Get a Free WorkTrek Demo
Let’s current you methods WorkTrek might also enable you optimize your repairs operation.
Try with out price
Inside the sophisticated world of business operations, machine repairs represents a essential intersection of human expertise and mechanical packages. This machine repairs safety data explores the essential components of safely sustaining gear, offering deep insights into the procedures and protocols that protect personnel and instruments.
Ensuring the safety of repairs crews is paramount to sustaining operational effectivity and defending every personnel and instruments
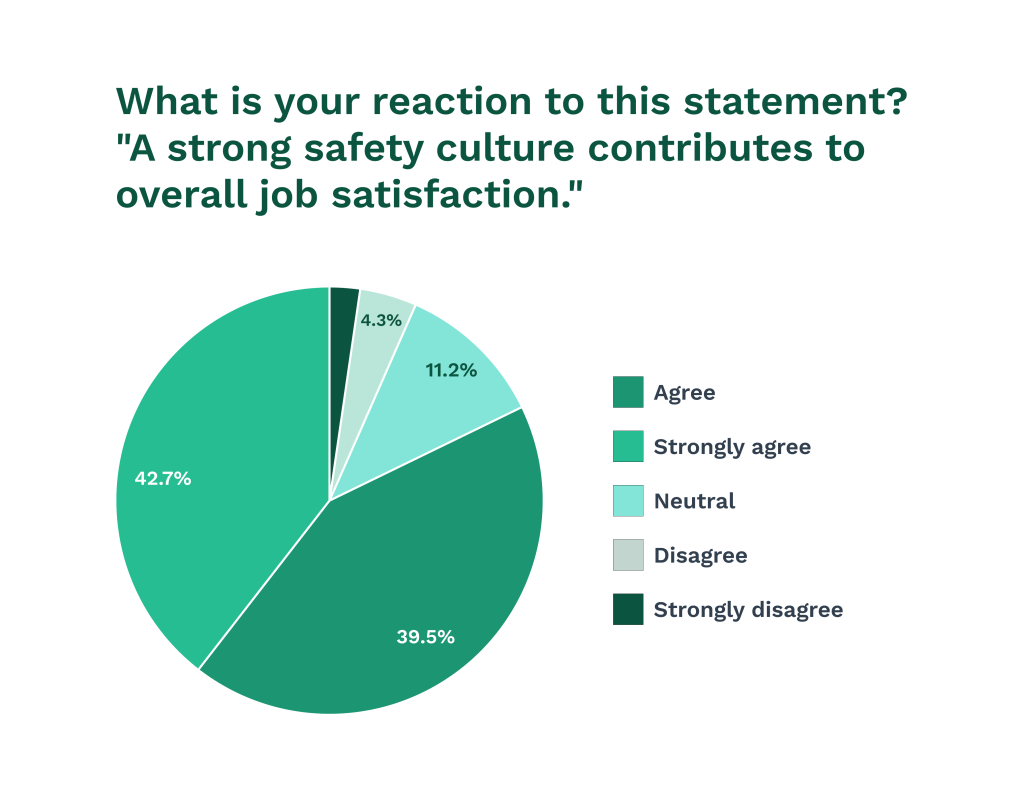
Barely than viewing safety as a sequence of checkboxes to tick off, we’ll have a look at how each ingredient contributes to creating an entire safety ecosystem.
Machine Repairs Safety Template
Underneath is a machine repairs safety template that repairs organizations can use:
The Foundation of Machine Safety
Machine safety is figuring out that every piece of equipment harbors potential risks, irrespective of complexity.
These risks turn into considerably pronounced all through repairs procedures when defending guards are eradicated, packages are disassembled, and the maintenance crew ought to work collectively straight with machine components.
This direct interaction creates a singular set of challenges that require cautious consideration and systematic approaches to ensure safety.
Implications of Unsafe Repairs
Unsafe repairs practices have implications far previous fast bodily harm. When safety protocols are compromised, the implications ripple, affecting each little factor from worker morale to financial stability.
Take into consideration a state of affairs the place a repairs technician rushes by the use of a lock-out course of on a hydraulic press. The fast hazard of injury is obvious, nevertheless the broader implications embody the potential long-term psychological impression on coworkers, decreased perception in administration, elevated insurance coverage protection costs, and attainable regulatory scrutiny.
Definition of Repairs Safety
Repairs safety refers again to the practices and procedures to ensure the safety of repairs workers, instruments, and the encircling setting all through repairs actions.
It contains determining and mitigating potential hazards, providing acceptable non-public defending instruments (PPE), and following established safety protocols to forestall accidents and accidents.
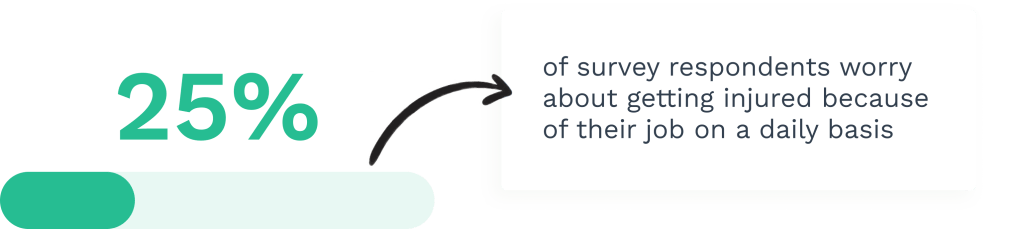
Repairs safety is an entire methodology encompassing each little factor from the preliminary hazard analysis to verifying a safe working setting.
By prioritizing repairs safety, organizations can protect their workforce, hold operational effectivity, and reduce the prospect of dear incidents.
The True Worth of Unsafe Repairs
Sooner than delving into specific procedures, it’s important to know what’s at stake. Unsafe repairs practices can lead to:
- Excessive accidents or fatalities amongst repairs personnel
- Costly instruments hurt requiring in depth repairs
- Manufacturing downtime affecting enterprise operations
- Approved liabilities and regulatory violations
- Decreased worker morale and elevated turnover
- Environmental incidents and associated cleanup costs
- Lowered effectivity and morale amongst repairs crews because of safety points
Understanding these potential penalties helps reinforce the importance of following appropriate safety protocols all through every repairs exercise.
Pre-Repairs Safety: A Essential Foundation for Preventive Repairs
Thorough preparation is the cornerstone of safe repairs. Sooner than any instrument touches a machine, repairs crews, and personnel ought to engage in an entire hazard analysis course of.
This analysis isn’t merely about determining obvious hazards; it requires a deep understanding of how completely completely different packages work collectively and the way in which assorted failure modes might manifest.

Take into consideration a seemingly straightforward exercise like altering a bearing in an industrial mixer. The hazard analysis ought to account for not merely the mechanical components of the responsibility however as well as potential saved energy throughout the system, chemical residues, ergonomic challenges of accessing the bearing, and even environmental components like temperature and humidity which can affect the maintenance course of.
Menace analysis turns into important when dealing with sophisticated packages with quite a few energy sources. A up to date manufacturing line, for instance, might incorporate electrical, hydraulic, pneumatic, and mechanical packages, each requiring specific consideration all through repairs procedures.
Making a Repairs Safety Plan
Making a repairs safety plan is crucial to ensure the safety of repairs workers and the overall success of repairs operations. The plan must embody:
- Hazard Identification and Menace Analysis: Decide all potential hazards associated to repairs actions. Then, an intensive hazard analysis will most likely be carried out to guage the severity and likelihood of each hazard and resolve acceptable administration measures.
- Enchancment of Safety Protocols and Procedures: Arrange clear safety protocols and procedures tailored to the actual risks involved in repairs operations. These protocols must cowl each little factor from non-public defending instruments to emergency response actions.
- Teaching and Coaching for Repairs Workers: Current full teaching and education to repairs workers on safety protocols, appropriate use of repairs devices, and the risks involved of their duties. Widespread teaching intervals help reinforce safety practices and inform workers about new safety measures.
- Widespread Safety Inspections and Audits: Conduct frequent safety inspections and audits to ensure compliance with safety protocols and set up potential safety hazards. These inspections help hold a safe working setting and promote workplace safety.
- Overview and Revision of the Plan as Wished: Always analysis and revise the maintenance safety plan based totally on recommendations, incident research, and changes in legal guidelines or instruments. Defending the plan up-to-date ensures it stays environment friendly in addressing current safety challenges.
By implementing an entire repairs safety plan, organizations can mitigate risks, protect repairs workers, and ensure the straightforward operation of repairs actions.
Vital Pre-Repairs Safety Procedures
Menace Analysis
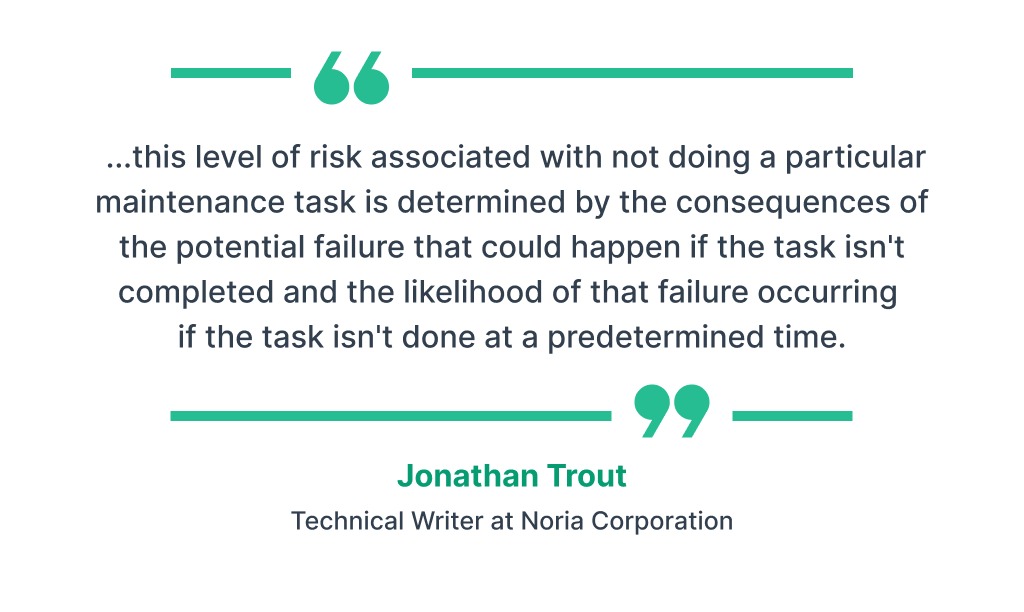
Sooner than any repairs work begins, repairs crews ought to conduct an intensive hazard analysis. This contains:
- Determining all potential hazards associated to the maintenance exercise
- Evaluating the severity and likelihood of each hazard
- Determining acceptable administration measures
- Documenting findings and sharing them with all involved personnel
The hazard analysis ought to consider mechanical, electrical, chemical, and ergonomic hazards and any environmental components affecting worker safety.
The Paintings and Science of Lock-Out/Tag-Out
Lock-Out/Tag-Out (LOTO) procedures symbolize one of many essential essential components of repairs safety, however they’re often misunderstood or oversimplified. Repairs crews must be completely expert in LOTO procedures to ensure all energy sources are accurately isolated sooner than beginning any repairs work.
LOTO isn’t almost turning off power and locking a change; it’s an entire course of that requires a deep understanding of equipment operation and potential energy sources.
Understanding energy isolation begins with recognizing that energy can exist in plenty of sorts. In an industrial setting, these might embody electrical current flowing by the use of conductors, pressurized fluid in hydraulic strains, compressed air in pneumatic packages, saved mechanical energy in springs or elevated components, and thermal energy in heated surfaces.
Each form of energy requires specific isolation procedures and verification methods.
Possibly basically crucial step throughout the LOTO course of is verifying the zero-energy state. This verification must be energetic considerably than passive—merely observing {{that a}} change is off or a valve is closed isn’t sufficient.
Repairs personnel ought to attempt to operate the instruments and check out for the presence of energy using acceptable gadgets and techniques.
LOTO is perhaps basically crucial safety course of in machine repairs. It contains:
- Determining all energy sources (electrical, mechanical, hydraulic, pneumatic, chemical, thermal)
- Notifying all affected workers regarding the repairs train
- Accurately shutting down the instruments
- Disconnecting or blocking all energy sources
- Making use of locks and tags to energy isolation items
- Verifying zero energy state by the use of testing
- Sustaining the lock-out scenario until work is full
Non-public Defending Instruments: The Remaining Line of Safety
Whereas Non-public Defending Instruments (PPE) often receives essential consideration in safety discussions, it’s essential to know its place throughout the hierarchy of safety controls. Repairs crews must be equipped with the acceptable PPE to protect themselves from potential hazards all through repairs duties. PPE have to be seen as a result of the ultimate line of safety, not the primary strategy of security.
This angle doesn’t diminish its significance nevertheless emphasizes the need for proper alternative, repairs, and use of PPE together with completely different safety measures.
The variety of acceptable PPE requires cautious consideration of the actual hazards present all through repairs duties.
For example, when engaged on electrical packages, it’s not enough to placed on insulated gloves; the gloves’ voltage rating ought to match or exceed the potential voltage present throughout the system.
Equally, eye security must be chosen based totally on specific hazards—impression security, chemical splash security, or security from optical radiation throughout the case of welding operations.
Selection and Use of Acceptable PPE
Fully completely different repairs duties require numerous sorts of PPE. Repairs crews ought to fastidiously select and use the acceptable PPE based totally on the hazards they may encounter all through their duties. Vital devices typically embody:
- Safety glasses or face shields for eye security
- Arduous hats for head security in areas with overhead hazards
- Metallic-toed boots to protect in the direction of falling objects
- Scale back-resistant gloves acceptable for the responsibility
- Listening to security in high-noise areas
- Respiratory security when working with hazardous provides
- Arc flash defending garments when working with electrical packages
Instruments Repairs Best Practices
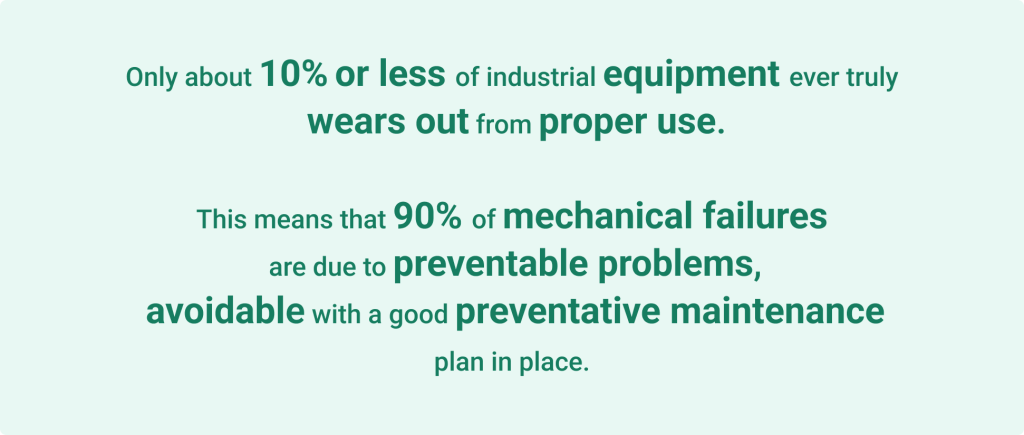
Instruments repairs is essential to ensure instruments reliability, effectivity, and safety. Listed below are some best practices for instruments repairs:
Performing Widespread Preventive Repairs
Widespread preventive repairs is essential to forestall instruments failures and cut back downtime. This consists of:
- Scheduling Widespread Repairs Duties: Develop a schedule that outlines frequent repairs duties for every little bit of equipment. Adhering to this schedule helps ensure that repairs actions are carried out persistently and on time.
- Performing Routine Inspections and Checks: Conduct routine inspections and checks to determine any indicators of injury, hurt, or potential hazards. Early detection of factors permits for nicely timed repairs and prevents further essential points.
- Altering Worn-Out Elements and Parts: Repeatedly trade worn-out components and components to maintain up instruments effectivity and safety. Using high-quality different components ensures the longevity and reliability of the instruments.
- Lubricating and Cleaning Instruments: Appropriate lubrication and cleaning are essential for the smooth operation of equipment. Repeatedly lubricate shifting components and clear instruments to forestall the buildup of mud and particles which will set off malfunctions.
- Updating Repairs Information and Logs: Protect detailed information and logs of all repairs actions, along with inspections, repairs, and half replacements. Appropriate documentation helps monitor the maintenance historic previous and set up patterns which is able to level out recurring factors.
Preventive repairs might also assist set up potential hazards and forestall accidents, lowering the prospect of accidents and instruments hurt. By following these best practices, organizations can assure their instruments stays in optimum scenario, promoting workplace safety and operational effectivity.
The Human Contemplate Repairs Safety
The place of human components in repairs safety cannot be overstated.
Repairs crews ought to take note of human components equal to fatigue and time stress which will impression their safety and effectivity.
Even basically probably the most full procedures and highest-quality defending instruments may be rendered ineffective by human error, fatigue, or complacency.
Understanding these human components requires exploring the psychological components of repairs work.
Take into consideration the impression of time stress on repairs operations. When manufacturing requires are extreme, and instruments downtime means misplaced earnings, repairs personnel may actually really feel stress to cut corners or rush by the use of procedures.
This stress can manifest subtly, equal to skipping steps in a lock-out course of or forgoing a closing safety confirm sooner than restarting.
Fatigue presents one different essential human difficulty downside. Repairs work often contains sophisticated problem-solving, bodily exertion, and the need to maintain extreme consideration to aspect.
When fatigue items in, the prospect of errors will enhance dramatically.
This relationship between fatigue and error hazard necessitates cautious consideration of labor scheduling and rest durations.
Documentation and Communication: Developing a Safety Custom
Adequate documentation and communication sort the backbone of any worthwhile repairs safety program.
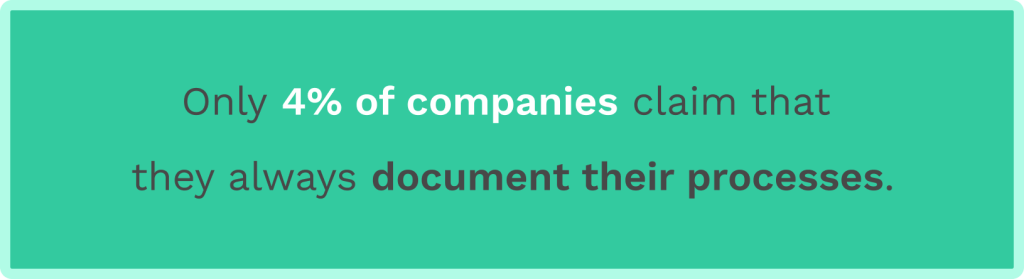
Repairs crews ought to ensure that all safety procedures are appropriately documented and communicated to all associated personnel.
Nonetheless, these elements delay previous merely sustaining written procedures or posting warning indicators.
They include making an entire system that ensures essential safety data is on the market, understood, and acted upon the least bit organizational ranges.
Documentation in repairs safety serves quite a few capabilities. It presents a reference for regular procedures, information repairs actions and safety incidents, and serves as a training instrument for model spanking new personnel.
Nonetheless, the mere existence of documentation isn’t sufficient; dwelling documentation ought to evolve based totally on experience and courses realized.
Communication in repairs safety ought to stream in quite a few directions – up and down the organizational hierarchy and horizontally between departments and shifts.
This communication must be formal (by the use of established reporting packages and customary conferences) and informal (by the use of every day interactions and fast recommendations channels).
Emergency Preparedness and Response
Emergency preparedness in repairs operations requires further than merely having a major assist gear and determining the location of emergency exits.
Repairs crews must be expert in emergency response protocols and participate in frequent drills to ensure they’re prepared for emergencies.
It calls for a whole understanding of potential emergency eventualities and the occasion of specific response protocols for each.
Take into consideration a state of affairs the place a repairs technician turns into trapped in a confined home all through instruments restore.
Responding to this emergency requires fast movement from quite a few occasions – rescue personnel with acceptable teaching and instruments, medical responders, and personnel who can safely shut down any affected packages.
This state of affairs illustrates why emergency preparedness ought to embody frequent drills and updates to emergency procedures based totally on courses realized.
Regulatory Compliance and Previous
Whereas regulatory compliance is integral to repairs safety, actually environment friendly safety functions transcend mere compliance.
Repairs crews ought to adhere to all regulatory requirements to ensure their very personal and their coworkers’ safety. Guidelines have to be seen as minimal requirements considerably than ultimate targets.
This angle encourages the occasion of safety practices that sort out specific organizational needs and challenges whereas meeting or exceeding regulatory requirements.
Understanding and implementing regulatory requirements requires staying current with legal guidelines and changes in enterprise necessities.
This ongoing course of contains frequent course of opinions, updating teaching functions, and sustaining appropriate documentation of compliance actions.
Conclusion
Machine repairs safety represents a complicated interplay of technical data, human components, and systematic approaches to hazard administration.
Repairs crews’ ongoing dedication to safety practices is essential for sustaining a safe working setting. Sustaining a safe repairs operation requires fastened vigilance, ongoing teaching, and a dedication to regular enchancment.
The way in which ahead for repairs safety lies in integrating new utilized sciences and methodologies whereas specializing in fundamental safety concepts.
As instruments turns into further sophisticated and automated, the challenges of sustaining it safely will evolve, requiring repairs professionals to switch their data and experience repeatedly.
Don’t forget that safety in repairs isn’t achieved by the use of any course of or piece of equipment. Nonetheless, by the use of the cautious integration of quite a few packages and approaches, all work collectively to protect basically probably the most useful asset in any group – its people.