Get a Free WorkTrek Demo
Let’s current you methods WorkTrek might allow you to optimize your maintenance operation.
Try with out spending a dime
https://www.goodfirms.co/software program program/worktrekMaintenance strategies protect gear working simply and successfully. Two frequent approaches are condition-based maintenance (CBM) and time-based maintenance (TBM).
These methods differ in deciding when to hold out maintenance duties and schedule maintenance.
State of affairs-based maintenance is determined by amassing information from gear to seek out out maintenance needs, whereas time-based maintenance follows a set schedule. CBM makes use of devices like sensors and analytics to predict when gear might fail.
TBM, alternatively, sticks to set intervals for maintenance work.
Every strategies intention to forestall breakdowns and lengthen gear life. The choice between CBM and TBM relies upon upon parts just like the type of gear, accessible sources, and enterprise targets.
Understanding these approaches might assist companies make wise choices about their maintenance plans.
Key Takeaways
- CBM makes use of real-time information to predict maintenance needs, whereas TBM follows a set schedule
- Deciding on between CBM and TBM relies upon upon gear type, sources, and agency targets.
- Every strategies intention to forestall breakdowns and improve gear lifespan
Understanding Maintenance
Maintenance strategies have superior to reinforce gear reliability and reduce costs. Key phrases help make clear utterly completely different approaches to conserving property working simply.
Evolution of Maintenance Strategies
Maintenance has come a good way from straightforward reactive repairs. Early strategies centered on fixing points solely after they broke down. This usually led to stunning downtime and extreme costs.
As industries grew further superior, preventive maintenance emerged.
Firms started doing widespread repairs based on time or utilization. This helped steer clear of some breakdowns nevertheless wasn’t on a regular basis setting pleasant.
State of affairs-based maintenance marked a significant shift.
It makes use of real-time information to predict when gear needs consideration. This technique saves money by solely doing maintenance when actually needed.
Instantly, many corporations use a combination of strategies. They combine time-based checks with data-driven choices.
This balanced methodology targets for max uptime on the bottom worth.
Key Maintenance Phrases Outlined
Reactive Maintenance: Fixing gear after it fails. It’s straightforward nevertheless may very well be costly and disruptive.
Preventive Maintenance: Widespread, scheduled repairs to forestall failures. It could embody:
- Cleaning
- Lubrication
- Half replacements
Predictive Maintenance: Using information to forecast when maintenance is required. It usually consists of:
- Sensors
- Analytics software program program
- Machine finding out algorithms
- Sensor information
- Historic information
State of affairs-Based totally Maintenance: A type of predictive maintenance that shows gear properly being in real-time.
Proactive Maintenance: Determining and fixing the idea causes of equipment points to forestall future factors.
Maintenance Thought Progress: Making a tailored combination of strategies for an organization’s specific needs.
State of affairs-Based totally Maintenance
State of affairs-based maintenance (CBM) makes use of real-time information to seek out out when gear needs service. It is determined by monitoring devices, wise sensors, and analytics to predict failures sooner than they happen.
Guidelines of CBM
CBM focuses on the exact state of affairs of equipment barely than fixed maintenance schedules.
It makes use of sensors and monitoring devices to hint key parameters like vibration, temperature, and oil top quality. These devices collect information continually to determine early indicators of wear and tear and tear or failure.
Like modern automobiles that use sensors to inform drivers of maintenance actions or routine maintenance events, CBM makes use of sensors in gear to provide this information.
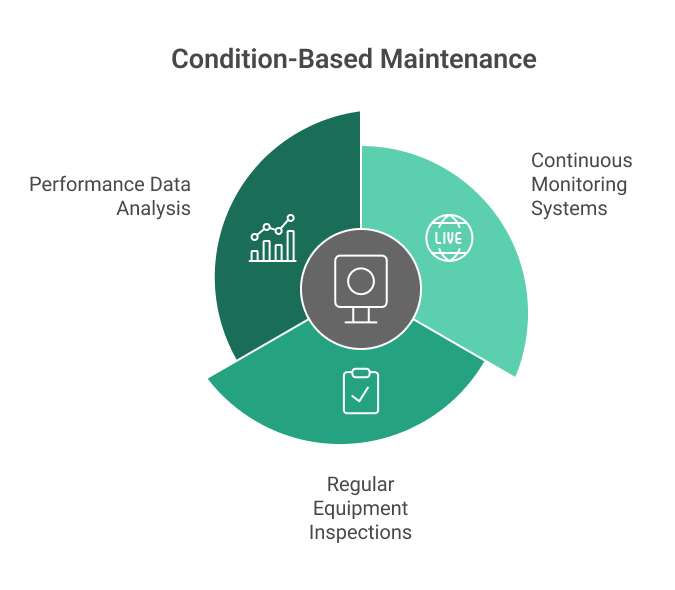
Analytics performs a large place in CBM. Superior software program program analyzes the information to find out traits and predict when maintenance is required.
This helps teams plan repairs shortly, avoiding pointless work and stunning breakdowns.
CBM moreover considers asset criticality. Important gear will get further consideration and sources to stay in excessive type.
Advantages of CBM
CBM can drastically improve gear availability. Fixing factors early reduces the hazard of sudden failures that will shut down operations.
It usually lowers maintenance costs over time. Teams solely do work when actually needed, saving on labor and parts.
A condition-based maintenance program helps lengthen the lifetime of the gear.
Catching points early prevents small factors from inflicting predominant hurt. You don’t want to wait until machines break sooner than taking movement.
It offers maintenance teams greater insights. They’ll see how gear performs over time and make smarter choices about repairs and replacements.
Empowering the maintenance workers with vital skills and data is crucial for determining potential factors and contributing to the overall success of the TBM program.
Challenges and Points
Organising CBM requires an upfront funding. Firms need to buy sensors, monitoring devices, and software program program.
Teaching is is one different crucial subject. Employees ought to examine to make use of recent devices and interpret information appropriately.
Information top quality is important. Faulty sensors or incorrect analysis can lead to harmful choices.
Not all gear benefits equally from CBM.
Simple machines or these with unpredictable failure patterns might be not good candidates.
CBM packages can generate plenty of information. Teams need a plan and have the abilities to deal with and use this information efficiently.
Types of State of affairs-Based totally Maintenance Monitoring Methods
Vibration Analysis
Vibration analysis is a strong condition-based maintenance monitoring strategy that measures the vibration ranges of apparatus to detect placed on or breakdown. This system is very environment friendly for monitoring the properly being of rotating gear, paying homage to pumps, motors, and gearboxes.
By analyzing vibration patterns, maintenance teams can decide potential factors sooner than they escalate into vital points, decreasing downtime and maintenance costs.
This proactive technique ensures that maintenance actions are carried out solely when obligatory, optimizing helpful useful resource allocation and lengthening the lifespan of vital gear.
Thermal Imaging
Thermal imaging is a non-invasive condition-based maintenance monitoring strategy that makes use of infrared cameras to detect temperature modifications in gear.
This system is broadly used to look at electrical packages, mechanical gear, and buildings. Maintenance teams can decide potential factors paying homage to overheating, electrical faults, and insulation points by capturing and analyzing thermal pictures.
This early detection helps reduce the hazard of equipment failure and enhances normal system reliability.
Thermal imaging is vital in a condition-based maintenance approach. It gives invaluable insights with out requiring direct contact with the gear.
Oil Analysis
Oil analysis is a condition-based maintenance monitoring strategy that features analyzing the state of affairs of lubricating oils to detect placed on or contamination.
This method is commonly utilized to look at the properly being of engines, gearboxes, and hydraulic packages.
Maintenance teams can decide potential factors paying homage to placed on, corrosion, and contamination by analyzing oil samples.
This proactive technique helps reduce the hazard of equipment failure and improve normal system reliability.
Oil analysis is vital to condition-based maintenance, guaranteeing gear operates successfully and efficiently.
Time-Based totally Maintenance
Time-based maintenance (TBM) is one different frequent approach for conserving gear working simply. It is determined by set schedules for maintenance duties and targets to forestall breakdowns sooner than they happen.
Fundamentals of TBM
TBM follows a set maintenance work schedule.
Duties are achieved at set events, regardless of the gear’s state of affairs. For example, an oil change may very well be carried out every three months.
TBM is a type of preventive maintenance. It assumes parts will placed on out at predictable events. The target is to trade or make issues higher sooner than they fail.
Key choices of TBM:
- Widespread inspections
- Scheduled half replacements
- Deliberate downtime for maintenance
- Mounted time intervals for repairs
- Predictable schedule
TBM works correctly for gear with recognized failure fees. It’s usually utilized in factories and for car repairs.
Benefits and Limitations
TBM affords an a variety of benefits:
- Simple to plan and funds
- It helps cease stunning breakdowns
- Can lengthen gear life
- Follows producer strategies
Nonetheless it moreover has drawbacks:
- Might end in pointless work
- Doesn’t account for exact gear state of affairs
- Can miss points that occur between scheduled maintenance
TBM may very well be a lot much less setting pleasant than completely different methods.
It’d trade parts which is perhaps nonetheless good. This can improve costs over time.
For some gear, TBM is the one possibility. It actually works correctly for simple machines with clear placed on patterns, nevertheless completely different methods might work greater for superior packages.
Predictive Maintenance
Definition and Rationalization
Predictive maintenance is a proactive maintenance approach that leverages superior information analysis methods and predictive fashions to estimate when maintenance have to be carried out.
This technique consists of analyzing historic maintenance information, gear effectivity information, and completely different associated information to predict when gear will fail or require maintenance.
By adopting predictive maintenance, organizations can significantly reduce maintenance costs, enhance gear reliability, and improve normal productiveness.
Machine Learning Algorithms
Predictive maintenance employs superior utilized sciences paying homage to machine finding out, artificial intelligence, and IoT sensors to assemble and analyze information from gear and packages.
This data then creates predictive fashions to forecast gear failure or effectivity degradation. These fashions allow maintenance teams to schedule maintenance actions upfront, decreasing downtime and enhancing normal system reliability.
Predictive maintenance is very helpful for vital or superior gear, the place downtime can have vital penalties.
Lower Hazard
By implementing predictive maintenance, organizations can scale back the hazard of equipment failure, improve gear effectivity, and improve normal productiveness.
Furthermore, predictive maintenance helps organizations steer clear of pointless maintenance, lower associated costs, and enhance the overall effectivity of their maintenance operations.
Predictive maintenance is a key component of a proactive maintenance approach and could be utilized along with completely different maintenance approaches, paying homage to preventive maintenance and condition-based maintenance.
By integrating predictive maintenance into their approach, organizations can optimize maintenance operations, reduce costs, and acquire higher productiveness.
Monetary Implications
Maintenance strategies have giant outcomes on costs and earnings.
Deciding on between condition- and time-based approaches affect budgets, gear life, and normal financial properly being.
Worth Analysis
Time-based maintenance usually ends in higher short-term costs. It requires widespread half replacements and labor, even when the gear works top quality. This can waste money on unneeded repairs.
State of affairs-based maintenance makes use of sensors and information to determine points early. It cuts costs by fixing factors sooner than they worsen. CBM moreover reduces downtime, which saves money.
CBM tends to be cheaper over time because of it helps protect gear working longer and reduces after-hours calls and additional time pay.
It extends gear life and prevents predominant breakdowns, decreasing different and restore costs in the long run.
Worth-Revenue Points
Firms ought to weigh the costs and benefits of each technique. Time-based maintenance is less complicated to plan and funds for and works correctly for a lot much less vital or lower-value property.
CBM requires further upfront funding in sensors and software program program nevertheless usually pays off for high-value or vital gear. It helps steer clear of costly failures and unplanned downtime.
Asset criticality performs a large place on this different. Important gear failures might trigger giant losses, so the extra worth of CBM is often worth it for these property.
Maintenance optimization is important. The proper approach usually mixes every approaches based on gear type, value, and significance.
Worth of Gear Downtime
Commerce-Specific Costs
Technological Developments
Know-how has transformed maintenance practices.
New devices allow greater gear monitoring and information analysis, enhancing companies’ asset maintenance.
Integration of State of affairs Monitoring
State of affairs monitoring devices have flip into further refined. Vibration analysis and thermography help detect factors early, and IoT sensors now continually observe gear standing.
These devices collect large portions of information, which superior analytics processes. This helps predict failures sooner than they happen.
Maintenance teams can now make choices based on real-time information. They not rely solely on fixed schedules. This technique usually prevents pointless downtime.
OEM and Commerce Innovation
Genuine gear producers (OEMs) play a key place in maintenance innovation. They develop new sensors and monitoring packages for his or her merchandise.
Digital BOP Assurance is an occasion of offshore drilling. It improves maintenance for blowout preventers.
Commerce collaborations moreover drive progress. Firms share information and biggest practices, dashing up the occasion of newest maintenance concepts.
Prognostics is an rising self-discipline that mixes state of affairs monitoring with predictive analytics to help estimate gear’s remaining useful life.
Laptop Maintenance Administration System to the rescue
Computerized Maintenance Administration Methods (CMMS) like WorkTrek play a pivotal place in efficiently managing every condition-based maintenance (CBM) and time-based maintenance (TBM) strategies.
For CBM, CMMS integrates seamlessly with state of affairs monitoring devices and sensors to assemble real-time information on gear effectivity.
This data is then analyzed to predict potential failures, enabling maintenance teams to hold out maintenance duties solely when obligatory.
Nonetheless, CMMS is equally invaluable for TBM because of it automates the scheduling of routine maintenance duties at predetermined intervals.
It ensures that maintenance actions are carried out persistently and by producer strategies, stopping stunning breakdowns and sustaining gear reliability.
CMMS gives maintenance managers with a centralized platform to hint historic maintenance information, deal with maintenance schedules, and monitor gear conditions, thus facilitating educated decision-making.
Moreover, CMMS enhances communication inside maintenance teams and all through departments by providing real-time updates on maintenance work and equipment standing.
This integration of CBM and TBM inside a CMMS framework ends in a further setting pleasant and environment friendly maintenance approach, lastly enhancing operational effectivity and decreasing downtime.
Strategic Maintenance Willpower-Making
Selecting the best maintenance technique impacts gear reliability and operational effectivity.
Firms ought to weigh the benefits and drawbacks of varied strategies to optimize their maintenance packages.
Balancing CBM and TBM
So how do you stability condition-based maintenance (CBM) with time-based maintenance (TBM)?
CBM makes use of real-time information to predict when maintenance is required. Within the meantime, TBM follows a set schedule regardless of gear state of affairs.
CBM may very well be further setting pleasant as a result of it prevents pointless maintenance.
It usually ends in higher gear availability and reduce costs.
Nonetheless, TBM is less complicated to implement and works correctly for gear with predictable placed on patterns.
Many companies use a combination of every approaches. Important gear might use CBM, whereas a lot much less crucial property adjust to TBM schedules.
This balanced technique helps optimize helpful useful resource allocation and scale back downtime.
Adapting to Organizational Desires
Environment friendly maintenance packages adapt to an organization’s specific needs.
Components to consider embody:
- Funds constraints
- Accessible know-how
- Employees expertise
- Gear criticality
- Regulatory requirements
Small companies with restricted sources might need TBM because of its simplicity. Within the meantime, large industrial facilities usually put cash into CBM packages for his or her vital property.
Widespread consider of maintenance strategies is vital.
As know-how advances and enterprise needs change, companies ought to manage their technique. This might suggest step-by-step shifting from TBM to CBM or discovering new strategies to combine every methods.
Means ahead for Maintenance
New utilized sciences and approaches to maintenance are shortly evolving. These advances intention to make gear repairs further setting pleasant, cost-effective, and sustainable.
Predictive Traits and Prognostics
Predictive maintenance is transforming how companies look after his or her property. It makes use of information from sensors and analytics to forecast when gear might fail, allowing fixes sooner than breakdowns happen.
Machine finding out helps spot patterns in gear information. These patterns can current early indicators of points, allowing technicians to plan repairs on the good time.
Prognostics take this extra. They estimate how quite a bit life is left in a component.
This helps companies get most likely probably the most use out of elements with out risking failure.
Analytics performs a key place in these advances.
It turns raw information into useful insights, which data maintenance choices and schedules and improve gear reliability.
Sustainable and Wise Maintenance
Wise maintenance packages have gotten further frequent. They use associated devices to look at the properly being of real-time gear, serving to catch factors shortly and reduce waste.
These packages usually use a lot much less vitality and sources. They intention maintenance the place it’s most needed.
This cuts down on pointless work and parts different.
State of affairs-based maintenance is a key part of this growth. It bases work on the exact state of equipment, not fixed schedules. This technique can decrease your bills and lengthen machine life.
New devices help optimize maintenance plans. They stability costs, risks, and effectivity.
This ends in greater choices about when and the way one can protect gear.
Summary
This textual content explores two key maintenance strategies: condition-based maintenance (CBM) and time-based maintenance (TBM). CBM makes use of real-time information to seek out out when maintenance is required, whereas TBM follows a set schedule.
Every intention to forestall gear failures and lengthen lifespan. CBM usually reduces costs by addressing factors sooner than they worsen. TBM is less complicated nevertheless might end in pointless maintenance.
The article discusses the monetary implications, technological developments, and strategic decision-making in maintenance. It highlights the importance of balancing every approaches for optimum gear reliability and operational effectivity.