Get a Free WorkTrek Demo
Let’s current you methods WorkTrek may enable you optimize your repairs operation.
Attempt completely free
Key Takeaways:
- Higher than half of providers depend upon reactive repairs.
- Preventive and predictive repairs in the reduction of asset failures.
- Over-servicing gear may end up in hurt.
- Skipping repairs for model spanking new property can void warranties.
Have you ever ever ever been knowledgeable to attend until one factor breaks to restore it or that new property don’t should be maintained regularly?
These widespread misconceptions may end up in inefficient practices and pointless downtime.
That’s why at current, we’ll debunk six widespread asset repairs myths.
The fact will empower you to make smarter choices for additional atmosphere pleasant asset repairs.
Let’s get started!
Reactive Maintenance Is Enough for Instruments Reliability
Many teams nonetheless rely on reactive strategies, believing this ensures gear reliability.
Moreover known as run-to-failure, this observe is widespread, with over half of providers using it to deal with their property.
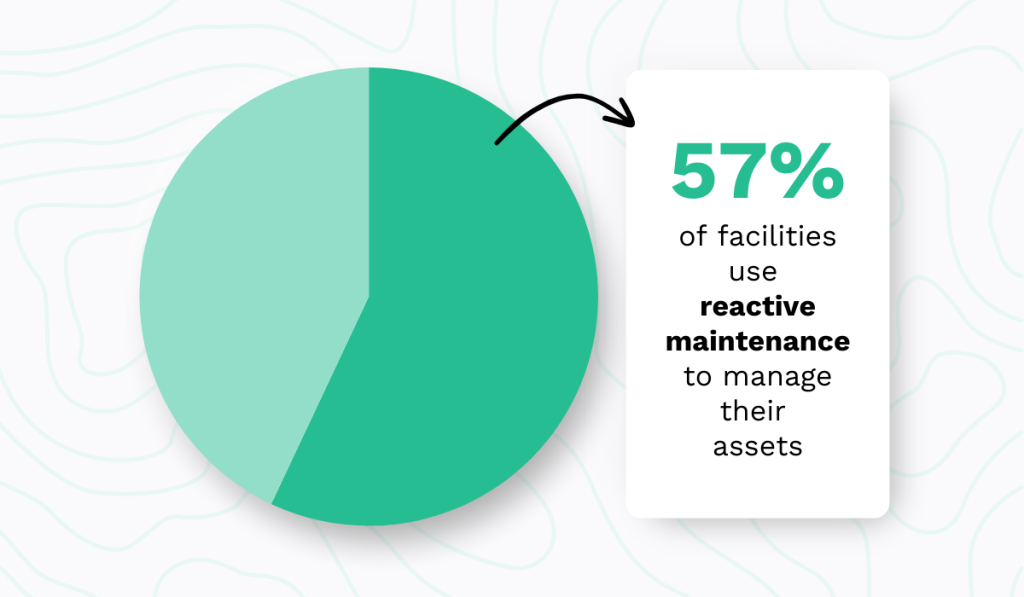
Whereas reactive repairs might be applicable (and is additional helpful) for non-critical, low cost property which will be easy to modify, the difficulty arises when it’s the one method.
Sadly, the equivalent analysis reveals that reactive repairs is the one repairs program for 5% of providers.
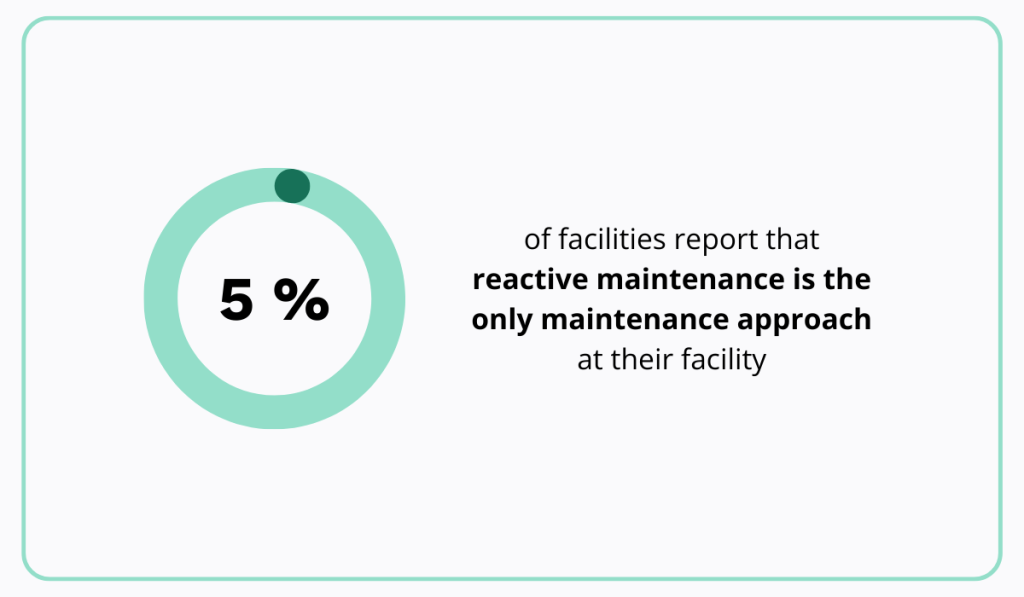
Nonetheless, relying solely on reactive repairs has important drawbacks.
Unplanned failures finish in dear downtime, repairs, and shorter asset lifespans.
Furthermore, sudden breakdowns can create hazardous circumstances for workers, notably in environments involving heavy or difficult gear.
Proactive repairs is a significantly better reply.
Preventive strategies cope with scheduled upkeep to stay away from failures, whereas predictive repairs (PdM) makes use of superior devices to predict factors sooner than they happen.
Every approaches significantly in the reduction of downtime, delay property’ life, and create safer working environments.
On prime of that, it’s less complicated to coordinate teams when repairs is deliberate and scheduled, as one repairs supervisor components out:
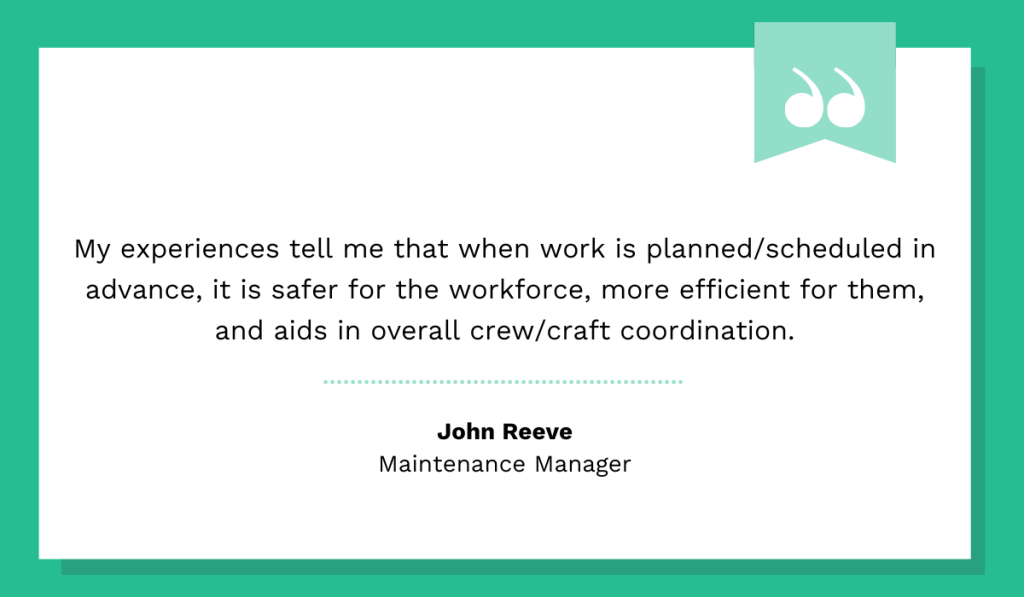
The knowledge moreover confirms the fairly a number of benefits of proactive repairs.
A survey by Superior Know-how Corporations and Plant Engineering Journal from 2020 found that about 70% of respondents reported lower asset failure risks and downtime when using predictive or preventive repairs.
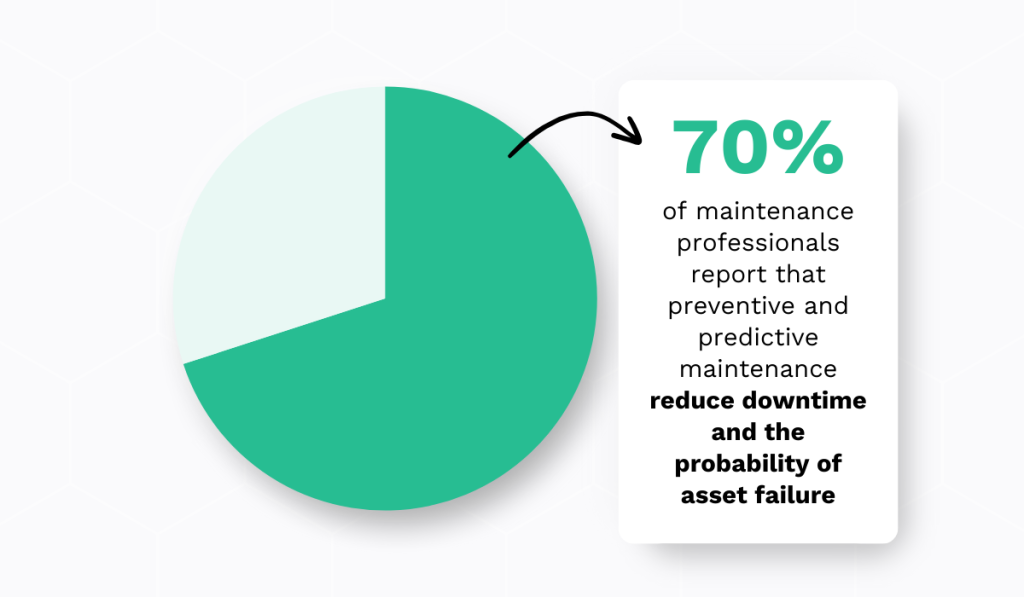
These methods present a greater, additional atmosphere pleasant path forward, proving that reactive repairs alone just isn’t ample for sustaining gear reliability.
Further Maintenance Is Always Larger
Some professionals mistakenly think about that additional repairs is always greater and that frequent interventions improve gear effectivity.
Nonetheless, over-maintaining property sometimes has the opposite impression.
Excessive repairs wastes sources, drives up costs, and even causes pointless placed on and tear on components, shortening their lifespan.
Duncan Aviation, a privately owned enterprise jet service provider, illustrates this clearly.
In aviation, over-servicing engines by repeatedly topping off oil can hurt gearbox seals, inflicting leaks and visible streaking on engine cowlings.
On this case, over-servicing does additional harm than good, unnecessarily grounding airplane and inflating costs.
The upper technique is data-driven repairs, the place the exact needs of the gear info choices.
Devices like state of affairs monitoring and predictive analytics allow repairs teams to judge these needs.
Industries like aviation and manufacturing present the importance of data-driven repairs.
For instance, GE Aerospace, a world chief in jet and turboprop engines, makes use of superior information analytics to stay away from pointless repairs and assure its engines work fully.
Patrick Ketelaar, former Principal Engineer at Distant Monitoring & Diagnostics and current GEnx-2B Product Chief, explains their mission:
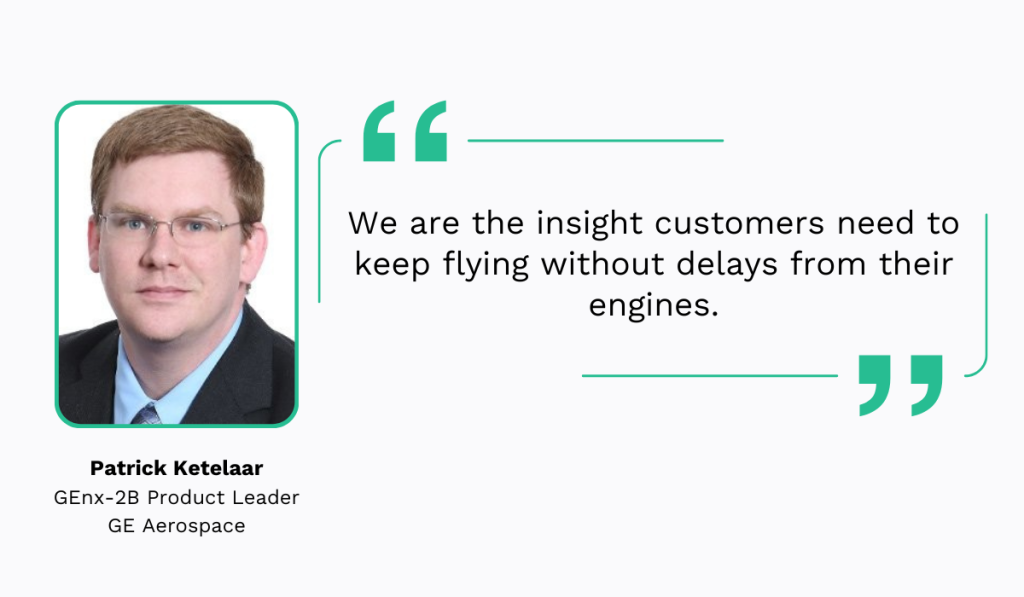
By real-time monitoring and diagnostics of over 38,000 jet engines, their system identifies potential factors akin to irregular exhaust gas temperatures or oil utilization traits.
When factors are detected, they immediately notify their prospects (airways) to behave.
This properly timed and data-driven technique to repairs prevents the wear and tear and tear and tear introduced on by excessive repairs whereas saving airways 1000’s and 1000’s of {{dollars}} yearly.
In the long term, the perfect repairs simply is not about doing additional nonetheless about doing what’s needed when it’s needed.
Information-driven strategies help stability the scale.
Preventive Maintenance Ensures Zero Failures
Preventive repairs is a confirmed method for lowering gear failures nonetheless not eliminating them.
Even with strict schedules and adherence to producers’ pointers, surprising factors can nonetheless happen.
For instance, a producing plant could adjust to rigorous preventive repairs for its motors nonetheless experience an shocking failure on account {of electrical} surges or supplies fatigue that weren’t detectable all through routine checks.
GE Aerospace brings one different occasion on this context.
In a single case, mechanics addressed an issue flagged by routine repairs (better than common nacelle temperatures), nonetheless they couldn’t uncover the set off:
With out understanding notably what was responsible for the higher temperature, the problem wasn’t found by mechanics instantly.
Fortunately, on this case, regular information monitoring acknowledged a stress line leak as the explanation for irregular temperatures.
As quickly because the faulty factor was modified, the engine effectivity returned to common.
So, to deal with the restrictions of preventive repairs, many corporations are turning to predictive devices, information analysis, and state of affairs monitoring for additional atmosphere pleasant processes.
From telematics in fleets to vibration analysis in wind mills or thermal imaging in HVAC strategies, predictive devices complement preventive repairs and fill the gaps it may’t sort out.
Tim Richards, gear supervisor at Sargent, a contractor from Maine, highlights this profit for his or her agency:
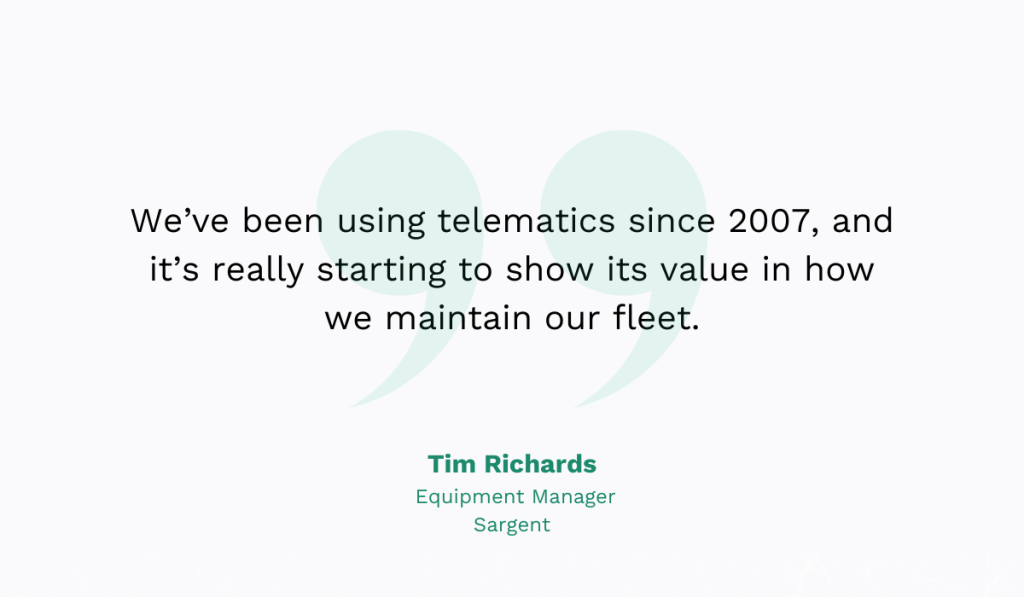
One among Sergent’s key strategies is using HCSS Equipment360, a telematics reply built-in into most of its gear.
It provides real-time information on machine effectivity, fault codes, and restore intervals, serving to them greater maintain autos and in the reduction of shocking downtime.
Ultimately, no repairs method can take away failures.
Nonetheless, combining preventive repairs with predictive devices and state of affairs monitoring is among the finest safety.
New Property Don’t Need Maintenance
The concept new gear requires no repairs is a dear misunderstanding.
Whereas it would sound logical that brand-new property will perform flawlessly, skipping repairs early on can nonetheless lead to shocking breakdowns, diminished effectivity, and even assure voids.
Producers sometimes specify repairs schedules to honor warranties, making routine repairs non-negotiable.
And they also moreover seek for repairs information.

So, not following their pointers and by no means defending information could finish in repairs or replacements being denied beneath assure, rising your costs significantly.
Take conveyor strategies for instance.
Even for a brand-new conveyor belt, frequent repairs is important.
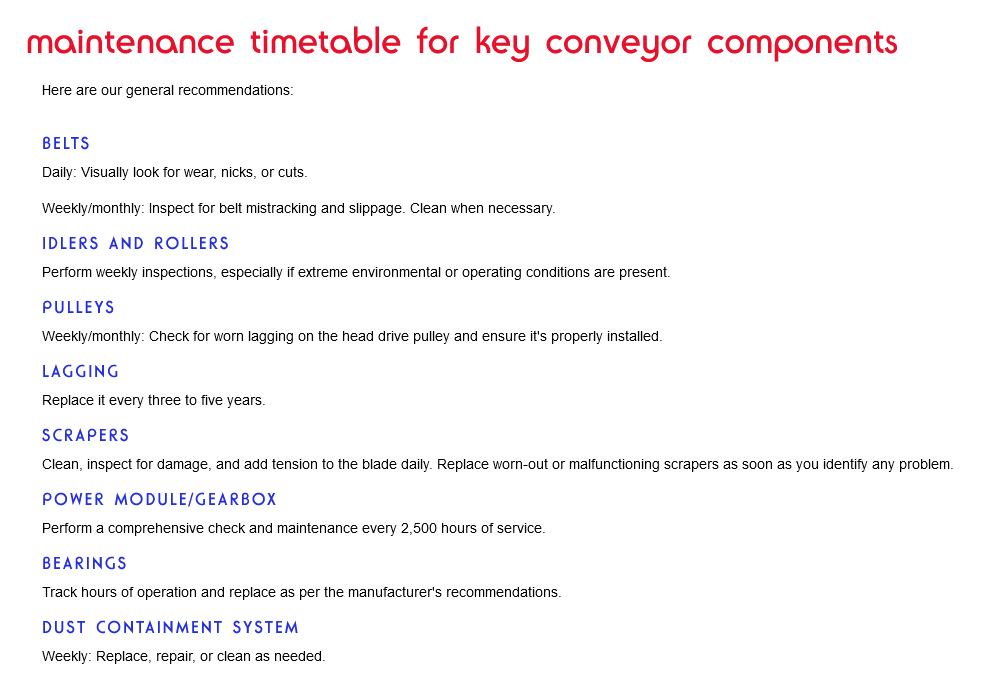
Each day inspections to determine placed on, nicks, or cuts in belts are necessary to forestall hurt.
Weekly or month-to-month checks for belt mistracking, slippage, and scraper blade rigidity are moreover important to ensure the system options simply.
Refrain from following these steps even when the conveyor system is brand-new could finish in early failures, akin to misaligned belts inflicting excessive placed on and even catastrophic breakdowns that halt manufacturing.
The assumption that “it’s new, so it doesn’t need consideration” could value corporations dearly in downtime and restore payments.
The fact is that repairs of latest property ought to begin even sooner than property are put in in your facility.
Mark Lamendola, an skilled in repairs administration, agrees:
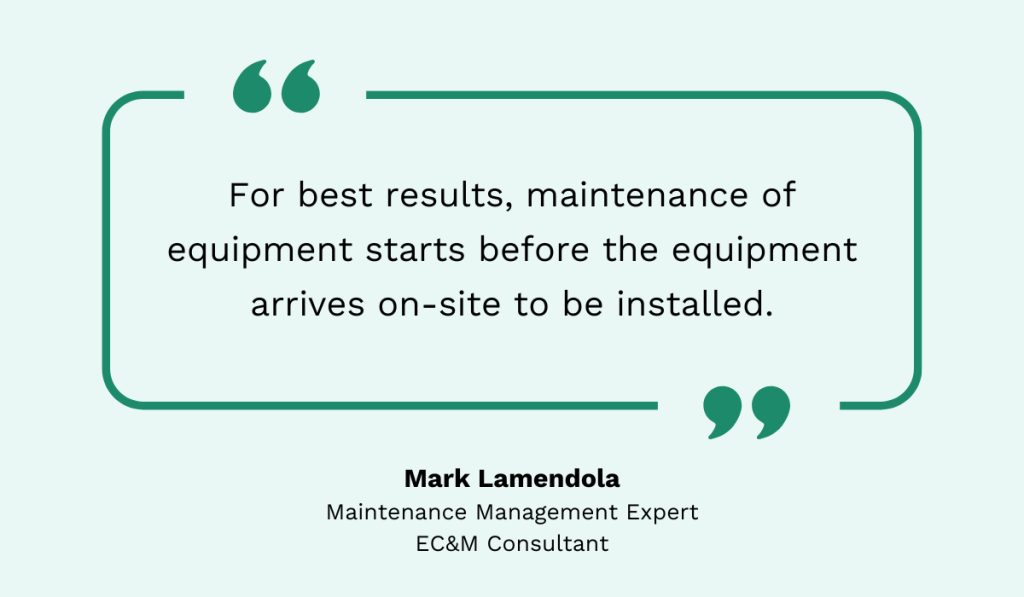
He has preparatory duties in ideas, akin to coming into property proper right into a CMMS, scheduling manufacturer-recommended repairs, and accumulating baseline information.
These straightforward duties lay the groundwork for environment friendly future repairs.
As an illustration, performing preliminary repairs at start-up offers you with a benchmark for detecting effectivity modifications all through subsequent checks.
Conversely, lacking it might properly go away you with baseline information, making it less complicated to determine irregular placed on traits.
All in all, repairs from day one protects your funding, ensures compliance with warranties and models the muse for an prolonged and additional reliable asset lifecycle.
Don’t skip it.
Spare Components Must Always Be on Hand
When a machine breaks down and spare elements are unavailable, manufacturing halts, costs rise, and downtime can stretch longer than essential.
Nonetheless do it’s a must to maintain 100 extra bearings or fifty couplings on the shelf, merely in case?
Fully not.
Whereas important spares should be accessible, overstocking ties up capital and can enhance storage costs.
And however, many repairs professionals fall into this entice, as well-known by Dr. Anthony Kenneson-Adams, a former Royal Air Energy Senior Engineering Officer:
Too sometimes I see 5 years’ value of bearings or couplings on a shelf whereas the maintenance supervisor is struggling to go looking out the funds to buy one other factor or service.
The smarter technique is to undertake an optimized inventory method based mostly totally on asset criticality and demand.
Dr. Kenneson-Adams extra advises determining important property and establishing true min/max in your storeroom.
Proper right here’s what he suggests:
- Start by determining your important property by an asset criticality analysis.
- Classify spare elements into important, necessary, and non-critical courses.
- Use devices like failure mode and outcomes analysis (FMEA) or failure reporting and criticality analysis (FRACAS) to prioritize which spares actually need fast availability.
- Leverage reliability information, akin to indicate time between failures (MTBF) and indicate time to revive (MTTR), to refine stock ranges.
- Use inventory administration strategies like just-in-time (JIT) and arrange clear minimal/most thresholds for each spare.
Aside from, CMMS like WorkTrek can warn you when inventory ranges drop beneath predefined thresholds.
This style, it’s possible you’ll streamline inventory administration and assure spare elements are ordered on time.
CMMS moreover outlets your whole repairs information, so it’s possible you’ll additional exactly predict future spare elements needs.
These helpful CMMS benefits carry us the ultimate fable we should always debunk at current.
CMMS Isn’t a Necessity
Certainly one of many best myths in repairs administration is {{that a}} computerized repairs administration system (CMMS) is pointless.
Many corporations think about they will deal with and never utilizing a CMMS, sometimes on account of misconceptions akin to:
- Some actually really feel that CMMS choices are too expensive, notably for small corporations.
- Others worry regarding the time and effort needed to teach staff
- Or fear they’ll need dear {{hardware}} upgrades.
- Staff could also be reluctant to vary from acquainted processes to at least one factor new.
- Some think about that CMMS platforms are difficult and exhausting to utilize.
Whereas these components may appear respectable, they’re faraway from the very fact of at current’s CMMS choices.
Implementing a CMMS requires time and sources, nonetheless at current’s strategies are designed to be user-friendly and scalable.
Fashionable CMMS choices, notably cloud-based ones like WorkTrek, require minimal infrastructure.
WorkTrek can, as an illustration, be accessed from models you already have—whether or not or not a desktop, tablet, or smartphone.
With subscription-based pricing fashions, the upfront value is often lower than anticipated, and corporations can pay only for the models of choices they need, making it an fairly priced alternative.
The exact value of a CMMS lies in its talent to streamline operations, enhance work order monitoring, lower downtime, and help data-driven choices.
Furthermore, a CMMS allows you to merely plan and schedule preventive repairs.
A well-implemented CMMS improves technician safety by providing clear, detailed repairs instructions, safety hazards, PPE requirements, and so forth.
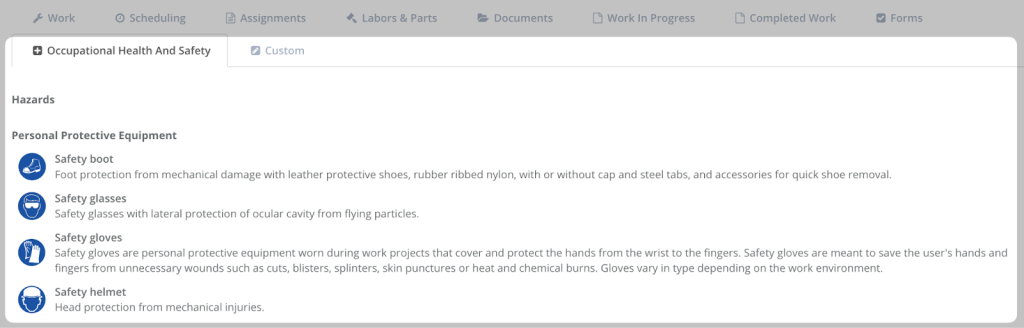
All these benefits collectively far outweigh the preliminary funding and power.
Nonetheless don’t merely take our phrase for it.
In accordance with the ATS analysis, 74% of corporations using a CMMS say it boosts their productiveness.
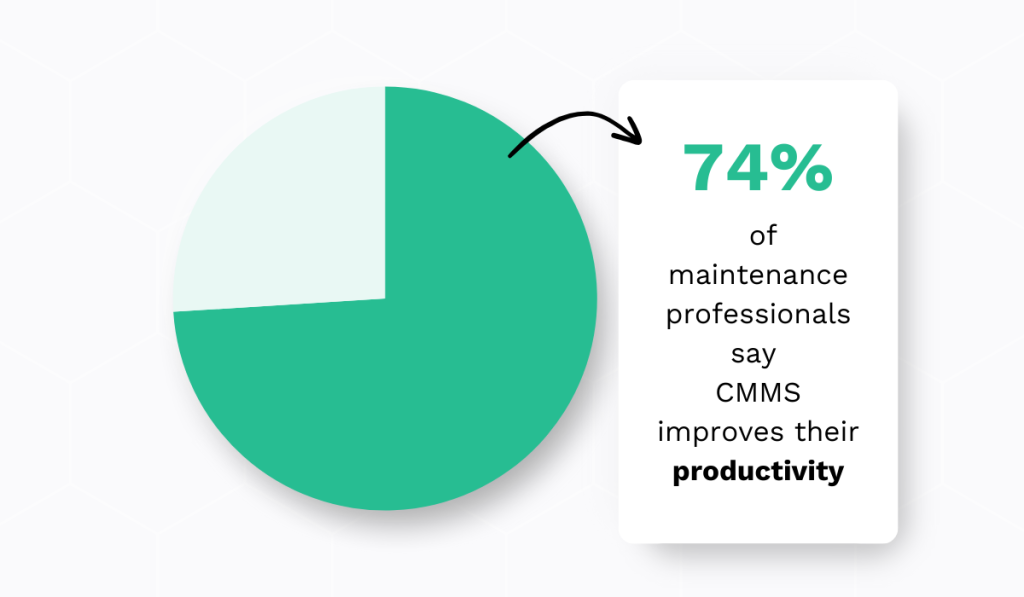
Moreover, a minimal of half of them say {{that a}} CMMS improves OEE, whole effectivity, safety, flexibility, usability, and uptime and has good ROI whole.
Given all this, a reliable CMMS is becoming an precise necessity.
Conclusion
What variety of of these asset repairs myths have you ever ever encountered or unknowingly believed?
If even one, it’s time to rethink your technique.
The fact is that environment friendly repairs strategies don’t merely in the reduction of costs—as well as they create a safer work setting.
It’s time to depart the myths behind and take administration of your asset repairs.