Get a Free WorkTrek Demo
Let’s current you the way in which WorkTrek may allow you to optimize your repairs operation.
Try with out value
Hazard-based repairs prioritizes repairs duties based on the possibility associated to gear failure. It is a approach centered on optimizing helpful useful resource allocation to strengthen asset reliability and lengthen its useful life.
Hazard-based repairs goes previous standard repairs approaches. It makes use of knowledge and analysis to make educated picks about when and straightforward strategies to protect belongings.
Hazard-based repairs (RBM) objectives to optimize helpful useful resource allocation and reduce the possibility of expensive breakdowns by determining essential belongings and potential failure modes.
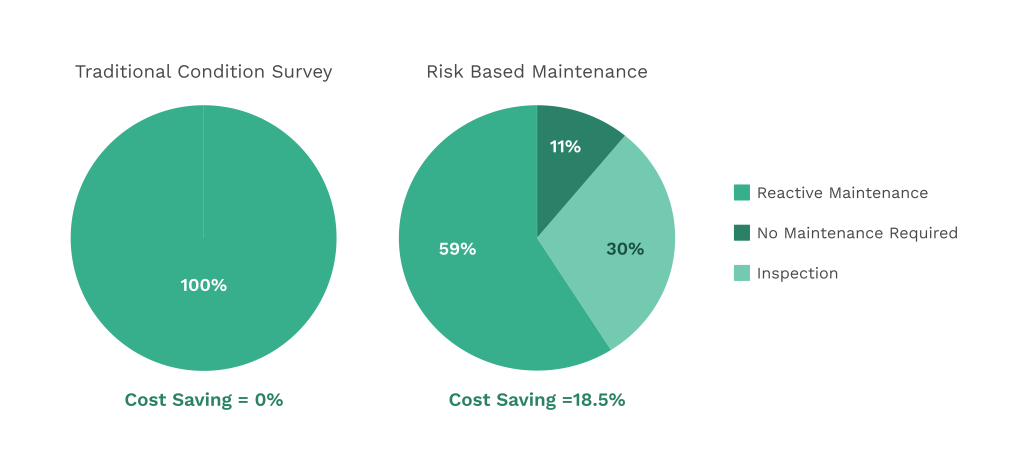
Provide: WLC
This technique helps organizations stability the need for gear reliability with the costs of repairs actions.
By systematically assessing risk, companies can allocate their sources further efficiently, specializing in in all probability essentially the most essential belongings that pose the perfect risk to operations, safety, or financial effectivity.
RBM features a regular cycle of risk analysis, planning, and execution.
It requires gathering info on gear effectivity, analyzing failure patterns, and evaluating the implications of potential failures.
This knowledge is then used to create tailored repairs plans that deal with the exact risks associated to each asset.
Key Takeaways
- RBM prioritizes repairs duties based on gear failure risks
- It optimizes helpful useful resource allocation and improves normal asset reliability
- RBM requires ongoing risk analysis and data-driven decision-making
Fundamentals of Hazard-Primarily based Repairs
Hazard-based repairs focuses on assessing and managing asset risks using repairs info. Hazard-based asset repairs is a strategic technique that prioritizes sources in course of in all probability essentially the most essential belongings based on their potential risk and penalties of failure.
It objectives to optimize repairs actions and helpful useful resource allocation based on the potential have an effect on of failure.
Definition of Hazard-Primarily based Repairs
Hazard-based repairs (RBM) is a method that makes use of risk analysis to info repairs picks. It considers how in all probability gear will fail and what would happen if it did.
Primarily based totally on asset effectively being, RBM helps companies resolve which belongings need consideration most. It considers risk probability elements like safety, environmental have an effect on, and financial loss.
This technique differs from mounted schedules. As a substitute, it adapts repairs plans based on altering risks.
Evolution of Repairs Strategies
Repairs strategies have modified over time. Early methods have been reactive, fixing points solely after they broke.
Subsequent received right here preventive repairs, which used set schedules. This was increased nonetheless typically led to pointless work.
Hazard-based Repairs emerged as a further setting pleasant and hybrid technique.
It combines info analysis with skilled info to give attention to high-risk areas.
RBM helps companies:
- Decrease your bills
- Improve safety
- Improve gear reliability
It’s part of a shift in course of smarter, further versatile repairs practices.
Benefits of Hazard-Primarily based Repairs
Implementing a risk-based repairs approach gives fairly a number of benefits to organizations. By prioritizing repairs efforts on high-risk belongings, firms can lower the possibility of unusual gear failures, reduce downtime, and optimize repairs sources. A number of of the important thing benefits of risk-based repairs embody:
- Improved Asset Reliability and Longevity: By focusing repairs efforts on essential belongings, organizations can assure they’re well-maintained, lowering the possibility of asset failure and lengthening their operational life.
- Decreased Repairs Costs: Specializing in high-risk belongings permits for further setting pleasant use of repairs sources, lowering pointless repairs duties and normal costs.
- Enhanced Safety and Decreased Hazard of Accidents: Accurately maintained gear is way much less susceptible to fail unexpectedly, which helps protect a safer working environment and reduce the possibility of accidents.
- Elevated Effectivity and Productiveness: Minimizing stunning gear failures and downtime ends in smoother operations and higher productiveness.
- Larger Allocation of Repairs Sources: By determining and specializing in high-risk belongings, organizations can allocate their repairs sources further efficiently, guaranteeing that in all probability essentially the most essential belongings get hold of the attention they need.
- Improved Compliance with Regulatory Requirements: Widespread and centered repairs helps meet commerce legal guidelines and necessities and steer clear of potential fines and approved factors.
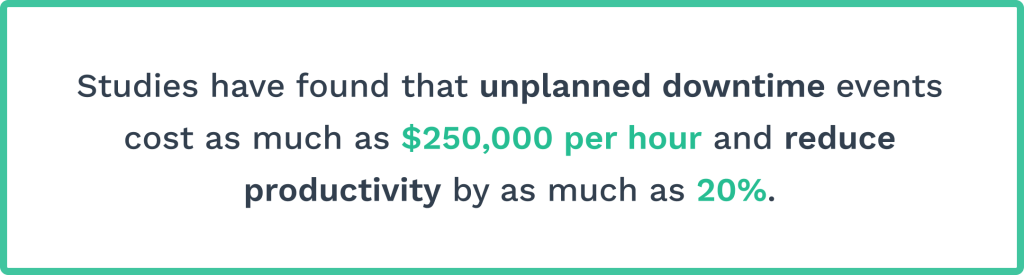
By focusing repairs efforts on essential belongings, organizations can guarantee that their most helpful belongings are adequately maintained, lowering the possibility of asset failure and minimizing the have an effect on of unusual downtime.
Implementing Hazard-Primarily based Repairs
Implementing risk-based repairs requires a structured technique. It consists of assessing belongings, setting requirements, and making a prioritization system. These steps help focus repairs efforts the place they’re most wished.
Analysis of Belongings and Their Failures
The 1st step is to look at all gear, which suggests checking each machine or half. Teams have to grasp how usually points break and why, and they also moreover wish to decide what happens when asset failures occur.
Hazard-based repairs strategies use precise info from earlier breakdowns. This helps predict future points. Teams must:
• Itemizing all belongings
• File failure historic previous
• Discover restore costs
• Monitor downtime
This knowledge helps spot patterns. It reveals which belongings need further consideration.
Hazard Evaluation Requirements
Subsequent, teams prepare tips to measure risk.
These tips help resolve how very important each asset is. They take a look at two elementary points:
- How in all probability is it to interrupt?
- What happens if it does break?
As quickly as risks are acknowledged, making a risk mitigation plan is important for stopping asset failures and guaranteeing repairs operations’ safety, effectivity, and cost-effectiveness.
Teams may use a scale like this:
Each asset will get a score for every probability and have an effect on. This helps rank them by risk diploma.
Prioritization Matrix
The ultimate step is making a matrix to rank belongings. This software program helps resolve the place to focus repairs work. It makes use of the scores from the possibility evaluation.
A straightforward matrix may appear as if this:
Have an effect on → Likelihood ↓ |
Minor | Common | Major |
---|---|---|---|
Low | 3 | 6 | 9 |
Medium | 2 | 5 | 8 |
Extreme | 1 | 4 | 7 |
Belongings with lower numbers get further consideration. This helps with planning and using sources correctly. Teams can think about high-risk devices first.
The matrix guides repairs schedules and helps resolve what checks to hold out. Extreme-risk belongings may need further frequent or detailed inspections.
Making a Hazard-Primarily based Repairs Plan
Making a risk-based repairs plan consists of a lot of steps, each designed to optimize repairs efforts and ensure the reliability of essential belongings. Proper right here’s a structured technique to creating an environment friendly repairs plan:
- Collect Information on Instruments and Belongings: Accumulate full info on all gear, along with failure histories, repairs costs, and completely different associated knowledge. This info varieties the inspiration of the possibility analysis course of.
- Conduct a Hazard Analysis: Take into account the potential risks associated to each asset. This consists of determining potential failure modes, their probability, and the implications of such failures.
- Develop a Repairs Method: Primarily based totally on the possibility analysis, create a repairs approach that addresses the acknowledged risks. This system must outline explicit repairs duties and their frequency.
- Assign Hazard Scores to Each Asset: Use the possibility analysis info to assign risk scores to each asset. These scores ought to duplicate every the probability of failure and the potential have an effect on of that failure.
- Prioritize Repairs Duties Primarily based totally on Hazard Ranges: Rank repairs duties consistent with their risk scores. The maintenance schedule must prioritize high-risk belongings.
- Schedule Repairs Duties and Allocate Sources: Develop an in depth repairs schedule that options all prioritized duties. Allocate repairs sources, harking back to personnel and devices, to ensure effectively timed and environment friendly execution of the plan.
- Evaluation and Substitute the Repairs Plan Often: Repeatedly monitor the effectiveness of the maintenance plan. Widespread evaluations and updates are essential to adapt to altering conditions and new info.
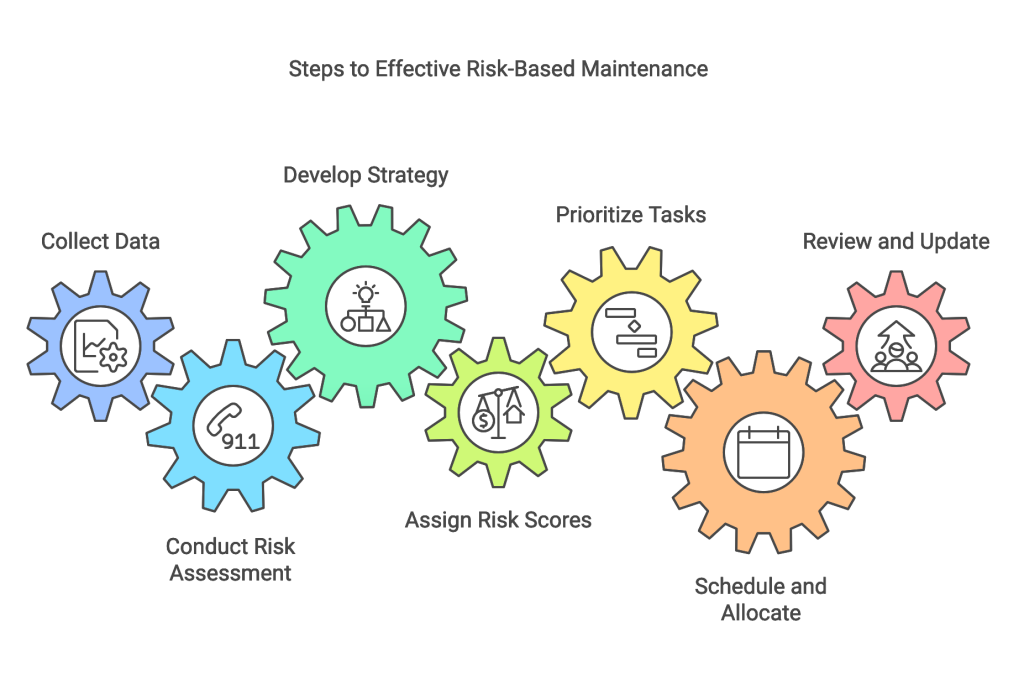
A well-structured risk-based repairs plan may assist organizations optimize repairs efforts, reduce downtime, and improve effectivity.
By systematically addressing risks, companies can assure their repairs approach is every proactive and environment friendly.
Hazard Administration in Repairs
Hazard administration is a key part of repairs planning. It helps teams think about in all probability essentially the most essential belongings and potential points. This technique can save time and money whereas preserving gear working simply.
Integration with Asset Administration
Hazard-based repairs works hand in hand with asset administration. Teams take a look at every little bit of equipment and bear in mind what may go mistaken. They ask questions like:
- How in all probability is a breakdown?
- What would happen if it failed?
- How quite a bit wouldn’t it not worth to restore?
This knowledge helps create a risk score for each asset. Extreme-risk devices get hold of further consideration, and maintenance efforts are optimized all through the facility to lower failure risks.
Widespread checks and data assortment are essential. They help spot factors sooner than they become large points. This proactive stance can forestall expensive breakdowns and protect operations working simply.
Balancing Costs and Risks
Discovering the becoming stability between repairs costs and risks is troublesome. An extreme quantity of repairs wastes money, whereas too little ends in breakdowns.
Hazard-based repairs helps uncover the sweet spot. It makes use of knowledge to make good picks concerning the place to spend time and money. Proper right here’s the way in which it really works:
- Decide essential belongings
- Assess risks for each
- Plan repairs based on risk ranges
- Monitor outcomes and regulate as wished
This system usually ends in worth monetary financial savings. It cuts down on pointless work whereas specializing in what points most. Over time, it may really enhance reliability and decrease normal repairs costs.
Nonetheless it’s not almost saving money. It’s about using sources correctly to take care of each half working safely and successfully.
Planning and Scheduling in RBM
Hazard-based repairs (RBM) will depend on a risk-based repairs technique involving cautious planning and good helpful useful resource use. It focuses on fixing gear based on how in all probability it is to interrupt and the way in which unhealthy that will likely be.
Repairs Planning
RBM planning begins with inspecting every little bit of equipment. Teams take a look at its age, use, and historic previous of points. As well as they bear in mind what would happen if it broke down.
Subsequent, they rank gear by risk.
The very best-risk devices get hold of in all probability essentially the most consideration, which helps steer clear of shock breakdowns.
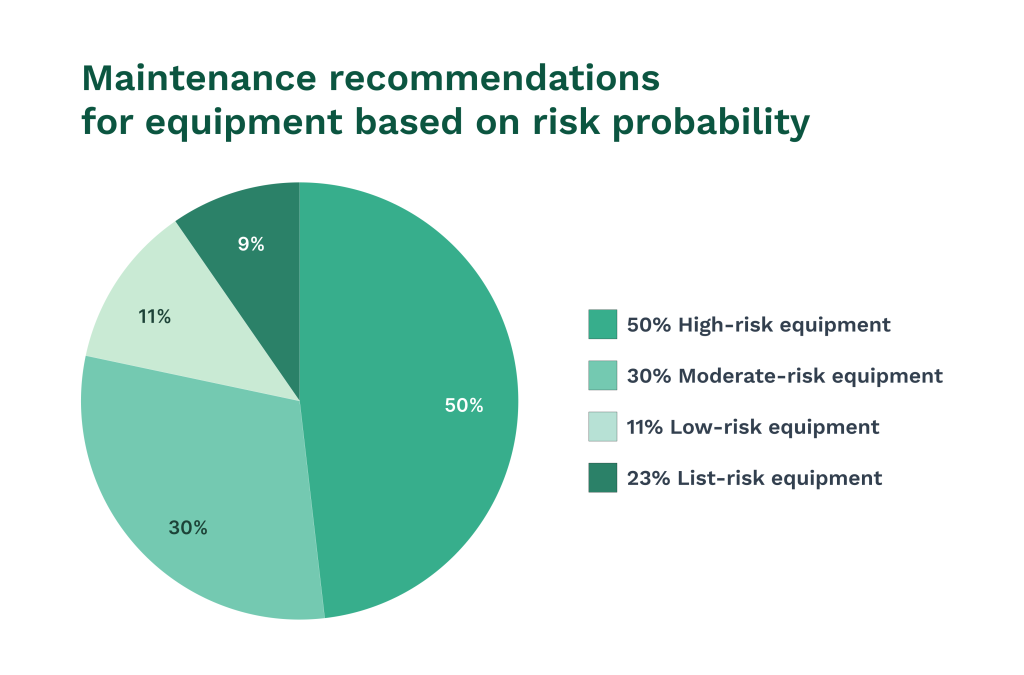
Teams then make a schedule. They resolve when to check, restore, or change each merchandise. The plan changes as new knowledge is accessible in.
Widespread evaluations protect the plan current, guaranteeing it matches the facility’s current risks and desires.
Helpful useful resource Allocation and Optimization
RBM helps use repairs sources correctly. It locations money and folk the place they’re wished most.
Extreme-risk gear receives further care, which implies further frequent checks or faster repairs. Low-risk devices get hold of a lot much less consideration, saving time and money.
Teams stability the worth of repairs in direction of the worth of failure. They objective to spend merely enough to forestall large points.
RBM moreover helps plan for parts and devices. It reveals what is maybe wished rapidly so teams could also be ready.
By specializing in risk, RBM maximizes every repairs dollar and labor hour, resulting in fewer breakdowns and fewer wasted effort.
This technique might be supreme when organizations with restricted sources reduce unplanned downtime.
Hazard-based repairs makes use of explicit devices and utilized sciences to judge risks and predict gear failures. These methods help repairs teams make data-driven picks and focus their efforts on essential belongings.
Hazard Analysis Devices
Hazard analysis devices help decide and measure potential risks to gear and strategies. One frequent software program is the Failure Mode and Outcomes Analysis (FMEA).
FMEA seems at how gear may fail and what impacts these failures might need.
One different helpful software program is the Hazard Matrix. This seen assist helps classify risks based on their probability and severity. It makes use of color codes to point which risks need fast consideration.
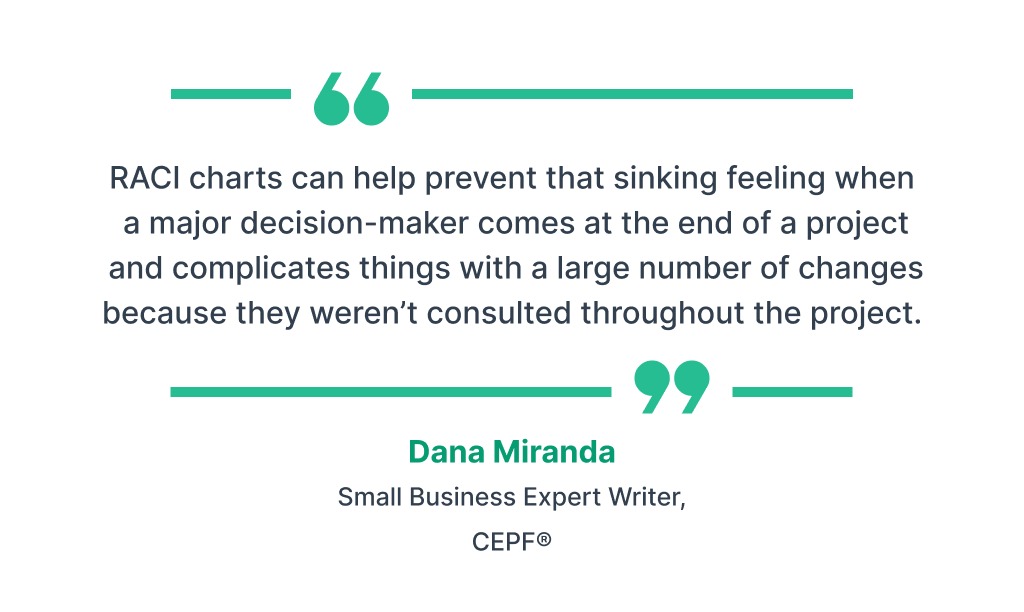
Fault Tree Analysis might be helpful. It maps out the chain of events that will lead to failure, serving to teams understand sophisticated strategies and uncover strategies to forestall points.
Predictive Repairs Utilized sciences
Predictive repairs makes use of superior tech to determine points sooner than they happen. Vibration analysis is a key methodology. It detects unusual vibrations in machines, which can signal upcoming failures.
Oil analysis is one different very important technique. It checks oil samples for indicators of wear and tear and tear or contamination. This will reveal factors inside engines or completely different shifting parts.
Infrared thermography makes use of heat-sensing cameras to go looking out scorching spots in gear. These scorching areas can stage to electrical points or excessive friction.
Ultrasonic testing helps detect leaks or cracks. It makes use of sound waves to go looking out factors which will’t be seen with the naked eye.
Key Effectivity Indicators
Key Effectivity Indicators (KPIs) help measure the success of risk-based repairs strategies. They provide info to judge repairs effectiveness and drive enhancements.
Measuring Repairs Effectiveness
Indicate Time to Restore (MTTR) is a crucial KPI for repairs teams. It measures the widespread time wished to restore gear after a failure. A lower MTTR signifies further setting pleasant restore processes.

Indicate Time Between Failure (MTBF) tracks the widespread time between gear breakdowns. Elevated MTBF values suggest increased reliability and maintenance practices.

Preventive repairs effectiveness measures how well-scheduled repairs prevents breakdowns. It compares deliberate repairs to unplanned repairs.
Work order effectivity tracks the completion worth and timeliness of repairs duties. This KPI helps decide bottlenecks inside the repairs course of.
Enchancment and Benchmarking
Asset repairs costs current notion into the financial have an effect on of repairs strategies. Monitoring these costs helps decide areas for potential monetary financial savings.
Reliability metrics, harking back to gear uptime and availability, current how properly repairs efforts protect belongings working. Elevated reliability usually interprets to improved productiveness.
Hazard analysis accuracy compares predicted failure probabilities to express outcomes. This KPI helps refine risk fashions over time.
Benchmarking KPIs in direction of commerce necessities or earlier effectivity highlights areas for enchancment. Widespread evaluation of these metrics drives regular enhancement of repairs practices.
Case Analysis
Hazard-based repairs has confirmed environment friendly all through quite a few industries. Companies have seen enhancements in safety, worth monetary financial savings, and equipment reliability.
Gulf Coast Chemical Plant
A chemical plant on the Gulf Coast carried out RBM for his or her mounted gear, piping, and stress discount models. The outcomes have been very important:
- 65% low cost in inspection requirements
- Projected $3.2 million low cost in repairs costs over 10 years
- Estimated $4.6 million in risk low cost monetary financial savings over 10 years
- Potential for $8 million in monetary financial savings over 10 years by rising turnaround intervals
BPD Refinery
A 130,000 BPD refinery within the USA carried out an RBI program using RBMI software program program:
- Decreased risk publicity by $5.1 million per yr
- Optimized inspection and maintenance plans, saving $1.2 million yearly
- Significantly lowered the possibility of lack of containment incidents
Dutch Utility Agency
A utility agency inside the Netherlands carried out a Proof of Concept (PoC) for RBM:
- Utilized to over 13,000 belongings in electrical and gasoline strategies
- Outcomes confirmed further setting pleasant and environment friendly repairs practices
- Most belongings required a lot much less frequent repairs
- Some belongings maintained the similar diploma or elevated repairs based on ambient conditions
- The company deemed the PoC worthwhile and decided to implement RBM all through your full group
Core Builder Machine Case Analysis
A look at on a core builder machine demonstrated some great benefits of integrating RBM with Worth of Unreliability (COUR) methods:
- Repairs intervals for essential components have been optimized:
- Heater: lowered from 24 days to 6 days
- Roll: lowered from 48 days to 13 days
- Conveyor: lowered from 48 days to 23 days
- Repairs costs decreased from $468,442 to $95,483 – a reduction of 79% in repairs costs
These case analysis exhibit that RBM can significantly improve repairs effectivity, worth low cost, and risk mitigation all through quite a few industries.
Courses Found
Companies found clear communication key to success. Teams wished to understand the model new risk-based technique, and training staff on risk analysis methods was important.
Information prime quality proved essential. Appropriate gear histories and failure info have been essential for good decision-making. Some firms needed to improve their info assortment first.
Many realized to start small and scale up. Beginning with pilot duties on essential gear helped refine the tactic, allowing for modifications sooner than full implementation.
Flexibility was very important. Hazard profiles modified over time.
Worthwhile companies generally evaluation and substitute their risk assessments.
Challenges and Choices
Implementing risk-based repairs comes with hurdles, nonetheless there are strategies to beat them. Companies can deal with frequent obstacles and improve their repairs strategies over time.
Overcoming Implementation Limitations
Resistance to differ is a significant issue when adopting risk-based repairs. Workers is also used to earlier methods and hesitant to be taught new ones.
To take care of this, companies must current clear teaching and current the model new system’s benefits.
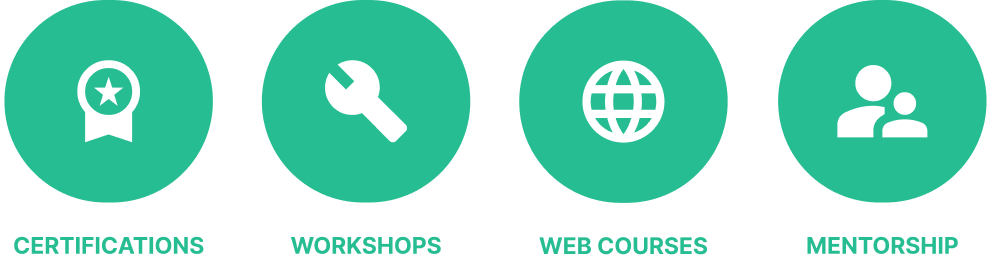
Information prime quality factors can hinder risk assessments. Incomplete or inaccurate info ends in poor picks. The reply is to spend cash on reliable info assortment devices and processes.
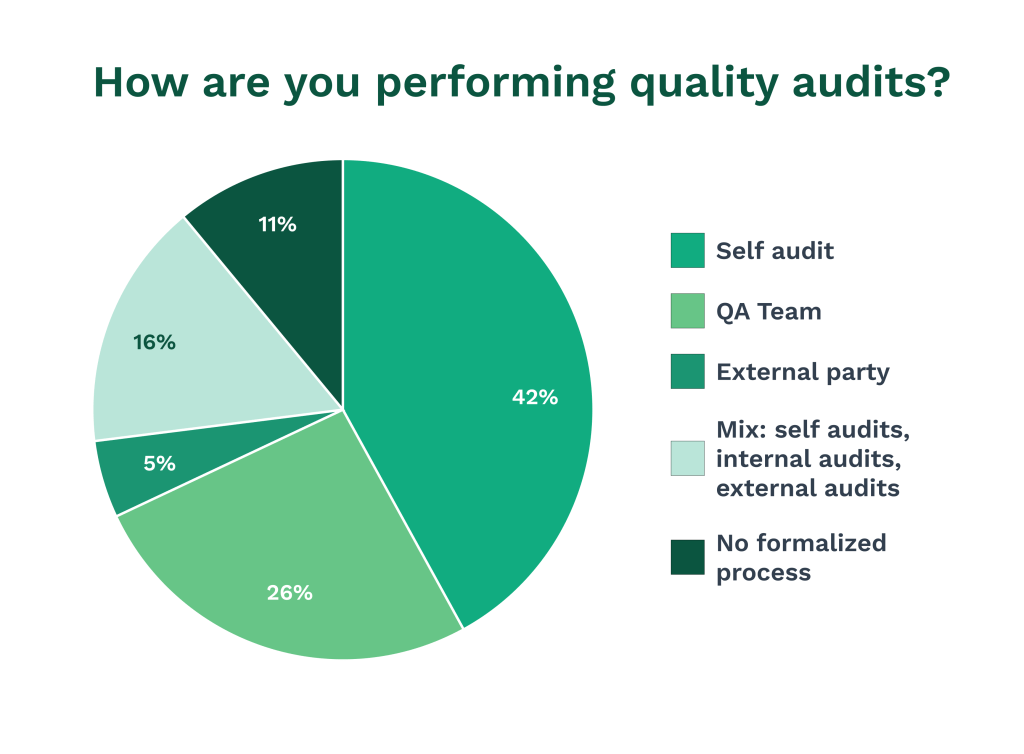
Helpful useful resource constraints usually limit implementation. Companies may lack time, money, or expertise. To beat this, start with small pilot duties and progressively enhance. Search help from outside specialists if wished.
Regular Enchancment and Adaptation
Hazard-based repairs needs ongoing refinement. Widespread course of evaluations help decide areas for enchancment. Organize ideas loops to gather enter from repairs teams and equipment operators.
Experience changes rapidly, so repairs strategies ought to protect tempo. Hold updated on new devices and methods. Attend commerce conferences and group with associates to be taught biggest practices.
Adjusting to altering enterprise needs is important. As manufacturing requires shift, so must repairs priorities. Assemble flexibility into the possibility analysis course of for quick updates when conditions change.
Measuring success helps drive enchancment. Monitor key effectivity indicators like gear uptime and maintenance costs. Use this info to fine-tune the risk-based technique over time.
Conclusion
Hazard-based repairs (RBM) is a superb technique to protect gear. It considers how in all probability points are to interrupt and the way in which unhealthy will probably be within the occasion that they did.
RBM helps companies think about what’s most important. This allows them to spend their time and money correctly on the machines that need it most.
This system makes use of knowledge to make picks. It’s not merely guessing or following a set schedule. RBM seems at appropriate particulars about every little bit of equipment.
Companies that use RBM can steer clear of large points. They kind issues sooner than they break down, preserving the workplace safer and stopping expensive shutdowns.