures. Understanding these varieties will assist corporations choose the exact method for varied situations.
Emergency Maintenance
Emergency repairs is important to reactive repairs.
The principle goal is on quick responses to stunning gear failures or breakdowns. The type of repairs is essential to cease further damage, assure safety, and cut back downtime.
When an emergency occurs, the maintenance workers ought to diagnose and restore the issue swiftly.
This sometimes entails specialised experience, gear, and belongings, making it additional costly than deliberate repairs.
Nonetheless, the urgency of these repairs justifies the expense, as delaying them would possibly lead to additional very important points.
Emergency Maintenance Conditions
Frequent conditions requiring emergency repairs embrace:
- Repairing a important piece of equipment that has failed unexpectedly
- Responding to pure disasters, similar to floods or earthquakes, which have damaged gear
- Addressing safety hazards, like leaks or electrical factors, that demand quick consideration
Emergency repairs, additionally known as corrective repairs, is normally carried out alongside completely different reactive repairs varieties to revive gear to common working circumstances as quickly and safely as attainable.
Whereas emergency repairs is normally unavoidable, restoring gear to common operation can be disruptive and dear.
Is there a better technique?
One reply is implementing a proactive repairs plan which will help reduce the frequency of emergency repairs.
For instance, preventive repairs entails routine inspections and maintenance carried out duties to ascertain potential factors sooner than they escalate.
This proactive technique can significantly reduce the need for emergency repairs and cut back associated costs and downtime.
Using Information and Analytics
Predictive repairs takes this extra by using data and analytics to forecast when gear will potential fail.
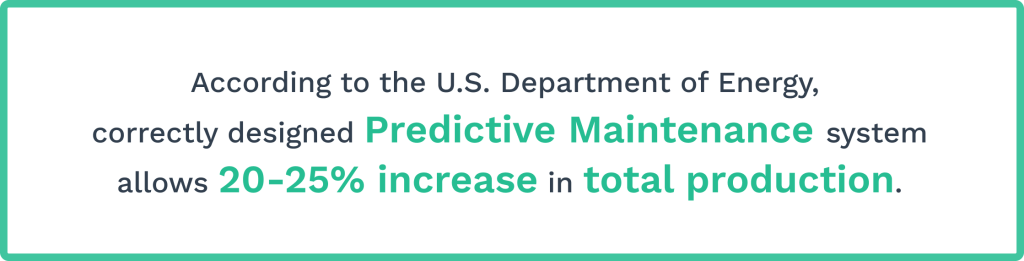
By anticipating failures, repairs teams can perform compulsory duties sooner than a breakdown occurs, lowering the need for emergency interventions.
In summary, emergency repairs is an important a part of reactive repairs, requiring quick movement to take care of stunning gear failures.
By adopting proactive repairs strategies, similar to preventive and predictive repairs, organizations can cut back the need for emergency repairs and assure smoother, cheaper operations.
Evaluating Maintenance Strategies
Reactive repairs is one amongst quite a lot of approaches to gear care sooner than failure occurs. Totally different methods embrace preventive and predictive repairs.
Preventive repairs entails frequent checks and upkeep to avoid breakdowns. A preventive repairs method will assist lengthen machine life nevertheless costs additional upfront.
Predictive repairs makes use of information to guess when repairs is prone to be needed. It might be very environment friendly nevertheless requires explicit devices and experience.
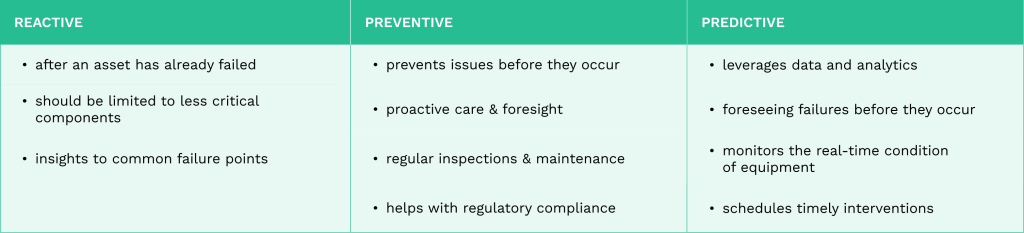
Reactive repairs is normally cheaper initially, nevertheless sudden breakdowns and emergency repairs can lead to better costs.
When Reactive Maintenance Is Related
Reactive repairs technique works biggest for positive situations the place you want to reduce pointless repairs.
It’s acceptable for gear that’s:
- Low-cost to interchange
- Not important to operations
- It is unlikely to set off safety issues if it fails
Some examples embrace:
- Delicate bulbs
- Small office gear
- Non-essential devices
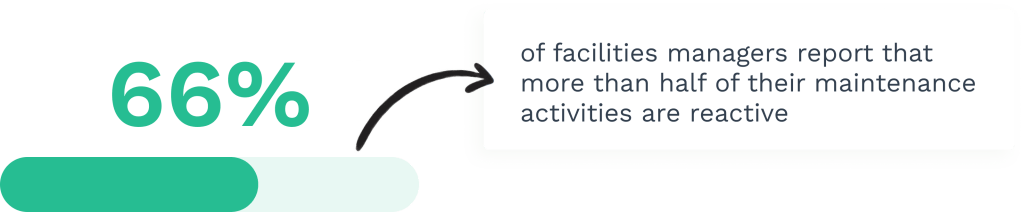
For important machines, reactive repairs can be harmful. It might set off stunning downtime and extreme restore costs.
Firms should weigh the professionals and cons rigorously. The acceptable method relies upon upon the exact gear and agency needs.
Utilizing CMMS for Enhanced Reactive Maintenance
A Computerized Maintenance Administration System (CMMS) like WorkTrek can significantly improve the effectivity and effectiveness of reactive repairs strategies.
By leveraging CMMS, repairs teams can streamline their processes, protect detailed information, and deal with notifications, lastly enhancing their ability to reply gear failures.
Streamlining Reactive Maintenance Processes
CMMS provides a centralized platform for logging and monitoring repairs duties in real-time. When gear fails, technicians can quickly enter restore requests into the system, guaranteeing all workers members know the issue.
This quick logging helps prioritize duties primarily based totally on urgency and accessible belongings.
File Defending and Historic Information
One key good thing about using a CMMS is its ability to maintain up full information of all repairs actions.
Each restore, along with parts used, time taken, and technician involved, is documented contained in the system.
This historic data is invaluable for determining patterns of equipment failures and would possibly inform future repairs strategies, most likely lowering the frequency of reactive repairs needs.
Notifications and Alerts
CMMS strategies have notification choices that alert repairs teams to new restore requests or updates on ongoing jobs.
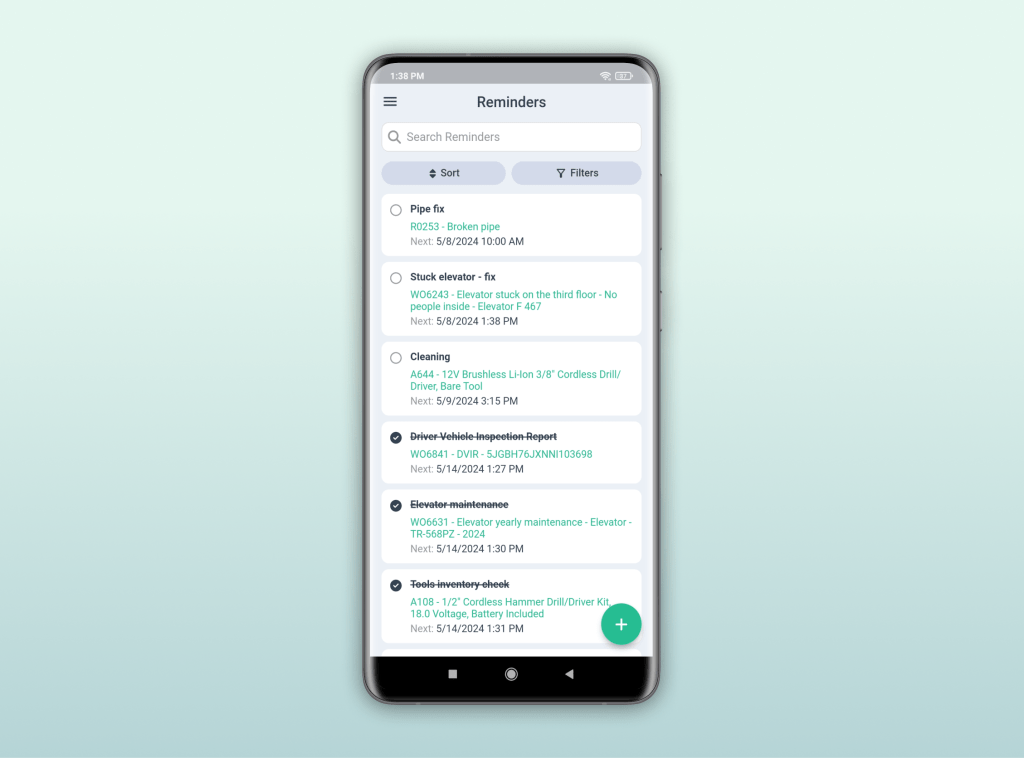
These alerts can be customized to tell associated personnel by the use of e-mail or mobile apps, guaranteeing that no important job goes unnoticed.
This attribute is useful for managing emergency repairs duties, the place swift response situations are important.
Enhancing Communication and Coordination
Environment friendly communication is critical in reactive repairs conditions. CMMS facilitates increased coordination amongst workers members by providing a shared platform for updates and progress experiences.
This ensures everybody appears to be educated regarding the standing of repairs and any priority changes, minimizing downtime and bettering normal response situations.
Reactive Maintenance Processes
Reactive repairs entails explicit processes to take care of gear failures quickly and efficiently. These processes focus on emergency repairs and routine repairs actions.
Emergency Repairs and Procedures
Emergency repairs refers to reacting quickly when gear fails unexpectedly. Technicians ought to first assess the situation to search out out the extent of the damage.
They then set up the idea purpose for the failure. This step is important for implementing the appropriate restore.
Subsequent, technicians acquire the required devices and parts. In some situations, they could need to order specialised components.
Emergency repairs sometimes include momentary fixes to scale back downtime. These quick choices allow operations to resume whereas eternal repairs are deliberate.
Safety is paramount all through emergency procedures. Technicians ought to adjust to strict protocols to protect themselves and others.
Clear communication is essential. Teams need to coordinate efforts and protect stakeholders educated all by means of the restore course of.
Maintenance Actions and Duties
Routine repairs duties are a key part of reactive repairs, with quite a few repairs duties carried out to revive gear to working order.
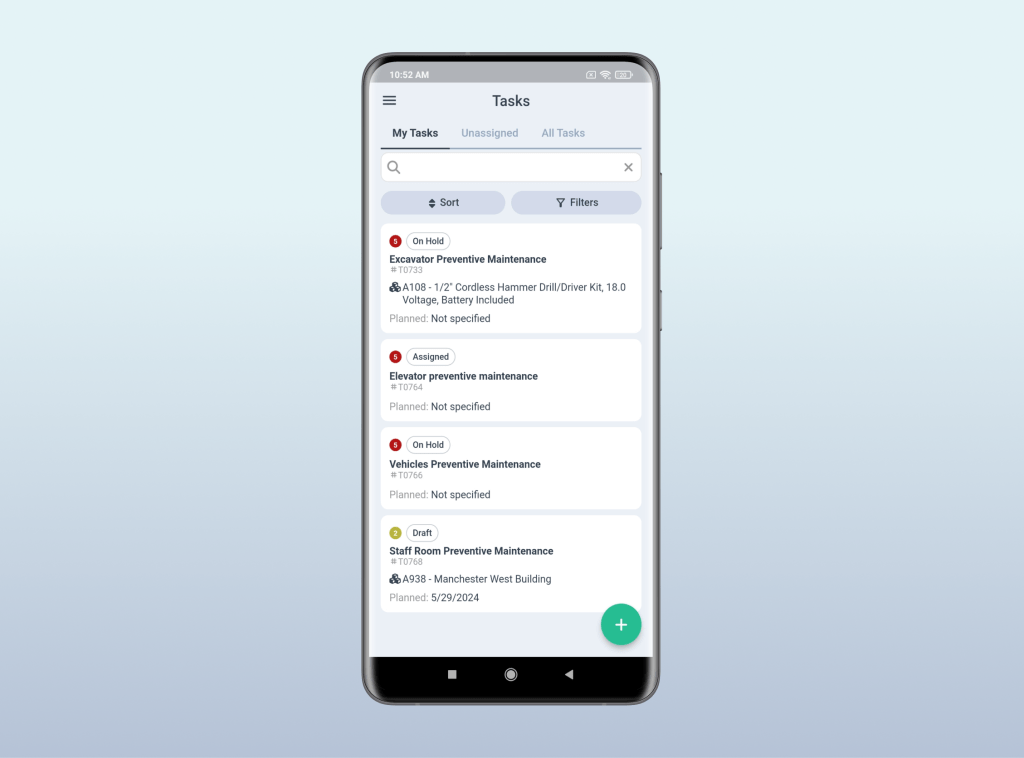
Frequent duties embrace:
- Altering worn or broken parts
- Cleaning and lubricating components
- Adjusting and calibrating gear
- Updating software program program or firmware
Technicians sometimes use checklists to ensure they full all compulsory steps. These lists help preserve consistency and top quality in repairs.
Documentation is important. Technicians report particulars of each restore, along with parts used and time spent.
This information aids in future troubleshooting and helps observe repairs costs.
Widespread inspections might adjust to repairs to ensure the restore was worthwhile. These checks help cease recurring factors and lengthen gear life.
Advantages and Disadvantages
Reactive repairs has every constructive and damaging parts. It presents some benefits however as well as comes with risks and drawbacks.
Benefits of Reactive Maintenance
Reactive repairs can be cost-effective throughout the transient time interval. Corporations spend a lot much less on routine checks and half replacements, and this technique works successfully for non-critical gear.
It requires a lot much less planning and fewer workers. Managers don’t need to create sophisticated repairs schedules; workers can focus on completely different duties when machines run simply.
Reactive repairs is straightforward to know and implement. Small corporations with restricted belongings sometimes use this technique because of it doesn’t need explicit teaching or devices.
Limitations and Risks
The disadvantages of reactive repairs embrace unplanned downtime. Gear failures can instantly halt manufacturing, leading to misplaced time and money.
Reactive repairs will enhance safety risks. Broken machines might set off accidents or accidents, and workers will not be able to take care of sudden breakdowns safely.
Prolonged-term costs can be better. Repairs for severely damaged gear are typically dearer. Machines that aren’t maintained normally generally tend to interrupt down additional sometimes.
This technique typically shortens gear lifespan. Lack of regular care might trigger parts to put on down faster, so companies ought to substitute machines additional ceaselessly.
Affect on Enterprise Operations
Reactive repairs significantly impacts how companies operate day-to-day. It touches many areas, from gear effectivity to financial effectively being.
Downtime and Unplanned Disruptions
Reactive repairs sometimes leads to stunning downtime. When machines break with out warning, work stops instantly. This will likely delay manufacturing and disappoint prospects.
Unplanned disruptions moreover stress staff. Workers ought to scramble to restore factors quickly. This rush can lead to errors or incomplete repairs.
All through these shock breakdowns, frequent enterprise processes get thrown off observe. Teams might need to work further time to catch up, which disrupts schedules and would possibly harm morale.
Worth Implications
The financial impression of reactive repairs is substantial. Emergency repairs usually worth better than deliberate ones, and companies sometimes pay premium prices for rush parts and labor.
Sudden gear failures can result in misplaced product sales and unhappy purchasers. These losses enhance quickly, significantly for corporations that depend upon regular operations.
Prolonged-term costs moreover enhance. Machines that run until they break sometimes need additional intensive repairs. This will likely shorten their normal lifespan, leading to earlier substitute.
Gear and Asset Administration
Reactive repairs strategies make it exhausting to deal with belongings efficiently. With out frequent checks, it’s highly effective to know the true state of affairs of the gear.
This technique can lead to:
- Shortened gear lifespans
- Inefficient use of repairs belongings
- Drawback planning for future gear needs
Poor asset administration can result in stunning capital payments. As an example, companies could need to interchange important gear forward of deliberate.
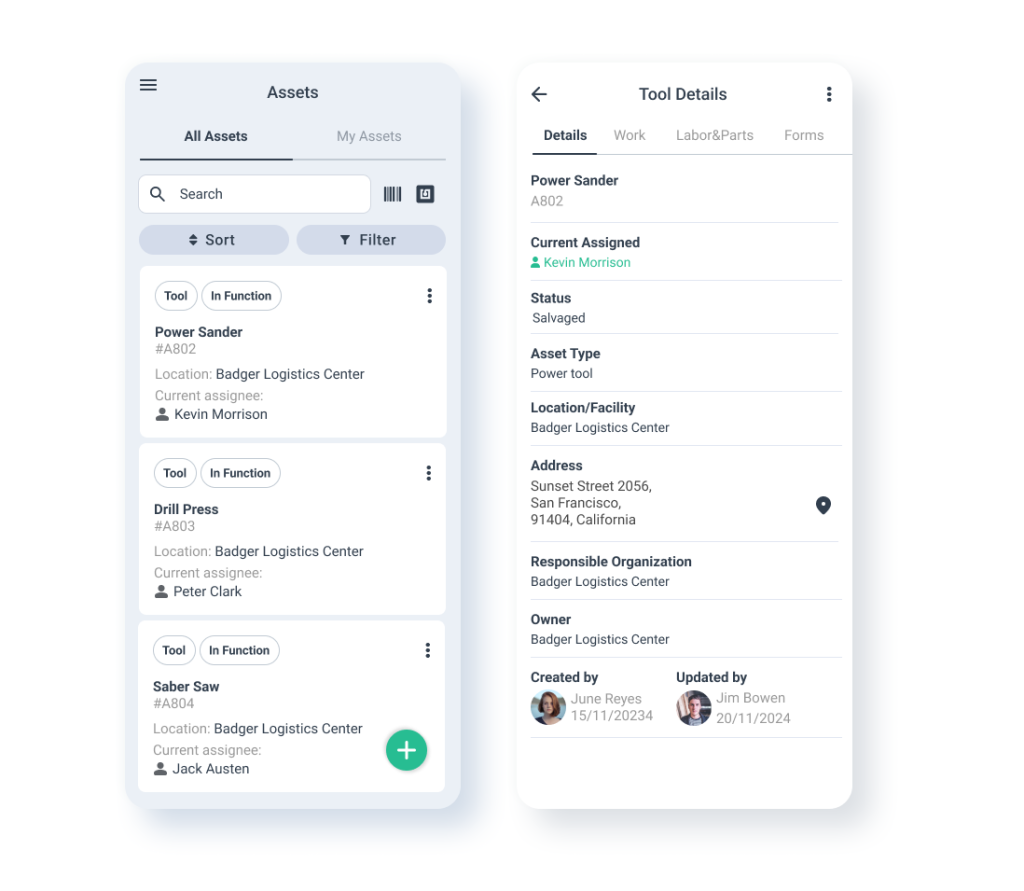
Reactive strategies moreover make optimizing gear effectivity troublesome. Machines might run underneath peak effectivity for prolonged intervals sooner than factors are noticed.
Implementing Reactive Maintenance
Reactive repairs requires a clear workflow and the exact devices. Corporations ought to plan their technique and use software program program to deal with repairs successfully.
Maintenance Workflow and Planning
An incredible reactive repairs plan begins with organising a clear workflow. This helps teams know what to do when gear breaks down.
The first step is to report the problem quickly. Workers ought to tell managers or repairs workers immediately when one factor isn’t working.
Subsequent, the issue have to be assessed. A gifted technician should confirm the gear to search out out what’s fallacious. They should then decide whether or not or not it could be mounted immediately or if additional work is required.
After the analysis, repairs begin. The workers should have entry to widespread parts and devices to restore factors quickly. If explicit parts are needed, a plan must be carried out to get them quickly.
Streamlined response strategies are key to worthwhile reactive repairs. Teams ought to use responding to widespread points to behave quickly when precise factors occur.
Utilizing Maintenance Administration Software program program
Good software program program makes reactive repairs so much easier to take care of. Computerized Maintenance Administration Strategies (CMMS) help teams observe repairs and deal with work orders. These strategies can:
- Log restore requests quickly
- Assign duties to the exact technicians
- Maintain observe of spare parts
- File the restore historic previous for each little bit of equipment
With a CMMS, managers can see what’s being mounted and the best way prolonged it takes. This helps them make increased alternatives about when to interchange gear as an alternative of repairing it.
Mobile apps for CMMS let workers report factors from anyplace. Technicians can entry restore manuals and kit data on their telephones or tablets whereas engaged on fixes.
Run-to-Failure Maintenance
Run-to-failure repairs is a deliberate technique the place belongings operate until they break down. This method entails deliberate non-intervention and cautious asset lifespan evaluation. It might be cost-effective for positive gear varieties.
Concept and Examples
Run-to-failure repairs lets gear operate until it stops working. It’s used when fixing or altering after a breakdown is cheaper than ongoing repairs.
Frequent examples embrace:
- Delicate bulbs
- Disposable batteries
- Printer ink cartridges
- Certain conveyor belts
This technique works successfully for non-critical objects with predictable lifespans. It’s moreover used for gear the place frequent checks could set off additional harm than good.
Executing a Run-to-Failure Approach
To utilize run-to-failure efficiently:
- Choose acceptable belongings
- Plan for quick replacements
- Stock spare parts
- Put together workers on quick response
Deliberate breakdowns can be part of this system. Teams put collectively for eventual failures, guaranteeing minimal disruption after they occur.
It’s important to look at asset effectivity. This helps predict potential failure situations and plan accordingly.
Evaluating the Asset Lifespan
Understanding gear breakdown patterns is important to run-to-failure repairs.
Teams observe:
- Widespread time between failures
- Typical indicators of damage and tear
- Worth of substitute vs. ongoing repairs
- Machine breakdowns
- Productive functionality
- Gear breakdowns
This information helps decide if run-to-failure is cost-effective. For some belongings, it’ll most likely save as a lot as 50% compared with frequent preventive repairs.
Widespread critiques ensure the method stays viable. Completely completely different repairs approaches might grow to be compulsory as gear ages or manufacturing needs change.
Strategic Issues
Choosing the right repairs technique is important for enterprise success. It impacts costs, safety, and operational effectivity. Let’s uncover key parts to ponder.
Deciding on Between Maintenance Approaches
Reactive repairs is biggest for non-critical strategies with low downtime costs. It’s straightforward and requires a lot much less planning. For important gear, preventive or predictive repairs may be increased.
These proactive methods can reduce breakdowns and lengthen asset life. They sometimes worth additional upfront nevertheless decrease your bills in the long term.
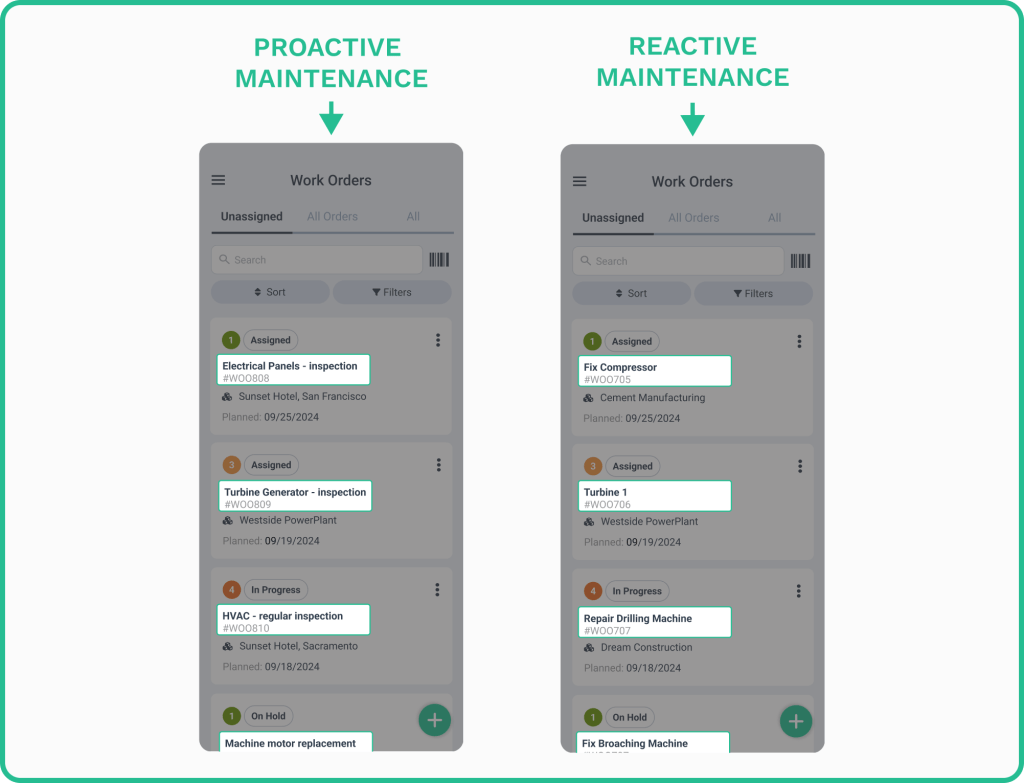
The choice relies upon upon gear value, failure impression, and funds. A combination of strategies sometimes works biggest. Very important machines need proactive care, whereas a lot much less very important objects can use reactive repairs.
Balancing Temporary-Time interval and Prolonged-Time interval Costs
Reactive repairs seems low-cost at first, as a result of it avoids frequent repairs costs. Nonetheless it’ll most likely lead to better long-term costs.
Sudden breakdowns set off manufacturing stops. Emergency repairs are pricey. Gear may need early substitute.
Proactive repairs costs additional initially. It consists of frequent checks and half replacements. Nonetheless it’ll most likely decrease your bills over time by:
- Reducing important breakdowns
- Extending gear life
- Bettering effectivity
- Lowering energy use
Corporations ought to weigh quick monetary financial savings in opposition to future benefits.
Safety and Compliance Factors
Safety risks are an enormous concern with reactive repairs. Sudden failures might trigger accidents or accidents.
Some industries have strict repairs pointers. Reactive strategies that do not meet these necessities might finish in fines or licensed factors.
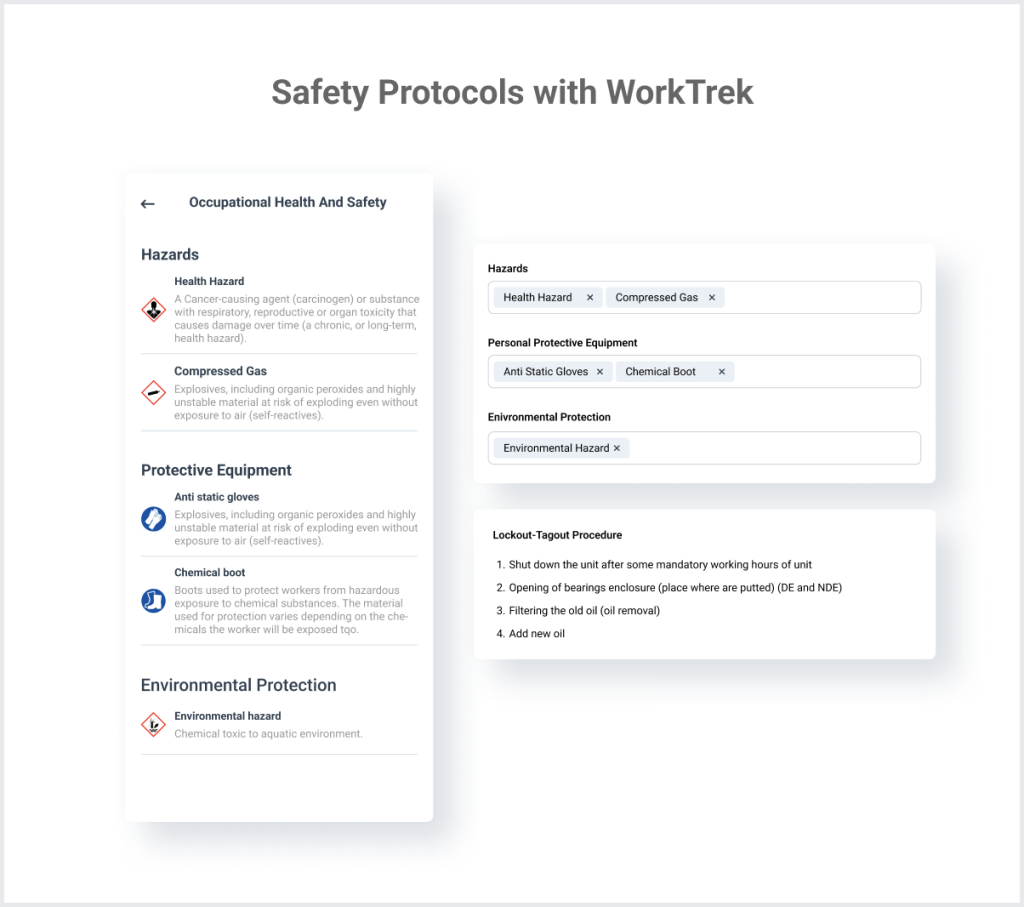
Proactive repairs helps assure safety. It catches points early, reduces accident risks, and retains operations in compliance with legal guidelines.
Widespread inspections moreover create a paper path. This can be very important for audits or investigations.
Safety must be a excessive priority in repairs alternatives. The value of an accident sometimes far outweighs prevention payments.
Case Analysis and Precise-world Features
Reactive repairs performs a key place in plenty of industries. Corporations have realized very important courses from using this technique.
- Reactive repairs is normally a acceptable method for low-cost, non-critical belongings that will not interrupt common enterprise processes after they break down.
- Smaller organizations with restricted belongings might uncover reactive repairs additional potential, significantly when the preliminary costs of preventive or predictive strategies are prohibitive.
- The Nationwide Institute of Necessities and Know-how (NIST) evaluation signifies that, on frequent, 45.7% of kit repairs is reactive.
- Reliability-centered repairs (RCM) signifies that decrease than 10 % of repairs must be reactive, implying that reactive repairs nonetheless has a spot inside a well-balanced repairs method.
Lessons Found from Reactive Maintenance
Many companies have found that the disadvantages of reactive repairs embrace better normal repairs costs.
Reactive repairs can be environment friendly for small, low-cost objects nevertheless harmful for important gear. A producing unit realized this when a key machine failed, stopping all work for days.
Consider using a hybrid technique, like many corporations have completed, to reduce upfront costs.
Perform deliberate repairs on very important machines nevertheless use reactive repairs for a lot much less important objects.
Appropriate monitoring of repairs is important. Implement a CMMS system to help observe your whole restore actions.
This helps spot patterns and decide which objects need additional care.
Conclusion
Reactive repairs is a straightforward technique that addresses gear failures as they occur. Whereas it presents benefits similar to decreased preliminary costs and ease, it moreover presents challenges like unplanned downtime and potential safety risks.
This repairs method is biggest fitted to non-critical belongings the place the worth of downtime is minimal. Nonetheless, relying solely on reactive repairs can enhance long-term costs and reduce gear lifespan.
Many corporations effectively mix reactive repairs with proactive preventive and predictive repairs approaches to optimize repairs efforts.
By doing so, companies can assure important gear receives the required care to cease stunning failures whereas managing costs efficiently for a lot much less vital belongings.
Lastly, the vital factor to a worthwhile repairs program is balancing completely completely different strategies to fulfill explicit operational needs and assure effectivity and safety all through all repairs actions.